I'm in the first stages of build on my very first strip canoe, a Prospector 16. I'll try to post comments, pictures, etc. along the way. Any help, criticism, comments are appreciated.
First, a brief summary of my background & equipment. I've been a woodworker, and woodworking teacher for a very long time. Between my home shop, and school shop, there isn't much I don't have access to. I've been researching fairly steady for the past 6 months, purchasing (& reading) seveal books, including CanoeCraft. I'm confident I have the ability, and hope I've gained enough knowledge to keep the mistakes manageable. The discussion on "Light Weight Solo Tripper Build" is awesome.
I just finished cutting my mold stations, and ran into my first snag. With access to a CNC router, I decided to use it. I converted table of offset data to X-Y coordinates, then generated a fair curve for the stations. I SHOULD HAVE created a half curve, from shear to profile, then mirrored it. I didn't realize my mistake until I was done. The result is, the centerline of the bottom of the canoe is rounded, rather than coming to a point from stations 3 thru 6. I'm going to regenerate curves tonight, so I can compare what they should be, to what I have. Unfortunately, there's no way to accurately put these pieces back into the CNC router. I'll have to modify by hand, if I go that way.
I'll be making a set of Jimmy clamps this weekend, and hopefully have my work station set up. I'm cleaning out a one car garage, and dedicating it to this canoe build project.
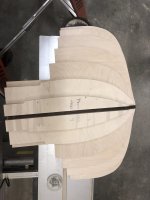
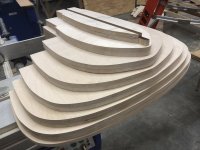
First, a brief summary of my background & equipment. I've been a woodworker, and woodworking teacher for a very long time. Between my home shop, and school shop, there isn't much I don't have access to. I've been researching fairly steady for the past 6 months, purchasing (& reading) seveal books, including CanoeCraft. I'm confident I have the ability, and hope I've gained enough knowledge to keep the mistakes manageable. The discussion on "Light Weight Solo Tripper Build" is awesome.
I just finished cutting my mold stations, and ran into my first snag. With access to a CNC router, I decided to use it. I converted table of offset data to X-Y coordinates, then generated a fair curve for the stations. I SHOULD HAVE created a half curve, from shear to profile, then mirrored it. I didn't realize my mistake until I was done. The result is, the centerline of the bottom of the canoe is rounded, rather than coming to a point from stations 3 thru 6. I'm going to regenerate curves tonight, so I can compare what they should be, to what I have. Unfortunately, there's no way to accurately put these pieces back into the CNC router. I'll have to modify by hand, if I go that way.
I'll be making a set of Jimmy clamps this weekend, and hopefully have my work station set up. I'm cleaning out a one car garage, and dedicating it to this canoe build project.
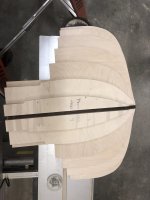
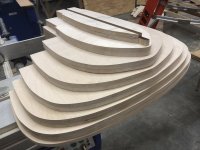