I guess with the joint compound I officially departed from a standard canoe build. I can't put away the woodworking tools quite yet, but I have moved into the composite realm.
I put two full coats of joint compound on the plug. I sanded the first one roughly, then dusted some old spray paint over it for a contrast. I put on a second coat and spend a good deal of time sanding the curves as evenly as I could. For the most part I used a regular drywall sanding block, but I also made a torture-board and duct taped three sanding screens together to really level things out. It worked really well on the flatter sections of the hips, and on the long, skinny nose. I thought I had it pretty well flat.
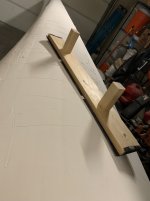
I then shot it with 2 coats of the duratec primer-surfacer. I've never used this product before, so it was with some trepidation I mixed it up and poured it into the paint gun. The problem is that it will gel in 14-16 minutes- so you have to shoot it and then clean the gun right away. I'm am novice painter at best, and the short gel time doesn't give me much room for error or time to dial things in. I used a $45 HVLP gun with a 2.5mm tip. I catalyzed at 1.7% as it was about 80 degrees. I set a timer for 13 minutes, which was my signal to stop spraying and and get some acetone into the gun asap. It turned out to be plenty of time. About 700 mL mixed was enough for a moderate coat on one side, and I could mix and spray it in only 6-7 minutes or so. At first I sprayed it un-thinned, and it went down, but was really sputtery and orange peely. I also had the air control too far open so it was just blasting out the gun. On the other side, I tried thinning it 10% with MEK substitute and it flowed out so much nicer than unthinned. I also got my air settings dialed in to give a nice even spray.
The good news is that this product leaves a good surface on the plug. The bad news is that it shows just how crappy of a sanding job I did. I am going to block sand it a little and shoot two more coats on each side. The drywall mud also had a lot of small craters and pinholes in it that didn't get fully covered over, so they need to be filled. So more sanding is in my future.
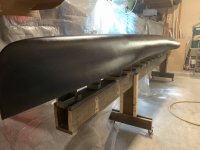