This post will cover off some of the finishing steps as we move to final fit and varnishing.
Normally, I would have completed the yoke by now and started finishing the gunnels ... but I "had an idea" and the router bit I ordered and require, is taking forever to get here, so the yoke is on hold and we move on with the seat and cleats.
The seat is actually in 2 parts, the seat and the cleats ...
First up is to get some rough cherry and rip some strips, they are shorter and the radial works just fine and is about the simplest setup I have for shorter strips. These have been marked before cutting and are assembled back in the same order as they were cut .... this eliminates the cutting irregularities that can occur when making multiple passes (such as strips)
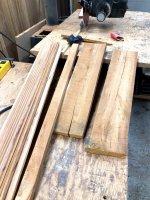
Hauled out the forms for the solo seat and decided they are 7 years old and I can do better now. The seat is comprised of 2 bent struts and 2 spacers, that are just solid material. the bent struts are steam bent, then epoxied using the same forms
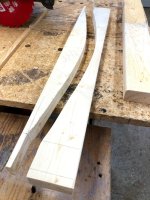
Made up the new template, front strut drops 2" and the rear drops 1"
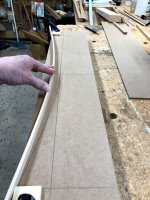
Rough cut with a jig saw and sanding to line on vertical sander
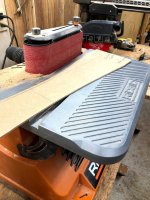
First side marked and rough cut, it will now be sanded to the line
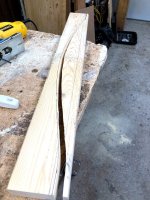
New 2 x 4 , line is offset the width of the strips ( 1.125" ) to the mating form
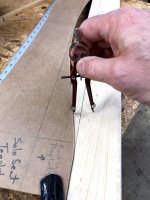
Mating form shape drawn in
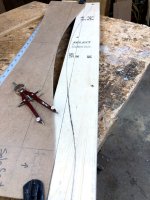
2 halves joined and they fit very well, the reason I used 2 separate pieces to make the forms was to have a little more meat for clamping .. just splitting a single leaves one a bit thin and I didn't have a 2 x 6 on hand. It doesn't look like they fit exactly and this was the point of using the offset to do the second part, they shouldn't fit, close but not exact. When the 1.125" of strips are added they will be a perfect match for the job.
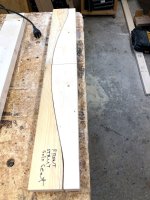
Assembled into a clamping form, the center line is marked on both halves, small blocks are added to keep the form aligned (they tend to wander otherwise).

Strip stack is assembled and a 1/8" hole drilled in one end
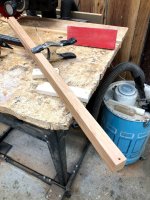
and then loaded into the steamer
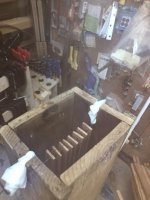
When they are medium rare, they are quickly loaded and clamped up, the form also allows a quick clampup, since you get on the order of 30 seconds to get the operation done, with the first 15 seconds being "prime" for bending, it is important to have your setup be quick and easy
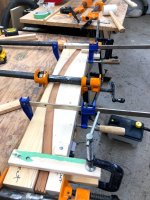
They sit for a day in the mold, then it is opened and the strips allowed to dry for a day. Then it is the epoxy regime, saturate with unthickened, butter with thickened, then clamp up .... gently. Just make sure all of the gaps are closed up, you don't need to overdo this ... you want to leave enough epoxy in the joint.
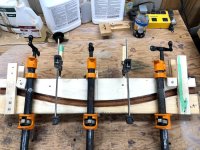
The centerline is transferred to the glue up as well
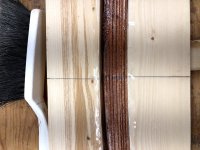
A point about the glue up, you can see that I like to tint the epoxy dark ... your choice is to try and hide the joint with a good match to colour or you can contrast with a whole different colour. If you try and use colourless or neutral (just cabosil) you get a black line that shifts with the light, that is the joint shadow as light enters the joint. The "close" colour match is tough at the best of times, so I prefer to just go with higher contrast and use the joint as a "feature".
I point this out to make the point that there are options in the joinery, selective use of contrasting epoxy joints can be quite visually pleasing IMO
A note on the form, you will also see an extra strut in the middle of the form, I added that because the middle strips wanted to shift and I needed a surface to push down on to keep them aligned.
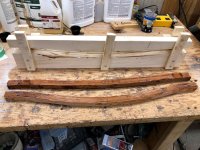
Struts get scraped and a quick pass through the planer to make it flat on both sides, here a "cleaned up" strut goes back in the form to re establish that centerline
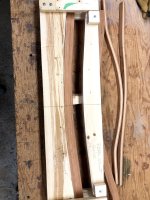
The sides of the seat where cut from some rough 1" cherry and left rough to keep the piece full width. They were sized to be slightly thicker than the struts, since the seat struts are not the same shape, the sides need to be shaped some, so leaving a little extra allows fitting as we move forward.
A mortise is made about 3" in from the ends of the struts, all laid out from this center line that was established in the mold. The mortises are 3/8" deep and slightly angled to fit the seat bend at that point.
Here you can see the bottom view of the initial setup with squares and the pilot screw holes, that allow for temporary assembly. You can see that the extra bit at each joint and that it isn't an equal amount along the piece.
The screws are not going to be the permanent fastener. I use them as an easy clamping and alignment tools for fitting and epoxy glue up, then i bore out the holes and add dowels as the final step.

This a "top up" view once it has been assembled with the screws, again the extra bit and it isn't equal along it's length

A closeup of the extra bit, the area to be removed is marked with a pencil, at both sides
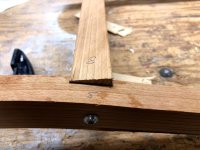
The side piece is removed, the pencil mark side to side is joined .... this gives a very clear picture of what needs to be removed to make the fit work
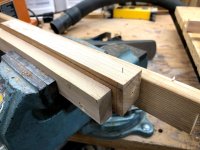
While the piece is free, an arc is scribed to remove some material from the bottom. The piece was made wider to accommodate the weaving and the arc will add a nice look while reducing the weight
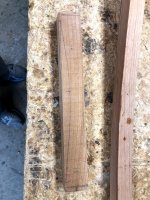
The adjustments bring the sides very close to fitting
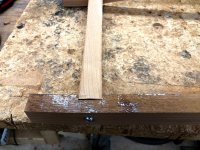
A bit of trimming and sanding and they fit nicely
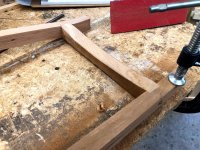
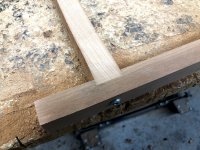
The seat is ready for assembly, I like to continue with the screws as it gives me a very simple clamping system. HOWEVER, if you do this ... make sure you wax the screws ... if you don't the screws will end up epoxied in and there will no way to remove them.
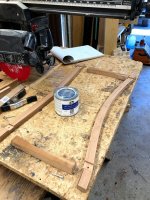
Saturated joints
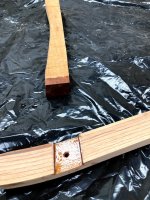
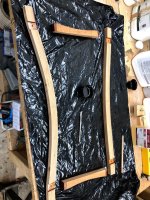
Thicken and tint the remaining epoxy, I used some walnut, cherry and the cabosil to lighten it a bit, assemble with the WAXED screws and snug them up till the joints are just snug. Use a gloved finger or a paper towel to remove the "squeeze out", it is a lot easier to do this now than later. It will leave you with a joint that just needs a little cleanup.
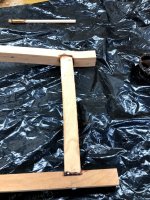
Once the epoxy is cured (usually next day for me), cleanup the joints and do a light sanding.
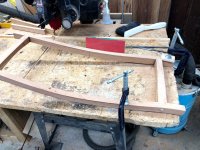
Remove the screws and bore holes for the dowels. I like to use forstner bits to get a clean edge, so a guide is needed to keep the bit from wandering due to the screw hole. I just use a piece of scrap strip and do as follows
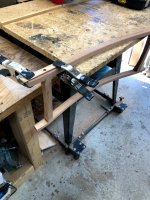
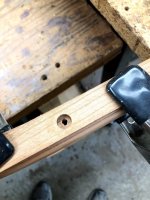
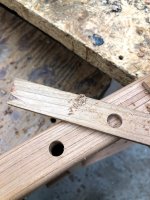
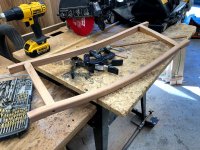
Epoxy in the dowels, in this case I used 3/8" x 2" maple dowels
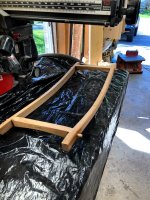
Trim and sand the next day
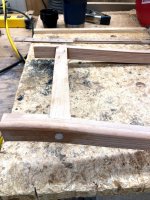
The basic seat frame is done, so now the cleats need to be made up to fit.
The seat location along the hull has already been established on the gunnels, I also know how far off the bottom I want the seat to sit, so I need to mark the location accurately side to side and mark out where the cleats will sit.
The gunnels are adjusted to be level, then a jig like this is positioned, tape is added in about the right location, so i can mark both sides with a reference location at the bow end of the seat, once this is done, I mark the stern end.
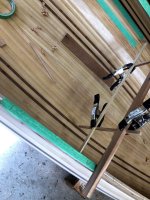
Once you have a reference top line for the cleat, the rest is pretty easy to pencil in a the cleat foot print, then outline that in tape
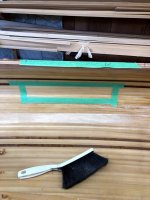
The complete seat cleat has 3 pieces, a 2" x 14" x 7/16" base and 2 3" x 3" x 7/8" blocks, 7 if you count the 4 dowels
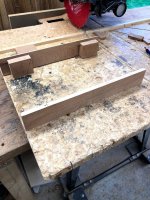
Mark up the center of each of the blocks, and draw in the triangular shape, use the completed seat frame to determine the centerline on the base for each of the blocks, leaving equal leftover at each end. You can do this empirically with the seat frame or by measuring, this is "in progress". The holes have screws holding from the back.
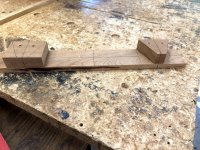
The triangles can be cut on pretty much any saw, I freehanded them on my radial. Again for looks and to trim some weight, you can see arches drawn in on the base
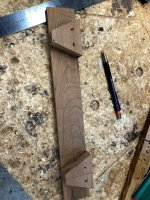
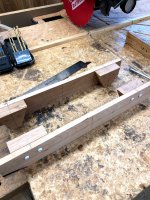
Ready for assembly
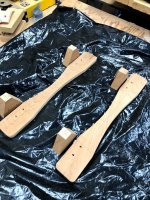
Epoxy up ..... first pic shows squeeze out, then clamping and finished, make sure to wipe up the joints once they are clamped. In this case, I removed the screws after about an hour, there was sufficient clamping and I had neglected to wax the screws ...
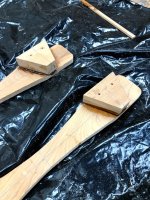
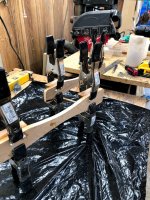
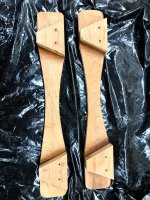
At this point the cleats need to be fitted to the irregular shape of the boat ... they are flat, the boat isn't. This is not a process that is easy to explain, but basically, put the cleat in place, see where wood needs to be removed. Do a bit, fit a bit and in about 20 minutes, you will have a good fitting cleat. Don't try and do too much in one go, it is definitely a "do a little at a time" process. Once you have the fit done, make some alignment marks on the tape and cleat
Once you have the backs fitted, it's time to fix those screw holes, bore them out and epoxy in the dowels
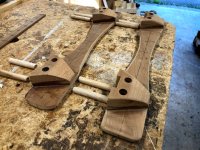
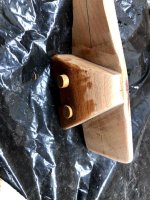
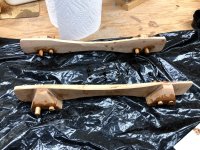
Trim the dowels, and sand out the facing areas .... leave the fitted area alone, except to cleanup the dowel area.
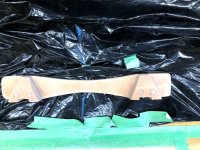
Sand up the taped area on the boat, well, then wet out the boat and cleat backside ... keep adding epoxy to the cleat as required for a few minutes, then remove excess with brush. Thicken your epoxy and thickly butter the cleat back side and carefully position using those alignment marks.
You may need to get a little creative with the clamping.
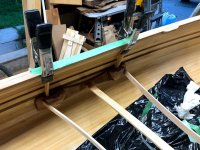
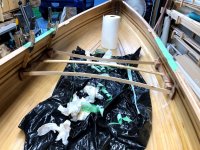
However you clamp, do a dry run first to make sure it will work, make provision for sliding, sometimes they want to, sometimes they don't. The above pictures are after about 2 hours. Once you have the cleat secured, cleanup all around and remove all the squeeze out you can, then go carefully around with a paper towel to get rid of the rest.
At about the 1 hour mark, the cleat shouldn't move and the epoxy will be well kicked, remove the surrounding tape ... if you leave it, the edge will be epoxied to the hull and you will have to clean it up .... if you haven't guessed yet, I don't like cleaning up epoxy if I don't have to.
And you now have an installed set of cleats

The seat was placed in the boat and the bolt holes were bored through the seat strut to the matching cleat, drilling about 3/4" into the cleat. This ensures that the holes will line up .... well, I also sized the hole to the bolt and dropped a bolt in each hole as I went, so that insured they would line up.
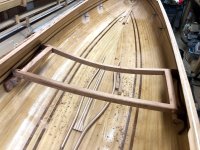

Using this sort of cleat, in a lowered seat configuration and tumbleholm has a few issues, one of the most important is that it is very difficult to drill straight down through a cleat, so you are left with an angled hole with no exit.
Enter Helicoils or steel inserts
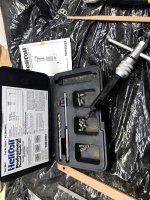
This is an insert kit, comprised of a drill bit, a tap, an insertion tool and of course the inserts themselves, the ones I am using are the purple/pink coloured ones. They are 12 mm M6-1 locking inserts ...
Step 1, use the tap to cut threads in the cleat hole
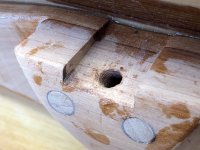
Saturate the hole thread with epoxy, be careful here, you want the threads wet, but no more. Load the insertion tool with the insert and screw it into the threaded hole
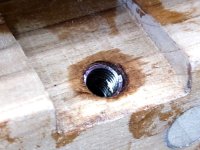
You now have a M6-1 threaded hole, that will lock the bolt when it gets turned in. If you look at the pic, you can see the "loc", it is the flat area which will bind on the bolt. You can still remove the bolt, but it won't loosen by itself.
The cleat is now sanded and a coat of epoxy added, careful not to add any epoxy to the threaded hole.
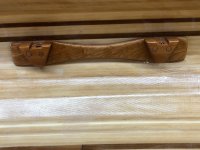
At this point the seat frame is assembled, the cleats and bolting system is installed, the seat will be finished (sanding/varnish/weaving) and won't go back in the boat until after varnishing.
This is more than usual for a single post, I will break seat finishing into a separate post.
Brian
Normally, I would have completed the yoke by now and started finishing the gunnels ... but I "had an idea" and the router bit I ordered and require, is taking forever to get here, so the yoke is on hold and we move on with the seat and cleats.
The seat is actually in 2 parts, the seat and the cleats ...
First up is to get some rough cherry and rip some strips, they are shorter and the radial works just fine and is about the simplest setup I have for shorter strips. These have been marked before cutting and are assembled back in the same order as they were cut .... this eliminates the cutting irregularities that can occur when making multiple passes (such as strips)
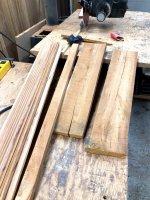
Hauled out the forms for the solo seat and decided they are 7 years old and I can do better now. The seat is comprised of 2 bent struts and 2 spacers, that are just solid material. the bent struts are steam bent, then epoxied using the same forms
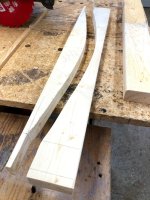
Made up the new template, front strut drops 2" and the rear drops 1"
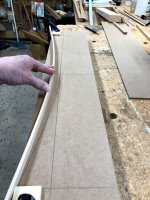
Rough cut with a jig saw and sanding to line on vertical sander
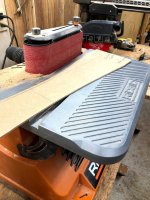
First side marked and rough cut, it will now be sanded to the line
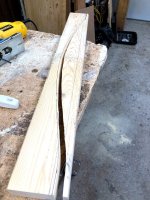
New 2 x 4 , line is offset the width of the strips ( 1.125" ) to the mating form
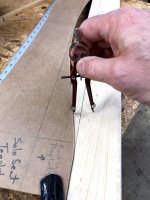
Mating form shape drawn in
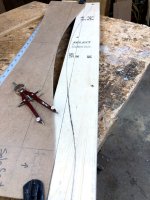
2 halves joined and they fit very well, the reason I used 2 separate pieces to make the forms was to have a little more meat for clamping .. just splitting a single leaves one a bit thin and I didn't have a 2 x 6 on hand. It doesn't look like they fit exactly and this was the point of using the offset to do the second part, they shouldn't fit, close but not exact. When the 1.125" of strips are added they will be a perfect match for the job.
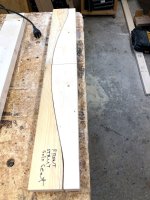
Assembled into a clamping form, the center line is marked on both halves, small blocks are added to keep the form aligned (they tend to wander otherwise).

Strip stack is assembled and a 1/8" hole drilled in one end
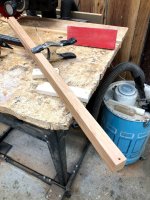
and then loaded into the steamer
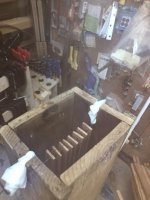
When they are medium rare, they are quickly loaded and clamped up, the form also allows a quick clampup, since you get on the order of 30 seconds to get the operation done, with the first 15 seconds being "prime" for bending, it is important to have your setup be quick and easy
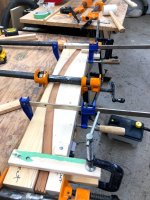
They sit for a day in the mold, then it is opened and the strips allowed to dry for a day. Then it is the epoxy regime, saturate with unthickened, butter with thickened, then clamp up .... gently. Just make sure all of the gaps are closed up, you don't need to overdo this ... you want to leave enough epoxy in the joint.
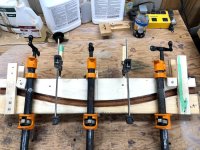
The centerline is transferred to the glue up as well
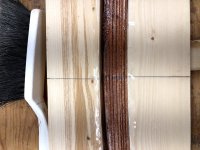
A point about the glue up, you can see that I like to tint the epoxy dark ... your choice is to try and hide the joint with a good match to colour or you can contrast with a whole different colour. If you try and use colourless or neutral (just cabosil) you get a black line that shifts with the light, that is the joint shadow as light enters the joint. The "close" colour match is tough at the best of times, so I prefer to just go with higher contrast and use the joint as a "feature".
I point this out to make the point that there are options in the joinery, selective use of contrasting epoxy joints can be quite visually pleasing IMO
A note on the form, you will also see an extra strut in the middle of the form, I added that because the middle strips wanted to shift and I needed a surface to push down on to keep them aligned.
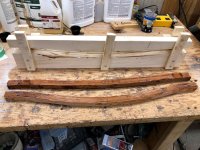
Struts get scraped and a quick pass through the planer to make it flat on both sides, here a "cleaned up" strut goes back in the form to re establish that centerline
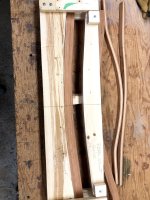
The sides of the seat where cut from some rough 1" cherry and left rough to keep the piece full width. They were sized to be slightly thicker than the struts, since the seat struts are not the same shape, the sides need to be shaped some, so leaving a little extra allows fitting as we move forward.
A mortise is made about 3" in from the ends of the struts, all laid out from this center line that was established in the mold. The mortises are 3/8" deep and slightly angled to fit the seat bend at that point.
Here you can see the bottom view of the initial setup with squares and the pilot screw holes, that allow for temporary assembly. You can see that the extra bit at each joint and that it isn't an equal amount along the piece.
The screws are not going to be the permanent fastener. I use them as an easy clamping and alignment tools for fitting and epoxy glue up, then i bore out the holes and add dowels as the final step.

This a "top up" view once it has been assembled with the screws, again the extra bit and it isn't equal along it's length

A closeup of the extra bit, the area to be removed is marked with a pencil, at both sides
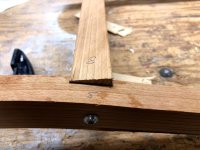
The side piece is removed, the pencil mark side to side is joined .... this gives a very clear picture of what needs to be removed to make the fit work
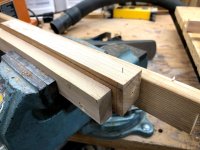
While the piece is free, an arc is scribed to remove some material from the bottom. The piece was made wider to accommodate the weaving and the arc will add a nice look while reducing the weight
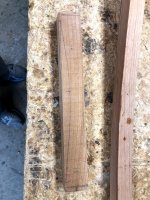
The adjustments bring the sides very close to fitting
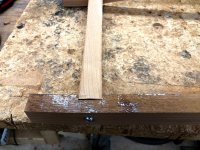
A bit of trimming and sanding and they fit nicely
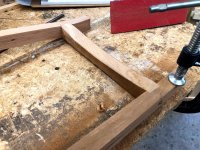
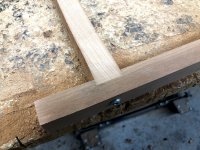
The seat is ready for assembly, I like to continue with the screws as it gives me a very simple clamping system. HOWEVER, if you do this ... make sure you wax the screws ... if you don't the screws will end up epoxied in and there will no way to remove them.
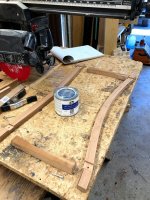
Saturated joints
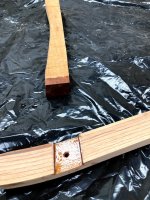
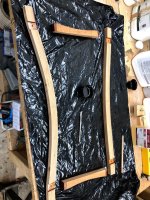
Thicken and tint the remaining epoxy, I used some walnut, cherry and the cabosil to lighten it a bit, assemble with the WAXED screws and snug them up till the joints are just snug. Use a gloved finger or a paper towel to remove the "squeeze out", it is a lot easier to do this now than later. It will leave you with a joint that just needs a little cleanup.
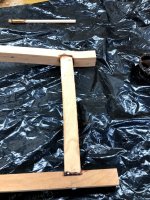
Once the epoxy is cured (usually next day for me), cleanup the joints and do a light sanding.
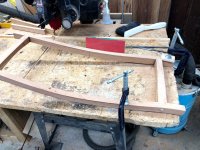
Remove the screws and bore holes for the dowels. I like to use forstner bits to get a clean edge, so a guide is needed to keep the bit from wandering due to the screw hole. I just use a piece of scrap strip and do as follows
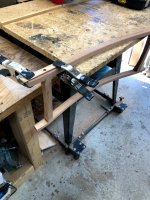
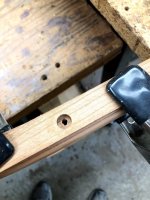
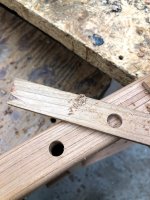
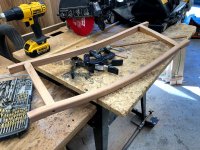
Epoxy in the dowels, in this case I used 3/8" x 2" maple dowels
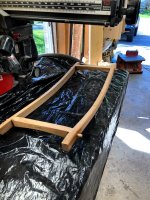
Trim and sand the next day
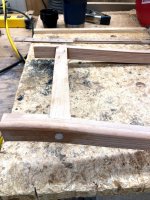
The basic seat frame is done, so now the cleats need to be made up to fit.
The seat location along the hull has already been established on the gunnels, I also know how far off the bottom I want the seat to sit, so I need to mark the location accurately side to side and mark out where the cleats will sit.
The gunnels are adjusted to be level, then a jig like this is positioned, tape is added in about the right location, so i can mark both sides with a reference location at the bow end of the seat, once this is done, I mark the stern end.
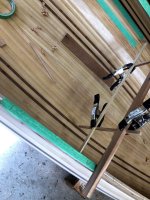
Once you have a reference top line for the cleat, the rest is pretty easy to pencil in a the cleat foot print, then outline that in tape
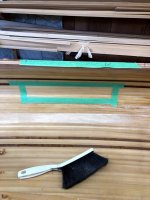
The complete seat cleat has 3 pieces, a 2" x 14" x 7/16" base and 2 3" x 3" x 7/8" blocks, 7 if you count the 4 dowels
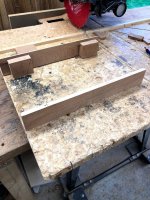
Mark up the center of each of the blocks, and draw in the triangular shape, use the completed seat frame to determine the centerline on the base for each of the blocks, leaving equal leftover at each end. You can do this empirically with the seat frame or by measuring, this is "in progress". The holes have screws holding from the back.
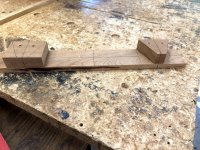
The triangles can be cut on pretty much any saw, I freehanded them on my radial. Again for looks and to trim some weight, you can see arches drawn in on the base
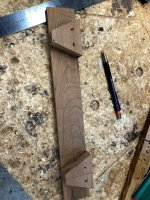
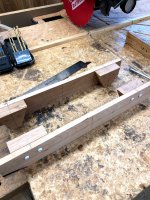
Ready for assembly
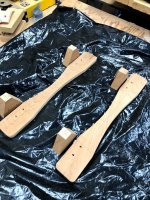
Epoxy up ..... first pic shows squeeze out, then clamping and finished, make sure to wipe up the joints once they are clamped. In this case, I removed the screws after about an hour, there was sufficient clamping and I had neglected to wax the screws ...
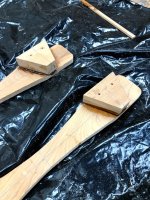
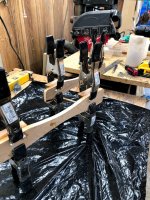
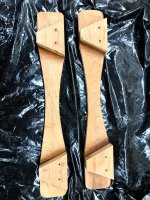
At this point the cleats need to be fitted to the irregular shape of the boat ... they are flat, the boat isn't. This is not a process that is easy to explain, but basically, put the cleat in place, see where wood needs to be removed. Do a bit, fit a bit and in about 20 minutes, you will have a good fitting cleat. Don't try and do too much in one go, it is definitely a "do a little at a time" process. Once you have the fit done, make some alignment marks on the tape and cleat
Once you have the backs fitted, it's time to fix those screw holes, bore them out and epoxy in the dowels
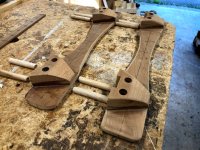
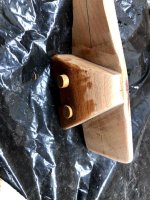
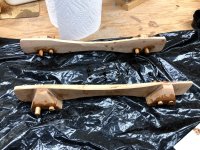
Trim the dowels, and sand out the facing areas .... leave the fitted area alone, except to cleanup the dowel area.
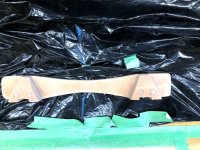
Sand up the taped area on the boat, well, then wet out the boat and cleat backside ... keep adding epoxy to the cleat as required for a few minutes, then remove excess with brush. Thicken your epoxy and thickly butter the cleat back side and carefully position using those alignment marks.
You may need to get a little creative with the clamping.
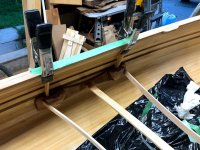
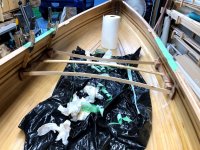
However you clamp, do a dry run first to make sure it will work, make provision for sliding, sometimes they want to, sometimes they don't. The above pictures are after about 2 hours. Once you have the cleat secured, cleanup all around and remove all the squeeze out you can, then go carefully around with a paper towel to get rid of the rest.
At about the 1 hour mark, the cleat shouldn't move and the epoxy will be well kicked, remove the surrounding tape ... if you leave it, the edge will be epoxied to the hull and you will have to clean it up .... if you haven't guessed yet, I don't like cleaning up epoxy if I don't have to.
And you now have an installed set of cleats

The seat was placed in the boat and the bolt holes were bored through the seat strut to the matching cleat, drilling about 3/4" into the cleat. This ensures that the holes will line up .... well, I also sized the hole to the bolt and dropped a bolt in each hole as I went, so that insured they would line up.
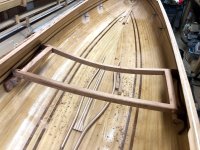

Using this sort of cleat, in a lowered seat configuration and tumbleholm has a few issues, one of the most important is that it is very difficult to drill straight down through a cleat, so you are left with an angled hole with no exit.
Enter Helicoils or steel inserts
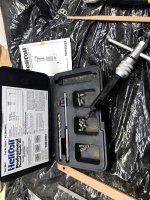
This is an insert kit, comprised of a drill bit, a tap, an insertion tool and of course the inserts themselves, the ones I am using are the purple/pink coloured ones. They are 12 mm M6-1 locking inserts ...
Step 1, use the tap to cut threads in the cleat hole
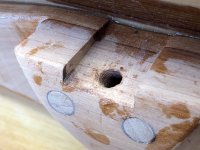
Saturate the hole thread with epoxy, be careful here, you want the threads wet, but no more. Load the insertion tool with the insert and screw it into the threaded hole
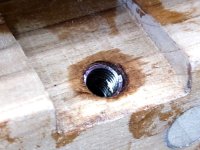
You now have a M6-1 threaded hole, that will lock the bolt when it gets turned in. If you look at the pic, you can see the "loc", it is the flat area which will bind on the bolt. You can still remove the bolt, but it won't loosen by itself.
The cleat is now sanded and a coat of epoxy added, careful not to add any epoxy to the threaded hole.
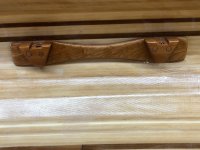
At this point the seat frame is assembled, the cleats and bolting system is installed, the seat will be finished (sanding/varnish/weaving) and won't go back in the boat until after varnishing.
This is more than usual for a single post, I will break seat finishing into a separate post.
Brian