Cockpit opening and Coaming
I traced out the cockpit opening from the Sea Wind onto craft paper and used some battens to fair out the curves. I put down some masking tape and followed the line on one side and flipped it over for the other.
I used a jigsaw to cut out the hole. I got a little tear out on the bottom before I realized I shouldn't be cutting into the grain. It will all sand out and be covered anyway, so no big deal.
I'm using the same method to build the coaming riser that Deerfly used in his build. It just involves stripping the coaming all the way around the cockpit opening. It sounds a bit tedious, but for some reason my brain really enjoys this type of thing. It took a total of 270 strips between 3 and 3-3/4" long to get all the way around. I used about 70 linear feet of 3/4" bead and cove strip.
I used some birch dowel to get things started at the bow, then it's off to the races. Once you get the hang of it the whole process goes quickly.
later that day..........................
I removed some of the forms to make things a bit easier, and notice how I had to notch the remaining forms to make room for the riser strips.
Here's a short video I made showing how it's done.
Sanded and ready to be glassed.
First I added a filet of thickened epoxy so the glass could make the tight bend. Being a bit skeptical at how strong this will be, I ended up using 6 oz glass for the first layer, and added another layer of 4 oz. This boat will be transported upside down with the coaming on the rack, and I want the coaming to have a chance at surviving the weight of me falling on it. Don't worry, the riser will be trimmed down below where the glass ends.
I finally was able to use Nick Schade's method of overlapping a glass layer onto masking tape, then using a razor blade to trim when things are still a bit soft. I have to say that I like the clean edge it leaves without all the little straggling fibers. This will save some work later on, which I am really trying to do on this build.
OK, another money shot of the deck and hull together. I know, that coaming looks pretty tall, but it will be trimmed down to about 2" all the way around and will grade a little higher towards the bow. It looks like I've got about 1/4 to 3/8" more total length in the hull, so I'm going to have to do some trimming after putting the two halves together.
I was originally worried about the strength of a coaming built with vertical cedar strips, but it's pretty rigid now. With a layer of kevlar and glass on the inside of the coaming I think it will be bomb proof.
Next, sanding and glassing the insides of both halves.
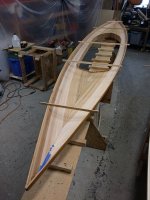