G
Guest
Guest
As the last outfitting touch on the FreeFIRE I wanted to install partial spray covers. This will be wordy, and photo heavy as usual; there are twentysome finicky little steps to the process. It’s not hard, just fussy to get right.
TLDR – I made a partial spray cover for the FreeFIRE using no-sew heat sealable material.
While only a day’s work (well two, I had to wait for some adhesive to set up) I will break up the process into manageable chunks for easier reading.
The bow cover will be more partial than usual; I typically bring the bow cover back to just before the utility/sail thwart, but this canoe has a combination foot brace/sail thwart, so the bow cover will be a shortie, call it 53” long. The stern portion can come all the way to the rear thwart, closer to 63”, leaving some easily accessible gear storage room behind the seat.
I do not saw. I can not sew. And our sewing machine has been broken for years. But, I have some leftover bright red heat sealable Packcloth from Seattle Fabrics, which needs only the use of an iron (and some tricky templates before cutting the fabric).
https://www.seattlefabrics.com/58-400-D-Heat-Sealable-Coated-Packcloth-2150-linear-yard_p_50.html
Some important caveats to consider before making a spray cover from heat sealable fabric:
First, without having purchased and installed the (far more elegant, custom) partial, open cockpit covers Cooke Custom Sewing made for our Wenonah Wilderness and soloized OT Penobscot I would be clueless about the basic design. And, without having installed those CCS covers using Dan’s step-by-step installation guide, even more lost about marking the locations on the hull for attaching the snaps on covers, which are installed first.
Second (& third) caveats, the Seattle Fabrics Packcloth is not the same material Cooke Custom Sewing uses for their spray cover. Not by a long shot; “It is weaker, the heavy urethane coating used to make fabric heat sealable reduces the tongue tear strength and if starts to tear it is far more likely to continue with less force”. I believe the coated nylon CCS uses has superior tear resistance when compared even to similar weight coated polyester.
The heat sealable Packcloth is heavier than coated nylon. I previously made short partial covers using heat sealable Packcloth for our Mad River Freedom Solo.
P1130039 by Mike McCrea, on Flickr
Those short partial covers weigh 1oz shy of 3lbs. The CCS covers for our longer, wider Penobscot 16 weigh a couple ounces less, and that weight includes a large center storage cover, paddle pockets at both ends and five lash straps. Gotta have lash straps for the paddles; five because I often have a double blade, single blade, furled sail and push pole to secure.
P2160542 by Mike McCrea, on Flickr
The same open cockpit design CCS covers for our Wenonah Wilderness, same two paddle pockets, large center storage cover, etc, weigh 2lbs, 10oz. If weight and tear resistant matter, coated nylon is a better choice.
Heat sealable Packcloth (or even the lighter 200D Oxford cloth – that will come up later) does not stuff. The DIY heat sealable Packcloth covers for our Freedom Solo are rolled into a cylinder and stored in an old camp chair bag. Our 3-part Cooke covers are in a CCS stuff bag the size of a youth football.
PB220102 by Mike McCrea, on Flickr
Red bag Wilderness, green bag Penobscot, blue bag DIY Packcloth
So there is all that on the demerit side to using heat sealable material. But I have bright red Seattle Fabrics material left and, as an experimental attachment, plan on using (a few) snaps combined with Dual Lock to make short partial spray covers for the FreeFIRE.
I needed to mark templates for cutting the fabric. To facilitate that I have a roll of Visqueen plastic, already cut to the same 58” width as the Packcloth. (CCS sends clear Mylar with instructions for that purpose)
First though, I need a large table to use as a cutting and ironing surface.
Our large potable platform “tables” are mostly painted 4’x8’ sheet of S1S plywood, stiffened with battens on the backside. But the 48” dimension can be problematic with 58” wide material, so I grabbed a second work platform, one of the handy 2’x8’ platforms.
Those half-width tabletops are really handy, and much easier to move around from basement to shop through three doorways; the yellow square marks the center balance, so I can carry them via a backside batten dangling from one hand.
PB180001 by Mike McCrea, on Flickr
The Visqueen came folded, as did the Packcloth for less expensive shipping. Both have been stored tightly rolled on lengths of pipe to remove the creases, a good idea with any material that comes folded (hint for DougD and Chip).
PB180004 by Mike McCrea, on Flickr
First, a length of 58” wide visqueen cut to the bow cover spray cover length. I folded over and temp taped 1” heat sealable “hems” at both ends, and Sharpied a centerline for orientation before placing it atop the canoe.
PB180005 by Mike McCrea, on Flickr
The visqueen was taped on the bow and some preliminary Sharpie marks drawn; the bottom of the black side stripes, as far down as I would want the spray covers to reach.
PB190007 by Mike McCrea, on Flickr
And marked the location of the carry handles and thwarts. I will be using at least a few snaps on each cover and those should not be seated directly behind the end of a thwart. I have done that in the past with DIY covers and had to remove the thwart to install the snaps. See also the reasons to use transparent visqueen plastic as a template material.
PB190010 by Mike McCrea, on Flickr
Template un-taped from the hull and back on the table I needed two more lines for the heat sealable “hems” on the long sides. I wanted a sizeable hem on those sides for doubled-over durability. My little shop iron is only 4” wide, so I went with a 3 ½” fold over hem, Sharpie-ing that fold over line below/inside the stripe line.
PB190012 by Mike McCrea, on Flickr
To make certain I didn’t cut the wrong line (not that I’ve ever done something like that) I crossed out the side stripe line, added a dotted line for the four inch fold-over-to-this-point (which will later be Sharpied on the heat sealable side of the material) and cut out the rough template.
PB190013 by Mike McCrea, on Flickr
That is a fair amount of material for a small bow spray shield, 55” long x 40” at the wide end.
A very “rough” template. For starters the fold over heat sealed hems become peculiarly shaped with angled material; when properly cut to fold over two corners sticks out in pointy dog ears, and two corners come up a bit short.
PB190015 by Mike McCrea, on Flickr
PB190018 by Mike McCrea, on Flickr
Helpfully the excess /| on the one corner is essentially the additional |/ needed on the other, just cut it off and tape it on the other side.
PB190021 by Mike McCrea, on Flickr
With the little slices and dog ears shaped there remain just a few more weirdo cuts to make on the template. The fabric only adheres heat sealable side to heat sealable side, and I will need to fold over and iron the 1” hems on the ends.
PB190024 by Mike McCrea, on Flickr
PB190025 by Mike McCrea, on Flickr
Last step with the bow cover template, toss it over the bow for a look see, and mark the snap locations on the plastic. The experimental plan is to use both Dual Lock and snaps. I found the snaps on a simple splash and drip cover, with no-stress from a spray skirt tunnel, can be spaced at least 10” or 12” apart, but with the Dual Lock augmentation I am planning only three snaps on each side of the bow cover, spaced 25” apart.
My theory is that having a snap at each end and, eh, one in the middle, will help align the Dual Lock for more accurate press fastening. I have a hopefully strategic plan for the Dual Lock installation as well.
Time to cut some red heat sealable fabric. Well crapola. I thought I had a lot more red heat sealable fabric, but have only enough for the bow cover. I will cut and install this one and ponder buying more.
PB200028 by Mike McCrea, on Flickr
I did not ponder for long. I really want a partial cover for the stern. The piece of red Packcloth I had left was 2 yards long, just enough to make the bow cover. Two more yards of Packcloth runs, yikes, $62 with shipping. In for a penny, in for 6200 pennies, so I called Seattle Fabrics to place an order.
With folks socially distancing a lot of people have undertaken sewing projects; Seattle Fabrics was going gangbusters. And, oops again, according to their records, the heat sealable material I am using is not 400 denier Packcloth; my last order for red heat sealable was for 200 denier Oxford cloth. Half the weight, and probably half the durability, but it will have to do. 4855 pennies including shipping.
I could have purchased 2 ½ or 3 yards and made the longer stern cover as originally planned, but the hull is symmetrical and, checking the template, the same size cover will fit on the stern
The waste pieces from cutting out the cover material are not actually waste.
PB200031 by Mike McCrea, on Flickr
A portion of the big red tapered “scrap” will be used to make a paddle pocket for the bow cover. The little 2” squares will get cut up for an experimental purpose to be revealed later. And red heat sealable scraps are really handy to make overhang flags for long canoes on roof racks.
Time to slave over a hot iron.
TLDR – I made a partial spray cover for the FreeFIRE using no-sew heat sealable material.
While only a day’s work (well two, I had to wait for some adhesive to set up) I will break up the process into manageable chunks for easier reading.
The bow cover will be more partial than usual; I typically bring the bow cover back to just before the utility/sail thwart, but this canoe has a combination foot brace/sail thwart, so the bow cover will be a shortie, call it 53” long. The stern portion can come all the way to the rear thwart, closer to 63”, leaving some easily accessible gear storage room behind the seat.
I do not saw. I can not sew. And our sewing machine has been broken for years. But, I have some leftover bright red heat sealable Packcloth from Seattle Fabrics, which needs only the use of an iron (and some tricky templates before cutting the fabric).
https://www.seattlefabrics.com/58-400-D-Heat-Sealable-Coated-Packcloth-2150-linear-yard_p_50.html
Some important caveats to consider before making a spray cover from heat sealable fabric:
First, without having purchased and installed the (far more elegant, custom) partial, open cockpit covers Cooke Custom Sewing made for our Wenonah Wilderness and soloized OT Penobscot I would be clueless about the basic design. And, without having installed those CCS covers using Dan’s step-by-step installation guide, even more lost about marking the locations on the hull for attaching the snaps on covers, which are installed first.
Second (& third) caveats, the Seattle Fabrics Packcloth is not the same material Cooke Custom Sewing uses for their spray cover. Not by a long shot; “It is weaker, the heavy urethane coating used to make fabric heat sealable reduces the tongue tear strength and if starts to tear it is far more likely to continue with less force”. I believe the coated nylon CCS uses has superior tear resistance when compared even to similar weight coated polyester.
The heat sealable Packcloth is heavier than coated nylon. I previously made short partial covers using heat sealable Packcloth for our Mad River Freedom Solo.

Those short partial covers weigh 1oz shy of 3lbs. The CCS covers for our longer, wider Penobscot 16 weigh a couple ounces less, and that weight includes a large center storage cover, paddle pockets at both ends and five lash straps. Gotta have lash straps for the paddles; five because I often have a double blade, single blade, furled sail and push pole to secure.

The same open cockpit design CCS covers for our Wenonah Wilderness, same two paddle pockets, large center storage cover, etc, weigh 2lbs, 10oz. If weight and tear resistant matter, coated nylon is a better choice.
Heat sealable Packcloth (or even the lighter 200D Oxford cloth – that will come up later) does not stuff. The DIY heat sealable Packcloth covers for our Freedom Solo are rolled into a cylinder and stored in an old camp chair bag. Our 3-part Cooke covers are in a CCS stuff bag the size of a youth football.
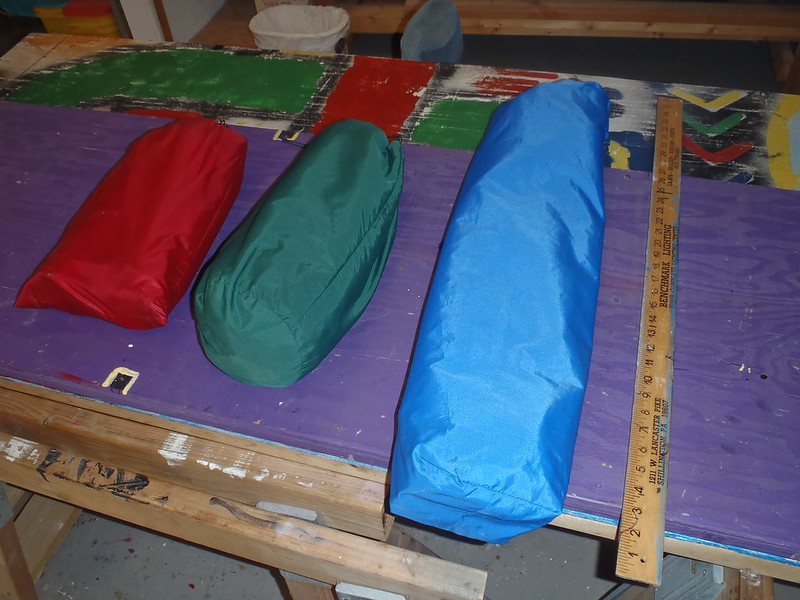
Red bag Wilderness, green bag Penobscot, blue bag DIY Packcloth
So there is all that on the demerit side to using heat sealable material. But I have bright red Seattle Fabrics material left and, as an experimental attachment, plan on using (a few) snaps combined with Dual Lock to make short partial spray covers for the FreeFIRE.
I needed to mark templates for cutting the fabric. To facilitate that I have a roll of Visqueen plastic, already cut to the same 58” width as the Packcloth. (CCS sends clear Mylar with instructions for that purpose)
First though, I need a large table to use as a cutting and ironing surface.
Our large potable platform “tables” are mostly painted 4’x8’ sheet of S1S plywood, stiffened with battens on the backside. But the 48” dimension can be problematic with 58” wide material, so I grabbed a second work platform, one of the handy 2’x8’ platforms.
Those half-width tabletops are really handy, and much easier to move around from basement to shop through three doorways; the yellow square marks the center balance, so I can carry them via a backside batten dangling from one hand.
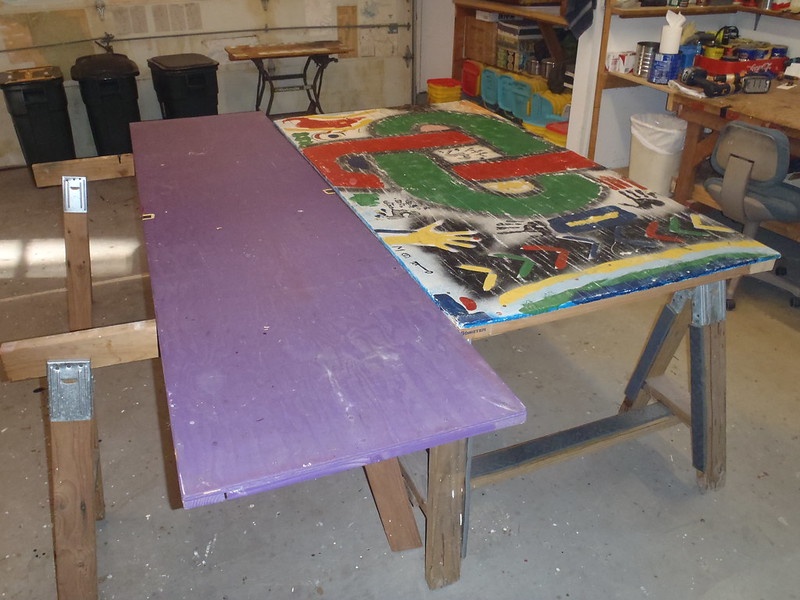
The Visqueen came folded, as did the Packcloth for less expensive shipping. Both have been stored tightly rolled on lengths of pipe to remove the creases, a good idea with any material that comes folded (hint for DougD and Chip).

First, a length of 58” wide visqueen cut to the bow cover spray cover length. I folded over and temp taped 1” heat sealable “hems” at both ends, and Sharpied a centerline for orientation before placing it atop the canoe.

The visqueen was taped on the bow and some preliminary Sharpie marks drawn; the bottom of the black side stripes, as far down as I would want the spray covers to reach.
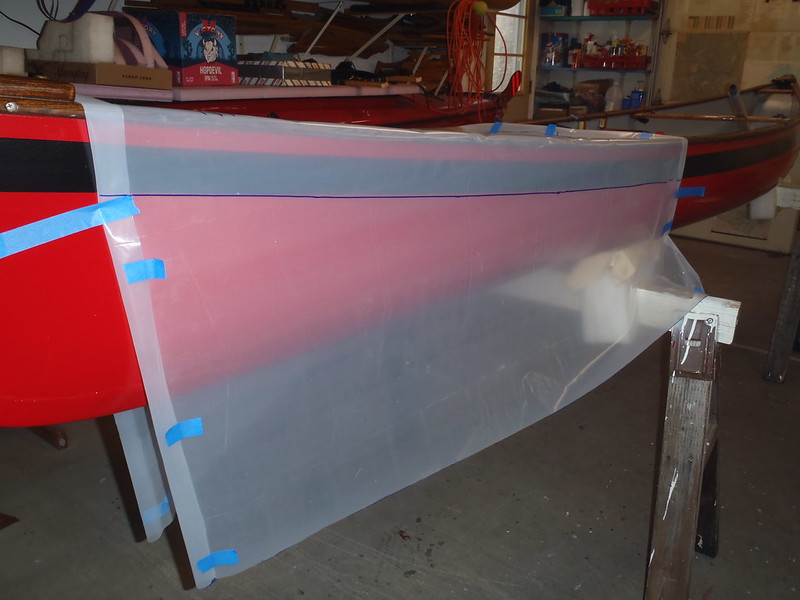
And marked the location of the carry handles and thwarts. I will be using at least a few snaps on each cover and those should not be seated directly behind the end of a thwart. I have done that in the past with DIY covers and had to remove the thwart to install the snaps. See also the reasons to use transparent visqueen plastic as a template material.

Template un-taped from the hull and back on the table I needed two more lines for the heat sealable “hems” on the long sides. I wanted a sizeable hem on those sides for doubled-over durability. My little shop iron is only 4” wide, so I went with a 3 ½” fold over hem, Sharpie-ing that fold over line below/inside the stripe line.

To make certain I didn’t cut the wrong line (not that I’ve ever done something like that) I crossed out the side stripe line, added a dotted line for the four inch fold-over-to-this-point (which will later be Sharpied on the heat sealable side of the material) and cut out the rough template.

That is a fair amount of material for a small bow spray shield, 55” long x 40” at the wide end.
A very “rough” template. For starters the fold over heat sealed hems become peculiarly shaped with angled material; when properly cut to fold over two corners sticks out in pointy dog ears, and two corners come up a bit short.


Helpfully the excess /| on the one corner is essentially the additional |/ needed on the other, just cut it off and tape it on the other side.

With the little slices and dog ears shaped there remain just a few more weirdo cuts to make on the template. The fabric only adheres heat sealable side to heat sealable side, and I will need to fold over and iron the 1” hems on the ends.
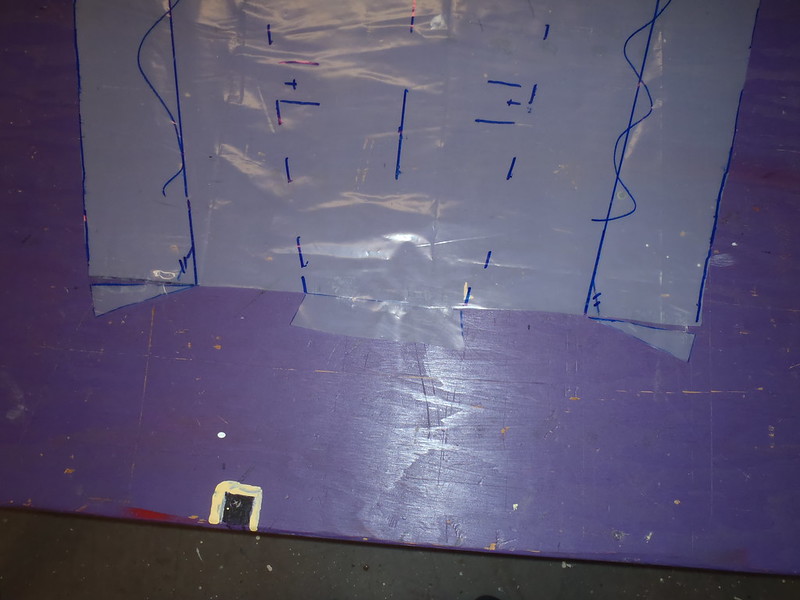

Last step with the bow cover template, toss it over the bow for a look see, and mark the snap locations on the plastic. The experimental plan is to use both Dual Lock and snaps. I found the snaps on a simple splash and drip cover, with no-stress from a spray skirt tunnel, can be spaced at least 10” or 12” apart, but with the Dual Lock augmentation I am planning only three snaps on each side of the bow cover, spaced 25” apart.
My theory is that having a snap at each end and, eh, one in the middle, will help align the Dual Lock for more accurate press fastening. I have a hopefully strategic plan for the Dual Lock installation as well.
Time to cut some red heat sealable fabric. Well crapola. I thought I had a lot more red heat sealable fabric, but have only enough for the bow cover. I will cut and install this one and ponder buying more.

I did not ponder for long. I really want a partial cover for the stern. The piece of red Packcloth I had left was 2 yards long, just enough to make the bow cover. Two more yards of Packcloth runs, yikes, $62 with shipping. In for a penny, in for 6200 pennies, so I called Seattle Fabrics to place an order.
With folks socially distancing a lot of people have undertaken sewing projects; Seattle Fabrics was going gangbusters. And, oops again, according to their records, the heat sealable material I am using is not 400 denier Packcloth; my last order for red heat sealable was for 200 denier Oxford cloth. Half the weight, and probably half the durability, but it will have to do. 4855 pennies including shipping.
I could have purchased 2 ½ or 3 yards and made the longer stern cover as originally planned, but the hull is symmetrical and, checking the template, the same size cover will fit on the stern
The waste pieces from cutting out the cover material are not actually waste.

A portion of the big red tapered “scrap” will be used to make a paddle pocket for the bow cover. The little 2” squares will get cut up for an experimental purpose to be revealed later. And red heat sealable scraps are really handy to make overhang flags for long canoes on roof racks.
Time to slave over a hot iron.