- Joined
- Aug 10, 2018
- Messages
- 1,389
- Reaction score
- 1,895
Brian, you're certainly right about the rough cut lumber and and the table saw (which I don't have) would certainly help.
I suspect that my sawyers weren't changing blades often enough as the band saws tend to start wandering & cutting thick-thin when the blades start to dull. I had some thicker spots in the pine (the Larch is more uniform) and probably should have run them thru a planer but I didn't.
Happily, the 1/8 inch cold-rolled seemed to have less flex than the strips and held the strips pretty solidly against the temporary fence.
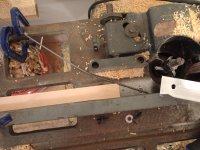
I replaced the lighter TIG wire with the 1/8 inch cold-rolled, used tin snips to cut the leading edge of the angle and then used pliers to form a ramp to guide the strip under it (as seen in the above picture). I inserted a strip, pushed the angle down securely and tightened the screws to secure the angle. It was a bit of a challenge getting the angle to have enough down pressure to hold the strip tightly to the table but, by bending the trailing corner down a little, I got it and the results are (IMO) acceptable.
One board had a pretty thick area at one end and the shaper set-up seems to uniform the strip pretty well. I may leave the crowder in place for the coving operation just to ensure total uniformity but I'm very pleased with today's results. You'll notice that the wire provides sufficient force to keep the strip tight against the fence while cutting much deeper as it removes the thick part of the strip. (apologies for the shaking, I was holding the phone with one hand & shoving the strip with the other)
Again, I think that running the boards thru a planer (especially when they have THAT much thickness variation) would have been a great idea, but I'm pretty satisfied with this set-up as a work-around and I'll, hopefully, get the bead cut into rest of the pine and the Larch on Wed. I'll then have to reset the shaper for the cove. (would a 2nd shaper seem excessive? Then I'd only have to reset if I changed strip thickness)
I suspect that my sawyers weren't changing blades often enough as the band saws tend to start wandering & cutting thick-thin when the blades start to dull. I had some thicker spots in the pine (the Larch is more uniform) and probably should have run them thru a planer but I didn't.
Happily, the 1/8 inch cold-rolled seemed to have less flex than the strips and held the strips pretty solidly against the temporary fence.
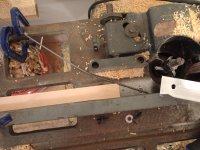
I replaced the lighter TIG wire with the 1/8 inch cold-rolled, used tin snips to cut the leading edge of the angle and then used pliers to form a ramp to guide the strip under it (as seen in the above picture). I inserted a strip, pushed the angle down securely and tightened the screws to secure the angle. It was a bit of a challenge getting the angle to have enough down pressure to hold the strip tightly to the table but, by bending the trailing corner down a little, I got it and the results are (IMO) acceptable.
One board had a pretty thick area at one end and the shaper set-up seems to uniform the strip pretty well. I may leave the crowder in place for the coving operation just to ensure total uniformity but I'm very pleased with today's results. You'll notice that the wire provides sufficient force to keep the strip tight against the fence while cutting much deeper as it removes the thick part of the strip. (apologies for the shaking, I was holding the phone with one hand & shoving the strip with the other)
Again, I think that running the boards thru a planer (especially when they have THAT much thickness variation) would have been a great idea, but I'm pretty satisfied with this set-up as a work-around and I'll, hopefully, get the bead cut into rest of the pine and the Larch on Wed. I'll then have to reset the shaper for the cove. (would a 2nd shaper seem excessive? Then I'd only have to reset if I changed strip thickness)

Last edited: