Hi canoe builders, wanabee builders and other people that like this kind of stuff.
I've been meaning to start a thread for some time with my first attempt at building a solo cedar strip canoe. Starting about a year ago, I got to thinking it was time for me to build a canoe. I friend in Idaho built one a few years back, and though I didn't get to participate in the build, I got to see the finished product. He is quite the woodworker, so at the time I thought it was a little outside my ability. After I found this forum a little over a year ago I saw there were lots of different methods to get to the same place. In the end it took me many months to decide on a boat, and in the end settled on the John Winters Kite. I was looking for a do-it-all type boat that could be used for a wide variety of conditions. I live next to the Yellowstone River, so the boat needs to handle some decent sized waves, but also be good for big lake travel and acceptable in portage and paddle country. I plan to build the boat a little heavy so it can withstand some knocks on rocks.
I started on this in mid-February, just working occasional evenings. Lately I've been at it full time with a few extended breaks. I'm actually well in to the build at this point and am about ready to pull the boat off the forms, but I'll trickle out photos until I catch up to the real-time build. Thanks to all the other forum members who build canoes and share their methods on this forum. Another Kite Canoe build is in recognition of Stripperguys Kite build that I've looked through a few dozen times in the last couple months, Thanks!
This canoe will not be my first boat build. I made a skin kayak last year, finishing it during the winter and took these photos on a cold, windy day in early March on a local lake. I was surprised the lake wasn't frozen.
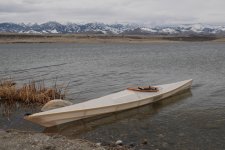
Who cares about kayaks though? On to the canoe build........
First, I cut all the strips using a skilsaw. Thanks Jim Dodd for all the details. My brother, a woodworker, couldn't believe how nice and uniform these came out. Oh, wait, the first step was to build a strongback. I bought 2 - 16", 16 foot I-beams for $50, screwed them together and used some old concrete soaked boards from last summers project (see, I'm standing on it) for the legs. The I-beams are straight as an arrow and really light too.
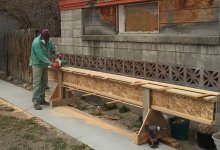
Very Nice! I'm very happy with this method.
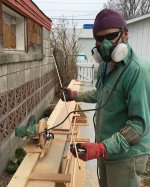
It took me half a day, including setup and takedown, to cut almost enough strips for 2 canoes. When I was collecting wood for this project I kept finding nice 8 and 12 foot boards when visiting lumber yards in the region so I would buy them. I did buy a few 16 foot boards for full price though.
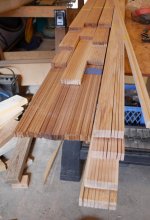
About this same time I cut all the forms from the plans I bought from Green Valley Canoe. I used 5/8" particle board. Here's a photo of my steaming setup and the stems being formed. I plan to use only inner stems made from cedar. I would have just built this stemless, but the plans didn't have stemlines for stemless construction. Since this is my first build I thought it best to stay with the plan. Note the old Wenonah looking on wondering what's up with all this.
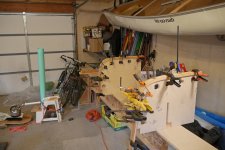
Next up is the bead and cove on the cedar strips. I have one of the cheapest router tables ever made, but it was certainly up to the task once I figured out how to attach the featherboards. This operation took me a full 9 hours, including setup and takedown, which I was determined to do all in one go. It started snowing near the end of this process. I wish I had pictures of the sawdust all over the snow.
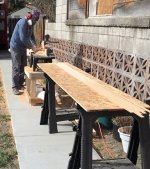
I ended up with a nice pile of beaded and coved strips, almost enough for 2 boats. Every one of them was spot on in dimensions. Needless to say, I was quite pleased with how well this part of the project went.
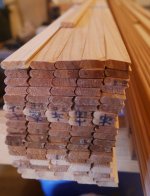
OK, that's enough for today. I'll make another post soon.
I've been meaning to start a thread for some time with my first attempt at building a solo cedar strip canoe. Starting about a year ago, I got to thinking it was time for me to build a canoe. I friend in Idaho built one a few years back, and though I didn't get to participate in the build, I got to see the finished product. He is quite the woodworker, so at the time I thought it was a little outside my ability. After I found this forum a little over a year ago I saw there were lots of different methods to get to the same place. In the end it took me many months to decide on a boat, and in the end settled on the John Winters Kite. I was looking for a do-it-all type boat that could be used for a wide variety of conditions. I live next to the Yellowstone River, so the boat needs to handle some decent sized waves, but also be good for big lake travel and acceptable in portage and paddle country. I plan to build the boat a little heavy so it can withstand some knocks on rocks.
I started on this in mid-February, just working occasional evenings. Lately I've been at it full time with a few extended breaks. I'm actually well in to the build at this point and am about ready to pull the boat off the forms, but I'll trickle out photos until I catch up to the real-time build. Thanks to all the other forum members who build canoes and share their methods on this forum. Another Kite Canoe build is in recognition of Stripperguys Kite build that I've looked through a few dozen times in the last couple months, Thanks!
This canoe will not be my first boat build. I made a skin kayak last year, finishing it during the winter and took these photos on a cold, windy day in early March on a local lake. I was surprised the lake wasn't frozen.
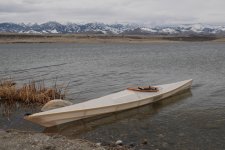
Who cares about kayaks though? On to the canoe build........
First, I cut all the strips using a skilsaw. Thanks Jim Dodd for all the details. My brother, a woodworker, couldn't believe how nice and uniform these came out. Oh, wait, the first step was to build a strongback. I bought 2 - 16", 16 foot I-beams for $50, screwed them together and used some old concrete soaked boards from last summers project (see, I'm standing on it) for the legs. The I-beams are straight as an arrow and really light too.
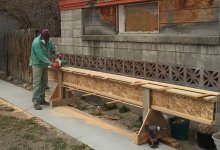
Very Nice! I'm very happy with this method.
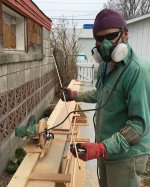
It took me half a day, including setup and takedown, to cut almost enough strips for 2 canoes. When I was collecting wood for this project I kept finding nice 8 and 12 foot boards when visiting lumber yards in the region so I would buy them. I did buy a few 16 foot boards for full price though.
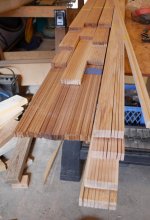
About this same time I cut all the forms from the plans I bought from Green Valley Canoe. I used 5/8" particle board. Here's a photo of my steaming setup and the stems being formed. I plan to use only inner stems made from cedar. I would have just built this stemless, but the plans didn't have stemlines for stemless construction. Since this is my first build I thought it best to stay with the plan. Note the old Wenonah looking on wondering what's up with all this.
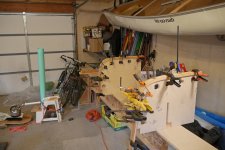
Next up is the bead and cove on the cedar strips. I have one of the cheapest router tables ever made, but it was certainly up to the task once I figured out how to attach the featherboards. This operation took me a full 9 hours, including setup and takedown, which I was determined to do all in one go. It started snowing near the end of this process. I wish I had pictures of the sawdust all over the snow.
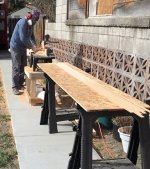
I ended up with a nice pile of beaded and coved strips, almost enough for 2 boats. Every one of them was spot on in dimensions. Needless to say, I was quite pleased with how well this part of the project went.
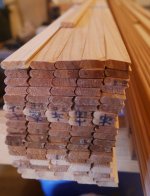
OK, that's enough for today. I'll make another post soon.