Rounding the shafts for both the twin and single blades is the exact same process IF you leave the shafts as a regular rectangle. Our singles aren’t, they have that taper, so an extra step will need to be done.
To mark up a regular shaft, first draw a line on the face, perpendicular to the side. Then measure the width at that point and measure along the shaft that distance and draw another mark. Carefully join the corners and you should have this.
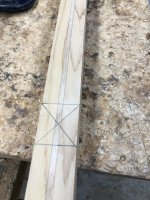
One half that diagonal is the correct measurement to draw a line for material removal. Set your measurement tool ( mine is an Incra Gauge) using that and draw in a line from each side. Flip over the shaft do the other side while you have the gauge set, repeat on the other side(s) and you get
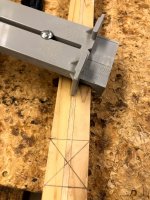
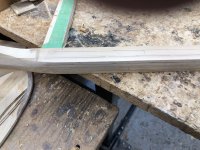
Set your spoke shave/plane for light cuts and remove the corners using the lines as a guide. If the wood is grabbing/tearing just reverse the planing direction. The shaft wood will likely have a grain direction and you really don’t want to try and go opposite that or you will get tearouts/divets that can quickly mar the shaft. The light cuts help reduce this and also the extent of any tearouts you may get.
You now have a hex shape that looks like this, with 8 small corners instead of 4 larger ones
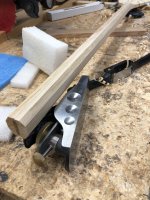
Now lightly plane off those 8 smaller corners, the operative word here is “lightly”, the corners are small and you just want to make the faces about the same size.
This will give you a 16 sided figure, that’s close to round, like this
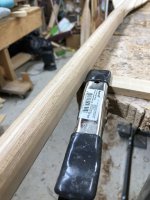
Before we sand the shaft, let’s go back and do the tapered shaft.
We have a mark 6” up from where the blade begins, so draw one of the “X” boxes as described above, this time though, just make a mark for the line position.
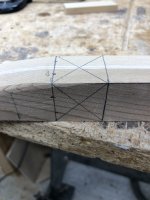
Go down to the other end near the handle and repeat the process
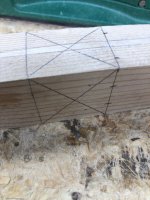
Now use a ruler to connect the marks, this gives guide line that follow the taper …. So the shaft can gradually change along its length.

And the final guide lines look like this
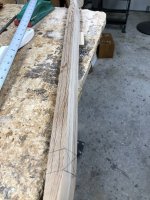
And carving away the corners is the same as regular shaped shafts
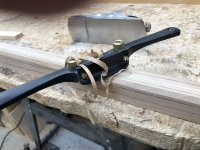
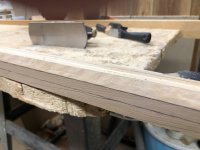
On to final rounding and finishing of the shafts. First up, figure out your clamping solution, you need access to the entire length of the blade and you don’t want it flopping around. The blade is no longer flat, so remember when you fasten it down, be careful to not stress it … here was my solution, flat wood, foam pad and light clamp at one end. Pair of blacks at the other.
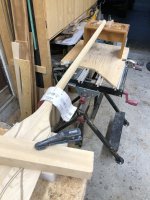
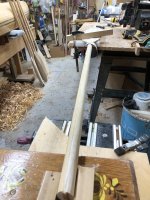
Sanding regime starts with a narrow strip of 80 grit and we start see sawing, gently down the blade, from top, sides, then flip over and repeat . The reason to go lightly is the 80 will scratch the wood, it is going to remove wood and shape the shaft … leaving visible scratches you will have to remove later. The harder you you pull the sand paper, the deeper the scratches and all those scratch have to sanded out with the next grit, go lightly and save some work on the next pass.
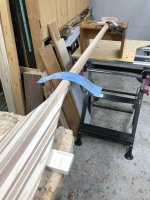
Move to a 100 grit strip, do the passes as before, finish by sanding with the grain, holding the paper with a small foam piece. The 100 grit is the start of actually finishing the shaft, the wood removal is done, so we are just getting stuff smooth now. I follow up with 120 and 150, as above and call it finished.
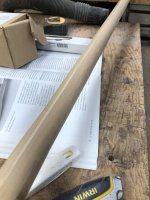
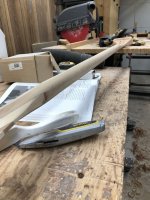
That gives us nicely rounded, ready to be finished shafts …. The twin blade handles are still not quite queued for installation … but soon.
Brian
To mark up a regular shaft, first draw a line on the face, perpendicular to the side. Then measure the width at that point and measure along the shaft that distance and draw another mark. Carefully join the corners and you should have this.
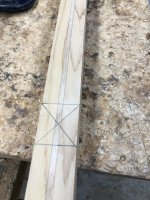
One half that diagonal is the correct measurement to draw a line for material removal. Set your measurement tool ( mine is an Incra Gauge) using that and draw in a line from each side. Flip over the shaft do the other side while you have the gauge set, repeat on the other side(s) and you get
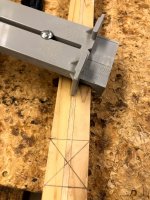
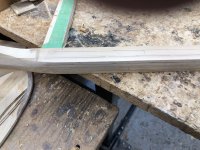
Set your spoke shave/plane for light cuts and remove the corners using the lines as a guide. If the wood is grabbing/tearing just reverse the planing direction. The shaft wood will likely have a grain direction and you really don’t want to try and go opposite that or you will get tearouts/divets that can quickly mar the shaft. The light cuts help reduce this and also the extent of any tearouts you may get.
You now have a hex shape that looks like this, with 8 small corners instead of 4 larger ones
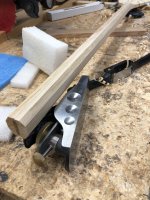
Now lightly plane off those 8 smaller corners, the operative word here is “lightly”, the corners are small and you just want to make the faces about the same size.
This will give you a 16 sided figure, that’s close to round, like this
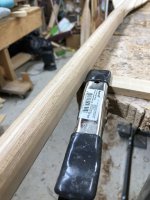
Before we sand the shaft, let’s go back and do the tapered shaft.
We have a mark 6” up from where the blade begins, so draw one of the “X” boxes as described above, this time though, just make a mark for the line position.
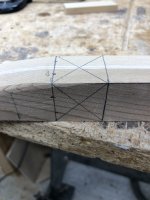
Go down to the other end near the handle and repeat the process
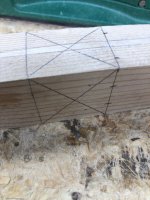
Now use a ruler to connect the marks, this gives guide line that follow the taper …. So the shaft can gradually change along its length.

And the final guide lines look like this
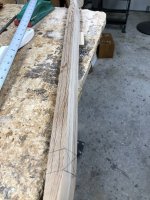
And carving away the corners is the same as regular shaped shafts
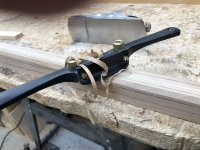
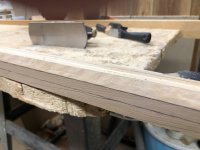
On to final rounding and finishing of the shafts. First up, figure out your clamping solution, you need access to the entire length of the blade and you don’t want it flopping around. The blade is no longer flat, so remember when you fasten it down, be careful to not stress it … here was my solution, flat wood, foam pad and light clamp at one end. Pair of blacks at the other.
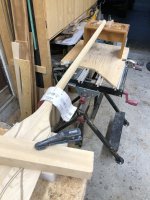
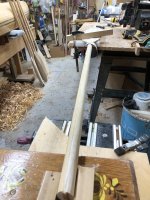
Sanding regime starts with a narrow strip of 80 grit and we start see sawing, gently down the blade, from top, sides, then flip over and repeat . The reason to go lightly is the 80 will scratch the wood, it is going to remove wood and shape the shaft … leaving visible scratches you will have to remove later. The harder you you pull the sand paper, the deeper the scratches and all those scratch have to sanded out with the next grit, go lightly and save some work on the next pass.
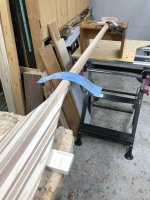
Move to a 100 grit strip, do the passes as before, finish by sanding with the grain, holding the paper with a small foam piece. The 100 grit is the start of actually finishing the shaft, the wood removal is done, so we are just getting stuff smooth now. I follow up with 120 and 150, as above and call it finished.
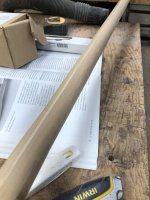
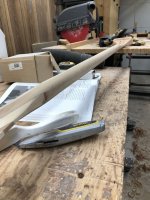
That gives us nicely rounded, ready to be finished shafts …. The twin blade handles are still not quite queued for installation … but soon.
Brian