All done. 63 strips total. By the time I got to the last board I really had it figured out and then it was time to quit.
Initial setup:

20140703_001 by Alan Gage, on Flickr
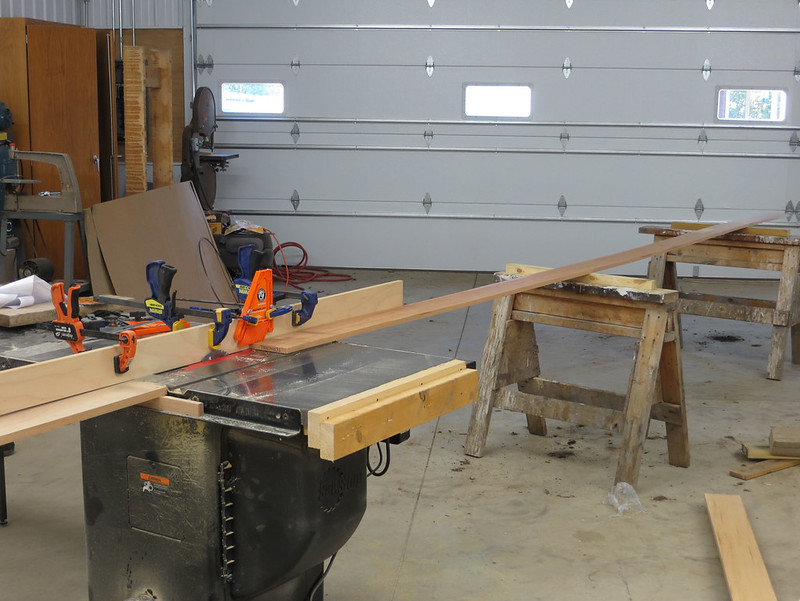
20140703_002 by Alan Gage, on Flickr
It didn't work too bad but it really bounced when the board came off the farthest sawhorse and then it drooped for a while, which lifted the board at the table saw and kept it from sliding nice and smooth. After the first board was done I laid a 2x6 between the sawhorses as a runway and topped it with a scrap piece of 1/4 melamine (slippery). This gave a nice smooth feed and made it very easy to adjust the tail left or right as needed while feeding. I don't know that the extended fence was really necessary.
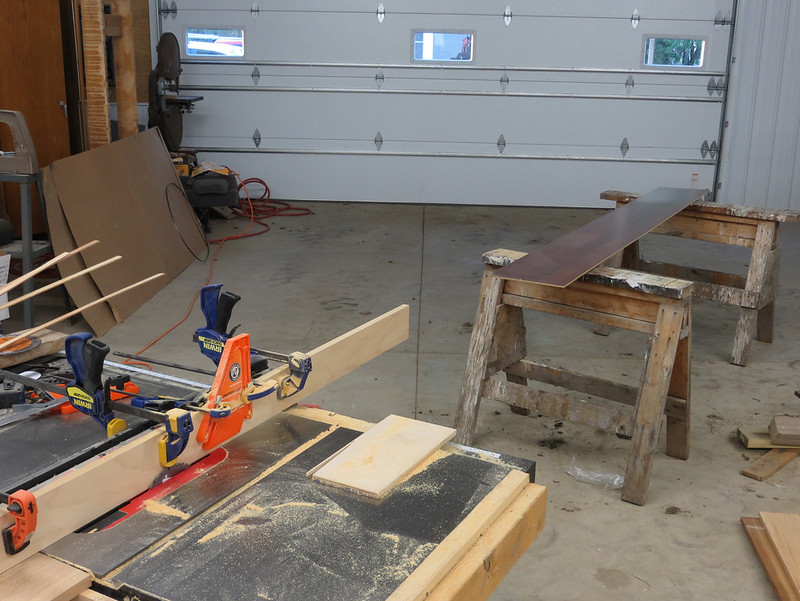
20140703_003 by Alan Gage, on Flickr

20140703_004 by Alan Gage, on Flickr
I found the best position was to stand at the table with my left hand a little behind the blade and using it to push the board tight against the fence. I didn't have to move it, just kept it in position and let the board slide past. A glove kept slivers and friction burns to a minimum. The right hand would reach behind me to grab the edge of the board and pull it through a couple feet before reaching back for another grip. My eyes could stay on the blade and fence the whole time to be sure it was staying tight against the fence. Like I said, by the time I got to the last board I had the system down and things were going very smoothly. A feather board would have accomplished the same thing but I didn't have one I could clamp to the table. And it would need to be reset every couple strips as the board got narrower.

20140703_005 by Alan Gage, on Flickr
Tomorrow morning I drive 4 hours round trip to pick up a new (to me) canoe. Then I take said canoe for a paddle if it's not raining. Then I bead and cove.
Alan
Initial setup:

20140703_001 by Alan Gage, on Flickr
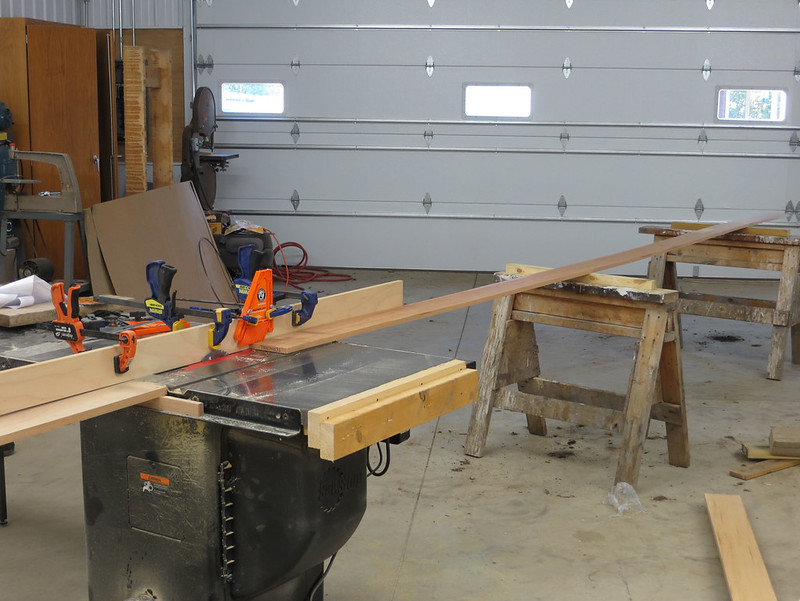
20140703_002 by Alan Gage, on Flickr
It didn't work too bad but it really bounced when the board came off the farthest sawhorse and then it drooped for a while, which lifted the board at the table saw and kept it from sliding nice and smooth. After the first board was done I laid a 2x6 between the sawhorses as a runway and topped it with a scrap piece of 1/4 melamine (slippery). This gave a nice smooth feed and made it very easy to adjust the tail left or right as needed while feeding. I don't know that the extended fence was really necessary.
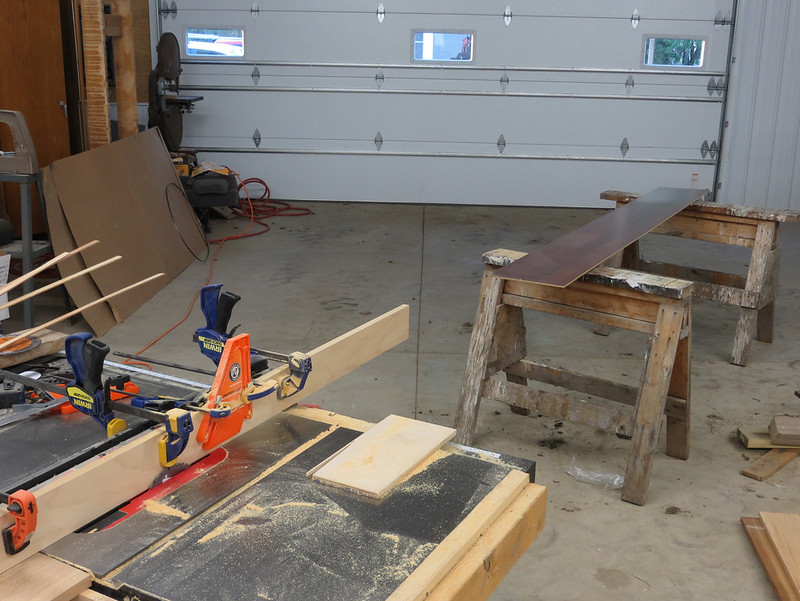
20140703_003 by Alan Gage, on Flickr

20140703_004 by Alan Gage, on Flickr
I found the best position was to stand at the table with my left hand a little behind the blade and using it to push the board tight against the fence. I didn't have to move it, just kept it in position and let the board slide past. A glove kept slivers and friction burns to a minimum. The right hand would reach behind me to grab the edge of the board and pull it through a couple feet before reaching back for another grip. My eyes could stay on the blade and fence the whole time to be sure it was staying tight against the fence. Like I said, by the time I got to the last board I had the system down and things were going very smoothly. A feather board would have accomplished the same thing but I didn't have one I could clamp to the table. And it would need to be reset every couple strips as the board got narrower.

20140703_005 by Alan Gage, on Flickr
Tomorrow morning I drive 4 hours round trip to pick up a new (to me) canoe. Then I take said canoe for a paddle if it's not raining. Then I bead and cove.
Alan
Last edited: