Thanks for the details, looks like Jim Dodd's method is what I'll go for on this one. Rough size turns in at 7 3/4 x 33.
Well, wait no longer.
Finished Sanding the fill Monday, and then realized that I needed more fill. Came up with a new (for me) Recipe that would not require multi-hour curing times.
1 part water, 3 parts wood glue (carpenters glue) (just a bit of water really thins it out)
wood flour and cabosil to taste. long pot life, but spread it in a thin crack and it's ready to sand in 25-30 min. Much lighter than an equivalent resin recipe, as well.
This is about as clean as I chose to get the ends, as they will be covered by the bulkhead, and getting in there is a real pain. Plus the main pad on the RO got used as a sanding pad without any sanding paper on it, so now it does not want to hang on to the interface pad.
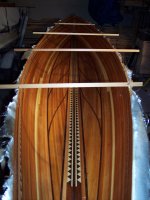
Wet-out (Solo, this time. My family all had schedules they needed to keep, so no help) took 4 hours. Finished at midnight. No Sealcoat this time, there seems no point with a resin this thin. There is definitely a use case for slow resins in temperatures just high enough for curing... The glass was being finicky. the inside of that knuckle could have maybe used a cabosil filet, but in the end it worked out. The sticks ended up being the best way to hold the hull in shape - the center had sprung about 2" with just the outer layer of glass. Four in those locations were just perfect.
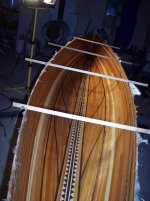
The night was not without some oddities. If you think that that looks like a patch in the middle of a fresh layup, you are right. I could not get the glass to lay in at this point - there were bridges 4"x4" on both sides of the hull, on both ends. I had to cut a slit about 6" long right down the center of the glass and allow it to spread. Since this will be under the bulkhead, I'm not terribly worried. Overall, though, I think it turned out well
The hull looks great. Can't wait to see it all fiberglassed!
Well, wait no longer.
Finished Sanding the fill Monday, and then realized that I needed more fill. Came up with a new (for me) Recipe that would not require multi-hour curing times.
1 part water, 3 parts wood glue (carpenters glue) (just a bit of water really thins it out)
wood flour and cabosil to taste. long pot life, but spread it in a thin crack and it's ready to sand in 25-30 min. Much lighter than an equivalent resin recipe, as well.
This is about as clean as I chose to get the ends, as they will be covered by the bulkhead, and getting in there is a real pain. Plus the main pad on the RO got used as a sanding pad without any sanding paper on it, so now it does not want to hang on to the interface pad.
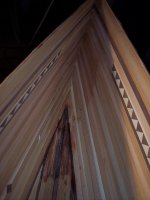
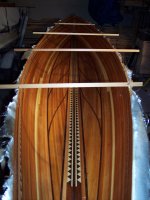
Wet-out (Solo, this time. My family all had schedules they needed to keep, so no help) took 4 hours. Finished at midnight. No Sealcoat this time, there seems no point with a resin this thin. There is definitely a use case for slow resins in temperatures just high enough for curing... The glass was being finicky. the inside of that knuckle could have maybe used a cabosil filet, but in the end it worked out. The sticks ended up being the best way to hold the hull in shape - the center had sprung about 2" with just the outer layer of glass. Four in those locations were just perfect.
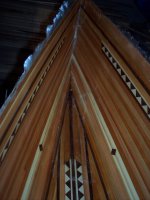
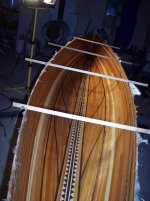
The night was not without some oddities. If you think that that looks like a patch in the middle of a fresh layup, you are right. I could not get the glass to lay in at this point - there were bridges 4"x4" on both sides of the hull, on both ends. I had to cut a slit about 6" long right down the center of the glass and allow it to spread. Since this will be under the bulkhead, I'm not terribly worried. Overall, though, I think it turned out well