I assembled both halves of the mold and bolted them together. Then I constructed two slings on the strongback to hold the upright mold: these are simply 2x4's screwed to the strongback in a "v" fashion with an NRS strap slung between the tops of the v to cradle the mold. It is resting about 2" above the strongback- this should allow me to apply the vacuum bag all around it when that time comes. I also taped all the edges and over the bolts with vinyl electrical tape to cover any sharp edges and prevent vacuum bag punctures.
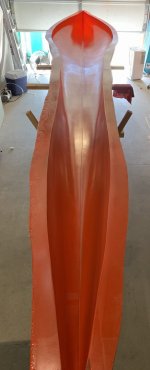
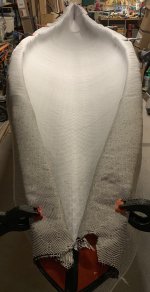
Then I started laying fabric: First a football of 1.4oz Eglass so I can sand out bottom scratches without the innegra fuzzing. After this, I laid some cosmetic detail pieces that I don't have any photos of- so they will be a surprise if they turn out. Then a full blanket of the innegra/carbon hybrid cloth. It is surprisingly difficult to get it to lay flat in the mold: it takes a lot of massaging the fabric to get it to conform to the compound curves of the hull, and then to make sure the pattern is relatively straight. Once it is positioned, there is some careful cutting of the bow/stern ends to get them to lay down in a nice overlap in the pointy ends of the mold. My caveman fingers are too large for this and I found a leftover pine strip useful for manipulating fabric in the ends. I was planning to put some internal skid plates in: strips of Sglass on the outside of the innegra, but I really don't think I can manipulate a small strip in the tight corner and not have it get all wrinkled when putting the innegra on top.
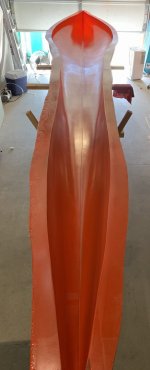
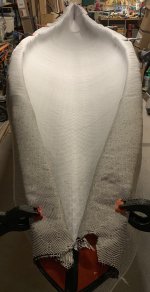
Then I started laying fabric: First a football of 1.4oz Eglass so I can sand out bottom scratches without the innegra fuzzing. After this, I laid some cosmetic detail pieces that I don't have any photos of- so they will be a surprise if they turn out. Then a full blanket of the innegra/carbon hybrid cloth. It is surprisingly difficult to get it to lay flat in the mold: it takes a lot of massaging the fabric to get it to conform to the compound curves of the hull, and then to make sure the pattern is relatively straight. Once it is positioned, there is some careful cutting of the bow/stern ends to get them to lay down in a nice overlap in the pointy ends of the mold. My caveman fingers are too large for this and I found a leftover pine strip useful for manipulating fabric in the ends. I was planning to put some internal skid plates in: strips of Sglass on the outside of the innegra, but I really don't think I can manipulate a small strip in the tight corner and not have it get all wrinkled when putting the innegra on top.