You can see the centerboard of my boat protruding below the hull in the designer's drawing.
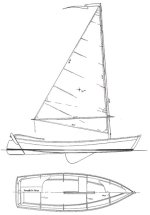
The centerboard goes through a hole in the bottom of the hull. The centerboard case, or trunk, keeps the water on the outside, and also provides structure to take the lateral force of the board.
The centerboard pivots on a pin (1/2" bronze in this case) and can retract into the hull. It will be raised and lowered by a lanyard, and will have a lead weight to keep it underwater. There are several advantages to this arrangement:
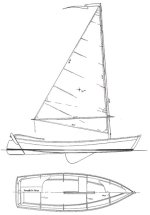
The centerboard goes through a hole in the bottom of the hull. The centerboard case, or trunk, keeps the water on the outside, and also provides structure to take the lateral force of the board.
The centerboard pivots on a pin (1/2" bronze in this case) and can retract into the hull. It will be raised and lowered by a lanyard, and will have a lead weight to keep it underwater. There are several advantages to this arrangement:
- The boat can operate in shallow water (4" for this boat) without running aground
- Because the centerboard is free to move, it can retract into the hull if it hits an obstacle
- The centerboard can be partly raised to fine tune the steering
- Raising the centerboard makes it easy to get the boat on and off a trailer.