OK, I'm about done messing around with test panels and such.
I'd previously determined that the Larch could be sanded without gumming up the paper but I wanted to be certain that the epoxy would bond and I needed to try out the micro balloons to see if they would affect the bond and if the aesthetic change be tolerable.
In order to find out, I sanded 2 test panels and then wet out 4 oz e-glass w/ straight epoxy on one and, on the other, I wet out 4 oz e-glass with epoxy that was mixed 2/3 epoxy and 1/3 micro balloons. I was impressed with how well the micro ballooned epoxy wet out the glass and coverage was noticeably better (like, almost double... more than I'd expected from a 1/3 volume change).
Note: as you'll see in the pictures, I also experimented a little with burning the wood with a propane torch to enhance the grain & try a different appearance. I think burning might be an option for a later build if the wood used is unremarkable but I felt the Larch was prettier in its natural appearance. IMO it was worth trying but I'll not be burning this boat (at least, not until
after I portage it a few times)
I allowed the epoxy to cure about 5 days and then broke the panels on Sat night to see what what kind of adhesion I'd achieved and if the micro balloons affected the bond. I was very pleasantly surprised by how much pressure it took to break the panels and I actually had to jump up and down on them to get them to fail. (I know, not very scientific. I suppose I could calculate my body weight vs the area of the test panel vs the area of my footprint and then take into account the height of my jump, etc. but I don't feel like it. I jumped on it, it broke and I tried to pull the glass away from the wood... good 'nuff)
I found that I was tearing wood fibers away from the strips on both the micro balloon panel and the straight epoxy panel so I feel that good adhesion was achieved with both. The micro balloon cloth, when torn away, seemed much more flexible and felt softer but I assume this was due to the micro balloons themselves and the panel did not seem to be any easier or harder to break when I stepped on it. Like the un-micro ballooned panel, it held my full weight until I jumped up and down on it.
The deal-breaker for me was that the addition of the micro balloons did leave the glass with a slightly cloudy appearance... enough so that I won't be using them on this build. Given the extra coverage and the feel of the cloth I was able to rip off of the panel after breaking it, I feel fairly certain that they would provide a good bond with potentially significant weight savings but I prefer the look of wood and I'll accept the extra weight in order to enjoy the improved aesthetics.
For comparison, here's the straight epoxy panel
The rest of this afternoon was spent cutting some holes in the garage and building some heat runs to warm the upstairs of the garage. As winter tries to stage a comeback in my neck of the woods, it'll be nice to be able to warm the boat shop enough to cure epoxy. I should be able to get the forms set this week and, if all goes well, I should be milling strips next weekend.
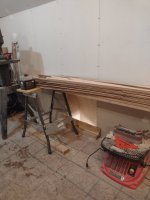