I work in spurts. With the sheer strakes in place, it's time to fit the outer stem. To match the inner and outer stems as closely as possible, I used a technique from Sam Rabl's Boatbuilding in Your Own Back Yard.
I attached the outer stem loosely, and then ran a Japanese saw between the two parts. It took two passes to get a close enough thank-goodness-for-the-gap-filling-properties-of-epoxy fit. It's important to remove any screws before hitting them with the saw.
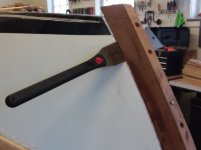
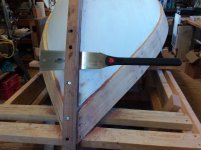
Outer stem is fitted.
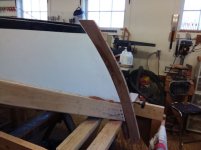
I attached the outer stem loosely, and then ran a Japanese saw between the two parts. It took two passes to get a close enough thank-goodness-for-the-gap-filling-properties-of-epoxy fit. It's important to remove any screws before hitting them with the saw.
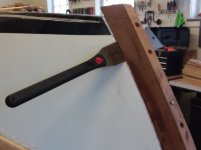
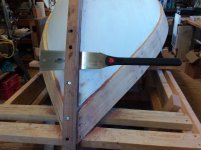
Outer stem is fitted.
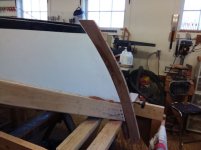