Here's a quick update, mostly pictures. This project is coming to a close now. I have to say that I'm a bit surprised at the time and effort it took to build a decked canoe compared to a regular open canoe. From where I'm at, I think this is easily double the effort of an open canoe. The cockpit coaming structure is a big part of the extra effort, but a boat with two halves is like building two boats. The coaming rim alone was a significant number of steps and is not the equivalent of making and installing gunwales. I attached a link down below to a video I made of all the steps in building the coaming rim for anyone interested.
Enjoy! Mark
For the coaming rim, I ripped 3/16" strips of spruce and planed them down to about 5/32". After that, I cut them in half to make strips 3/8" wide, which was the starting thickness of the rim. I decided to make a form to bend them instead of doing it on the boat in case the heat had an effect on the curing epoxy. For a steamer I used some plastic tubing sent to me by one of the members on here, but I can't remember who it was. The tubing was hooked to an old kettle with radiator hose. It worked great. I bent the stems this same way, and is now my preferred way to bend gunwales and anything these days. The steam box doesn't work nearly as well. I might have been able to bend these strips using a heat gun, but the spruce is pretty dry and I didn't want to take any chances.
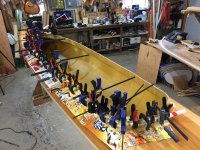
After drying, the bent strips were put in place on the canoe. I removed clamps in the center third and brushed epoxy all over the top of the strips. Then I worked epoxy into the spaces between the strips. I clamped that section and did the same to the front and rear. I used a heat gun to get the epoxy to flow into all the nooks and crannys at the end and let it set overnight.
After doing the second side, the rim was ready to be installed on the canoe using thickened epoxy.
While the epoxy was setting on the rim, I used the time to experiment with the seat riser configuration and came up with this. I'll probably only ever use the center height, but there are two more just in case an adjustment is ever needed. Who knows.
These are just the temporary seat risers, but I decided to put some leftover glass on each side to make them usable. They seemed a bit too flexible with glass only on one side.
These are the panels I'll use for the final seat risers once I get some time in the temporary set. These are made of 1/4" birch plywood. Supposedly the glue is waterproof. I put carbon on each side and a layer of 4 oz glass. These 12 x 24" panels are really stiff and surprisingly heavy.
Back to the coaming lip. I trimmed the first side and laid second side on like this.
The Stern
Coaming rim on and trimmed
I put a heavy bead of thickened epoxy under the rim for support and to get the glass to wrap around the sharp edge.
OK, I'm skipping pictures of a big part of the operation. I routed the inside edge using a roundover bit. The kevlar fuzzed up like crazy and dusted the shop with kevlar dust. I used a respirator during that part of the operation. I was able to use coarse sandpaper to remove most of the fuzz, but it ended up getting glassed over anyway, so was no problem. I also rounded over the outside edge using a block plane and sandpaper. I put 2 layers of 4 oz glass over the rim, which wrapped from below the fillet to up and over most of the way down the kevlar. That rim is strong as hell now, and I don't think I can break it. With all the overlaps, the coaming riser has 1 layer of kevlar on the inside in addition to 3 layers of 4 oz glass. The outside has 4 layers of glass. Crazy!
Here is a link to the video of making the coaming rim:
I decided that I want to have the seat riser removable, so I installed a couple of cleats on the floor in line with the coaming riser. These were epoxied down and then some 4oz glass was laid at the joint on either side of the cleat.
Temporary seat risers are installed with one of my seats. I'll probably add one or two more screws/bolts to these at each joint.
The jet propulsion system will need some fancy exhaust tips near the stern. I made these out of ash, but they'll be lined so they don't burn. They're a bit bright, so I'll probably stain them to tone it down a bit. Another option is to paint flames on them which I'm considering. As rudder cable exit points they're a bit overkill, but it's too late since they're already glued on.
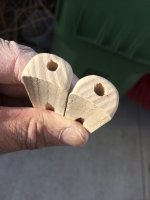
Here's what they looked like prior to installation. I had to go out and buy a 12" - 3/16" drill bit to get the angle to drill through these and into the hull.
And finally the test sit. There I am, not feeling so well these days, but happy that I'm where I'm at with this build. I just need to install the foot braces and run the rudder cables and this canoe can be put on the water which I'll be looking to do in a couple weeks. The problem is that open water is difficult to find in Montana at this time of year. I'm willing to drive, so who knows where I'll end up.
Mark