With the ends closed up it was time for the interior layer of kevlar. As usual I put the cloth in the stems first. I find this area to be fiddly and time consuming and I don't want to deal with it when doing the full layer. This gives me more time to work and and it's easier with the small pieces of cloth. I peel ply the edges for a pretty smooth transition and then overlap the main layer.
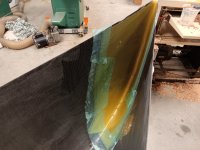
It was suggested I might want to add some ribs or reinforcement strips, especially where the seats will hang and at the center of the hull. This was good advice. Rather than running separate strips I instead laid the interior layer as 3 separate pieces with generous overlaps at the seat positions and center of the hull.
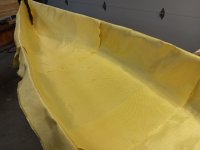
The actual wetting out of the inner Kevlar layer was, well, let's just say, interesting.
I think I mentioned earlier in this thread that I'm using up a lot of old cloth and other materials from when I was building a few years back. I did buy a 3 gallon kit of RAKA resin for my 2 current builds and this was pretty much gone but I had a new 1 quart kit of MAS epoxy that has been kicking around for about 5 years. I figured that would be enough and I was saving it for this interior layer.
Well, it wasn't enough after all. It also seemed to give less working time than the RAKA resin I'm used to.
I was about 1/2 done with the interior when I realized I was going to run out of resin. I had a little bit of RAKA left and I hoped that would finish it off. I concentrated on the center of the hull and left the stems dry.
The resin was starting to gel and I wasn't happy with the amount of air pockets scattered around the hull. I was having a hard time removing them. With the resin on the hull starting to gel it seems I was unable to either get the air out or get more epoxy in to fill the voids. I finally reached the point where I had to give up and finish wetting out the stems while I still could.
I mixed up the last few ounces of RAKA resin and I realized this was not enough to finish wetting out both stems. It did do one of them though.
Some quick rummaging found some more ancient epoxy from Adtech. It was thick with a fast setting hardener but it was all I had left and there was plenty of it to finish wetting out the other stem.
I'd cut up the very last of my peel ply into narrow strips and I placed these over the seam overlaps. The whole thing was not a pretty job.
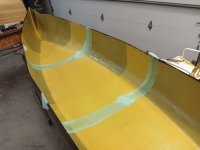
It's difficult to see in the picture but you can see the pale spots that indicate voids under the Kevlar. Many are along the transition area from foam to bare hull but there are plenty in other areas as well. Disappointing.
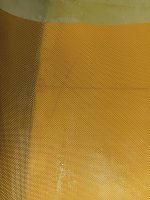
The good news is that the bottom of the hull feels rock solid now that the Kevlar layer is on top of the foam.
Alan
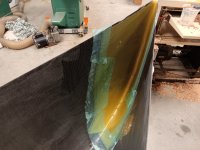
It was suggested I might want to add some ribs or reinforcement strips, especially where the seats will hang and at the center of the hull. This was good advice. Rather than running separate strips I instead laid the interior layer as 3 separate pieces with generous overlaps at the seat positions and center of the hull.
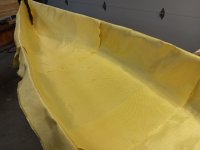
The actual wetting out of the inner Kevlar layer was, well, let's just say, interesting.
I think I mentioned earlier in this thread that I'm using up a lot of old cloth and other materials from when I was building a few years back. I did buy a 3 gallon kit of RAKA resin for my 2 current builds and this was pretty much gone but I had a new 1 quart kit of MAS epoxy that has been kicking around for about 5 years. I figured that would be enough and I was saving it for this interior layer.
Well, it wasn't enough after all. It also seemed to give less working time than the RAKA resin I'm used to.
I was about 1/2 done with the interior when I realized I was going to run out of resin. I had a little bit of RAKA left and I hoped that would finish it off. I concentrated on the center of the hull and left the stems dry.
The resin was starting to gel and I wasn't happy with the amount of air pockets scattered around the hull. I was having a hard time removing them. With the resin on the hull starting to gel it seems I was unable to either get the air out or get more epoxy in to fill the voids. I finally reached the point where I had to give up and finish wetting out the stems while I still could.
I mixed up the last few ounces of RAKA resin and I realized this was not enough to finish wetting out both stems. It did do one of them though.
Some quick rummaging found some more ancient epoxy from Adtech. It was thick with a fast setting hardener but it was all I had left and there was plenty of it to finish wetting out the other stem.
I'd cut up the very last of my peel ply into narrow strips and I placed these over the seam overlaps. The whole thing was not a pretty job.
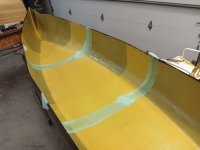
It's difficult to see in the picture but you can see the pale spots that indicate voids under the Kevlar. Many are along the transition area from foam to bare hull but there are plenty in other areas as well. Disappointing.
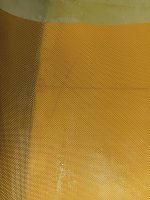
The good news is that the bottom of the hull feels rock solid now that the Kevlar layer is on top of the foam.
Alan