Some good news, and some not as good news:
Good news: I'm finished fiberglassing. And happy about it.
Good news: The mold released just fine from the plug, and has a great shiny tool surface.
Not as good news: Im going to have to do a little repair on the mold.
I finished laminating the fiberglass matt- same schedule as the other side. After It cured for a day, I did a quick sanding of the outside with 60grit and then rolled on a 'hot coat' of resin without any fiberglass. I thought it would be an easy way to knock off any little invisible fiberglass slivers, and to leave a smooth surface to prevent any puncture of the vacuum bag. Tonight, I drilled holes in the parting flange for 1/4" bolts, and then cut the flanges and parting line down to 3.5" with the sawzall. It worked well using a metal blade, but made a mess and sent fiberglass dust everywhere. Then I sanded the cut edges smooth and went to separate the mold. Using a plastic putty knife and wooden chip brush handles, I was able to pry it apart without too much trouble. The plug actually survived pretty well: there was a little section along the parting flange where the duratec stuck to the mold and pulled off of the plaster, but those small chips released form the mold just fine.
The mold did end up right around 5mm thick. It is stiff enough, but I don't think I'd recommend making it any thinner. I was glad to find that If I'm careful, I can lift and move each side myself- picking it up from the center.
The second half of the mold is near perfect. I can buff it then start waxing and prepping it for infusion. The first half though, needs a bit of repair work. The part of the flange that alligatored will need some gelcoat fill and sanding, and the gunwale edge between the hull and flange is a little rough in some places. Nothing I can't fix, and I'll chalk it up to amateur mistakes that more experienced mold-makers have learned how to avoid.
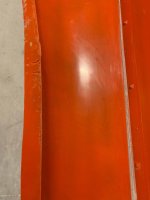