- Joined
- Jul 6, 2021
- Messages
- 643
- Reaction score
- 562
“I was able to get the hogging out and slight v shape back with bracing. I don’t have a good before photo, but this is in a much better shape. I am going to run 6oz fiberglass tape and epoxy between the skid plates and roll epoxy on the outside. I don’t expect a miracle, but I am hopeful this helps. I am open suggestions if anyone has any.”
Almost all of the fiberglass tapes I have are E-glass. Some years ago we tried some “experimental” repairs on the bottom of a couple vee bottomed sea kayaks, using E-glass tape, S-glass fabric and Dynel.
The E-glass and S-glass on the vee bottom were torn up after season’s hard use, the Dynel was still going strong, and still is. This is full length Dynel sleeve on a vee bottomed Caribou sea kayak.
P5290028 by Mike McCrea, on Flickr
The orange stripes are a Baltimore Orioles homage, covering repairs to the sharp (originally a stitch and glue design) kevlar chines. Of note, those chine cracks were repaired using 2” E-glass. Kinda like the current day Orioles, even those (not bottom-dweller) repairs using E-glass tape were nicked and chipped fugly a few years later, and were kind of a PITA to re-repair.
At least the Caribou looks good. I have no such hopes for the O’s.
For a keel strip spanning nearly stem to stem I’d be use pre-rolled Dynel sleeve, and rolled, release treated peel ply.
PC290010 by Mike McCrea, on Flickr
Even with two fabric layers Dynel sleeve stands less tall then the old Kevlar felt skid plates.
20220301_090917 by Mike McCrea, on Flickr
Done properly Dynel sleeve doesn’t stand too tall, ugly or gurgling, and the abrasion resistance of Dynel is far beyond fiberglass. Still my favorite Dynel test, someone who DIY abraded fiberglass and single layer Dynel fabric using a brick.
A 6 pound fire brick held on a 45 degree angle
The test with 6oz fiberglass cloth took 52 strokes to cut through to the wood
The 5.5oz Dynel has more than 250 strokes and is still not through to the wood
Sweet Composites sells Dynel sleeve. Part way down this link:
https://sweetcomposites.com/Polyester.html
The “lightweight” Dynel sleeve is 1 ½” wide, the “standard weight” is 1 ¾” wide.
Sweets has a $25 minimum order or, ordering less than that, a $25 handling charge. What else do you need? There are some hard to find boatwork materials in the Sweets catalog. Oooh, look, graphite sleeve, Dynel cord. . . . oh my, thick, bias woven Twaron and Kevlar tapes.
https://sweetcomposites.com/Fabric.html
Release treated peel ply, used in a long linear application, is easiest done using peel ply in narrow rolls. From Aircraft Spruce & Specialty. That pre-cut rolled peel ply is amazingly handy, I may need to buy more soon.
https://www.aircraftspruce.com/catalog/cmpages/peelply.php
The peel ply doesn’t need to be a lot wider than the Dynel sleeve or glass tape; an inch of overlap on each, in case your unrolling application is a bit off kilter side is fine, and in fact too much peel ply overlap will wrinkle when laid down and compressed, leaving the occasional epoxy crinkle at the edges.
This peel ply is too narrow, and this peel ply is too wide, and a 3” or 4” wide roll is just right for most tapes or Dynel sleeve.
Even if you go with fiberglass tape the rolled peel ply is (beyond) helpful. The selvage edge of glass tapes will set up tall and scraped epidermis bleeding sharp; compressing the tape under the peel ply, by hand or hard roller, will eliminate that sharp selvage edge, and 90% of the sanding.
Easiest installation of a long keel strip, unless you have a sixteen foot wingspan, is to dry fit the sleeve (or tape), sighting it in end-to-end aligned with the center, tape off around the perimeter of the free resting Dynel, and then re-roll the sleeve. Same for the peel ply, cut to length, overlapping the tape box, and re-rolled for later application.
Wet out inside the taped area with epoxy, unroll the sleeve atop that, topcoat generously and wait, and wait some more, until the epoxy has opportunity to fully saturate into the sleeve but is still uncured enough to compress under peel ply.
Then pull the tape and paper mask, unroll the already cut to length peel ply over the sleeve and compress it. Using release treated peel ply, not green pull nylon stuff, you can walk away ‘til the next morning. The peel ply pull is an exciting reveal. Or maybe I’m just easily excited.
And, not to kill your hopes and dreams of resurrecting a prefect hull shape, but if the internal keelson bracing is coming out, a strip of glass tape or even Dynel sleeve will only do so much to eliminate the hog or other odd concavities from the hull’s memory.
But it can’t hurt.
I gotta ask, after reinforcing keel strip and other repairs, is there a painting plan?
Almost all of the fiberglass tapes I have are E-glass. Some years ago we tried some “experimental” repairs on the bottom of a couple vee bottomed sea kayaks, using E-glass tape, S-glass fabric and Dynel.
The E-glass and S-glass on the vee bottom were torn up after season’s hard use, the Dynel was still going strong, and still is. This is full length Dynel sleeve on a vee bottomed Caribou sea kayak.
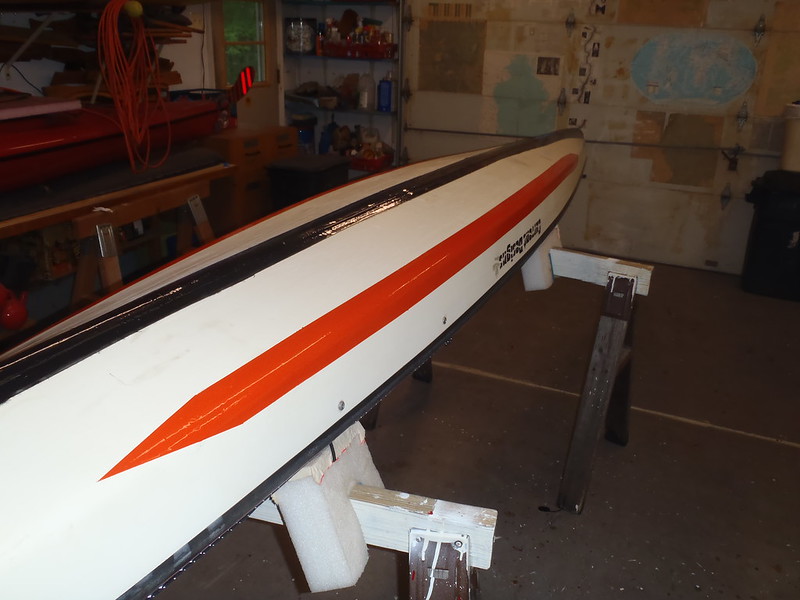
The orange stripes are a Baltimore Orioles homage, covering repairs to the sharp (originally a stitch and glue design) kevlar chines. Of note, those chine cracks were repaired using 2” E-glass. Kinda like the current day Orioles, even those (not bottom-dweller) repairs using E-glass tape were nicked and chipped fugly a few years later, and were kind of a PITA to re-repair.
At least the Caribou looks good. I have no such hopes for the O’s.
For a keel strip spanning nearly stem to stem I’d be use pre-rolled Dynel sleeve, and rolled, release treated peel ply.
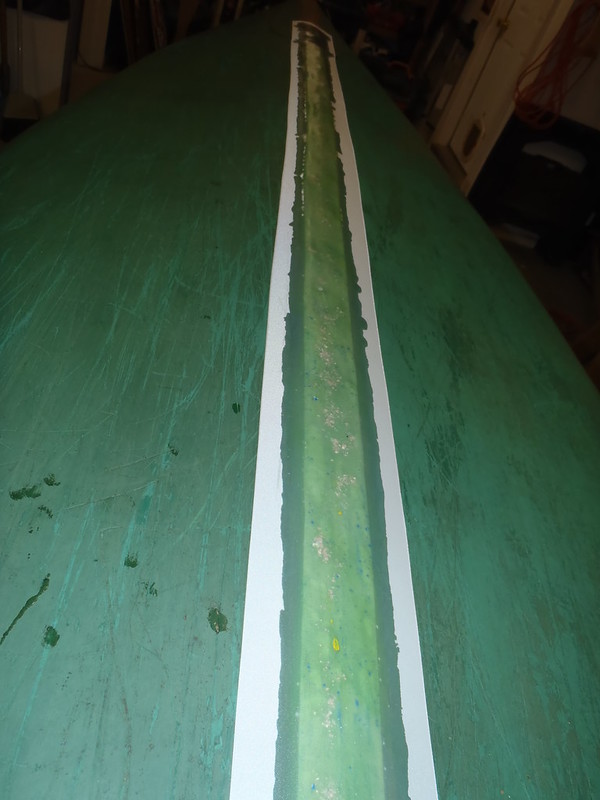
Even with two fabric layers Dynel sleeve stands less tall then the old Kevlar felt skid plates.

Done properly Dynel sleeve doesn’t stand too tall, ugly or gurgling, and the abrasion resistance of Dynel is far beyond fiberglass. Still my favorite Dynel test, someone who DIY abraded fiberglass and single layer Dynel fabric using a brick.
A 6 pound fire brick held on a 45 degree angle
The test with 6oz fiberglass cloth took 52 strokes to cut through to the wood
The 5.5oz Dynel has more than 250 strokes and is still not through to the wood
Sweet Composites sells Dynel sleeve. Part way down this link:
https://sweetcomposites.com/Polyester.html
The “lightweight” Dynel sleeve is 1 ½” wide, the “standard weight” is 1 ¾” wide.
Sweets has a $25 minimum order or, ordering less than that, a $25 handling charge. What else do you need? There are some hard to find boatwork materials in the Sweets catalog. Oooh, look, graphite sleeve, Dynel cord. . . . oh my, thick, bias woven Twaron and Kevlar tapes.
https://sweetcomposites.com/Fabric.html
Release treated peel ply, used in a long linear application, is easiest done using peel ply in narrow rolls. From Aircraft Spruce & Specialty. That pre-cut rolled peel ply is amazingly handy, I may need to buy more soon.
https://www.aircraftspruce.com/catalog/cmpages/peelply.php
The peel ply doesn’t need to be a lot wider than the Dynel sleeve or glass tape; an inch of overlap on each, in case your unrolling application is a bit off kilter side is fine, and in fact too much peel ply overlap will wrinkle when laid down and compressed, leaving the occasional epoxy crinkle at the edges.
This peel ply is too narrow, and this peel ply is too wide, and a 3” or 4” wide roll is just right for most tapes or Dynel sleeve.
Even if you go with fiberglass tape the rolled peel ply is (beyond) helpful. The selvage edge of glass tapes will set up tall and scraped epidermis bleeding sharp; compressing the tape under the peel ply, by hand or hard roller, will eliminate that sharp selvage edge, and 90% of the sanding.
Easiest installation of a long keel strip, unless you have a sixteen foot wingspan, is to dry fit the sleeve (or tape), sighting it in end-to-end aligned with the center, tape off around the perimeter of the free resting Dynel, and then re-roll the sleeve. Same for the peel ply, cut to length, overlapping the tape box, and re-rolled for later application.
Wet out inside the taped area with epoxy, unroll the sleeve atop that, topcoat generously and wait, and wait some more, until the epoxy has opportunity to fully saturate into the sleeve but is still uncured enough to compress under peel ply.
Then pull the tape and paper mask, unroll the already cut to length peel ply over the sleeve and compress it. Using release treated peel ply, not green pull nylon stuff, you can walk away ‘til the next morning. The peel ply pull is an exciting reveal. Or maybe I’m just easily excited.
And, not to kill your hopes and dreams of resurrecting a prefect hull shape, but if the internal keelson bracing is coming out, a strip of glass tape or even Dynel sleeve will only do so much to eliminate the hog or other odd concavities from the hull’s memory.
But it can’t hurt.
I gotta ask, after reinforcing keel strip and other repairs, is there a painting plan?