Was able to spend a little time down at the shop, and started working the 1/8" Cedar insert.
Removed the excess glue, and took down any ridges with a small Block plane. Then rolled the strongback and insert outside, for a quick sanding with 50 grit.
Back inside, I laid out a batten, on the insert, where I would trim at.
dusted off my old Japanese pull saw, and went to work.
Trimmed with an old Razor plane. The new ones aren't as good, but I love this old one ! I trim nearly all my football strips with this little plane. !
After trimming was complete, I dug out three scales The Digital conferred with one other, and the insert weighed in at 4 lbs 3 oz.
I hope Stripperguy is still around, and maybe comment of the weight difference between the foam he used on his Kite !
I figure I will shave a 1/4 lb off the insert after it is glued in place, scraping and sanding.
Then it was time to lay the insert in the hull. It fit like a glove ! Using my forms to make the insert was the secret !
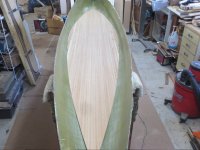
Next step I'll close the ends, and epoxy the insert to the hull.
I just want say that working with 1/8" strips was easy ! No beveling, or bead and cove, just edge glue ! Yes I used staples on the forms, but just the modified Spring clamps to hold the strips tight together !
I may even attempt a 1/8" strip build someday ! An easy hull design to strip up might be in line !
More later !
Jim