G
Guest
Guest
Bottom inspection of skid plate test patches.
There is no sense in trying to weigh the individual pieces now that I have cracked, broken and abraded sections away. But after seeing the undersides of the peeled-off kevlar felt and S-glass/Dynel patches, I did want a look at the bottoms of the other 2-ply sandwiches.
#4, carbon fiber under Dynel. Fully saturated on the bottom, the twill weave is visible. It is carbon fiber black with black tinted epoxy (the white is flash glare) but is smooth to the touch and seems well saturated. Still, black on black, who knows?
P3290027 by Mike McCrea, on Flickr
#6, kevlar tape under Dynel. That is the one I was most curious about, after seeing the poor bottom saturation on the kevlar felt pieces. There was one still kevlar-yellow area near the molded bend angle in the siding.
P3290030 by Mike McCrea, on Flickr
#7, E-glass under Dynel. There is a small crescent of white E-glass showing through, again at the siding angle. Those under saturated angles atop the vinyl siding may be indicative of unseen issues with hand laid cloth and epoxy skid plates on stem areas curves where it is more difficult to maintain a layer of epoxy while laying cloth.
P3290032 by Mike McCrea, on Flickr
#8, single layer Dynel. Smooth and fully epoxy saturated, with a (very) few champagne-bubble sized pock marks.
P3290034 by Mike McCrea, on Flickr
I have always thought that I was too-heavy-hand with epoxy; painting an uber thick coat, laying fabric, painting a thick coat of epoxy on top and then peel ply hand compressing. But I’ve never had a good look at the bottoms of fabrics I have hand laid before. Not something you usually get to see.
I was not heavy enough with any of the kevlar felts, and it makes me reconsider the “lighter epoxied is better” theory; although that more lightly epoxied kevlar felt does seem to perform better under impact. I was closer to full saturation with the kevlar tape and closer still with the 8oz E-glass.
Those bottom saturation differences would not have been as visible without the graphite powder and black pigment, showing the under-saturated kevlar yellow and E-glass white fabric colors.
I already recognized the weight difference achievable with vacuum bagged boats; I now have a better appreciation of the more thorough epoxy saturation with vacuum bagging, in the layers you don’t usually get to see.
With all of the skid plate materials removed I have one more torture test to perform.
There is no sense in trying to weigh the individual pieces now that I have cracked, broken and abraded sections away. But after seeing the undersides of the peeled-off kevlar felt and S-glass/Dynel patches, I did want a look at the bottoms of the other 2-ply sandwiches.
#4, carbon fiber under Dynel. Fully saturated on the bottom, the twill weave is visible. It is carbon fiber black with black tinted epoxy (the white is flash glare) but is smooth to the touch and seems well saturated. Still, black on black, who knows?
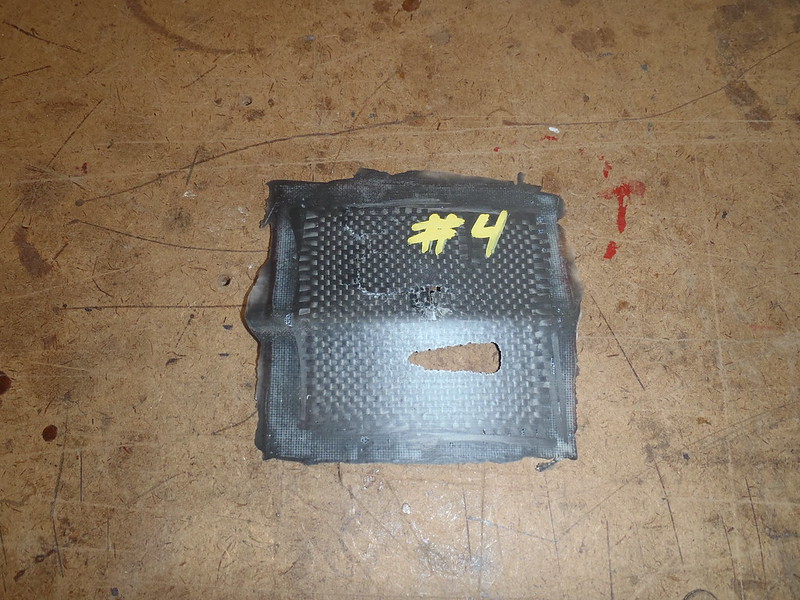
#6, kevlar tape under Dynel. That is the one I was most curious about, after seeing the poor bottom saturation on the kevlar felt pieces. There was one still kevlar-yellow area near the molded bend angle in the siding.
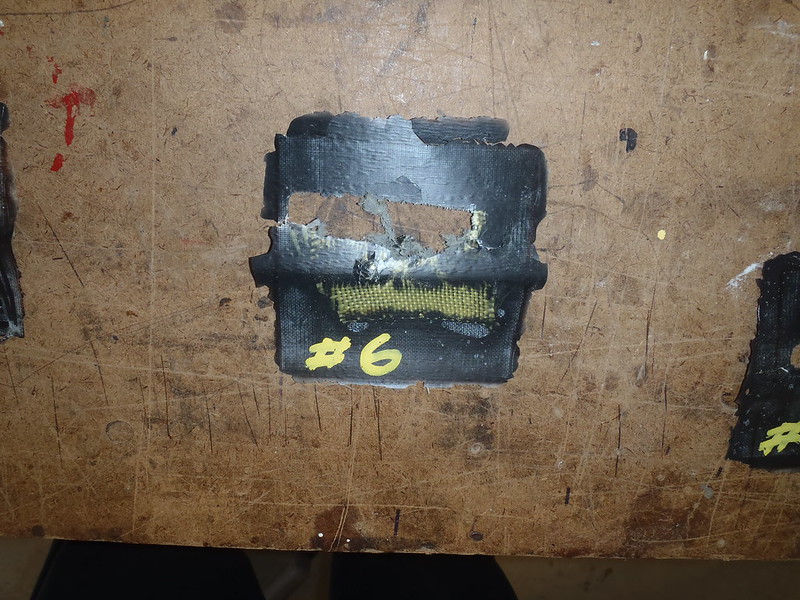
#7, E-glass under Dynel. There is a small crescent of white E-glass showing through, again at the siding angle. Those under saturated angles atop the vinyl siding may be indicative of unseen issues with hand laid cloth and epoxy skid plates on stem areas curves where it is more difficult to maintain a layer of epoxy while laying cloth.
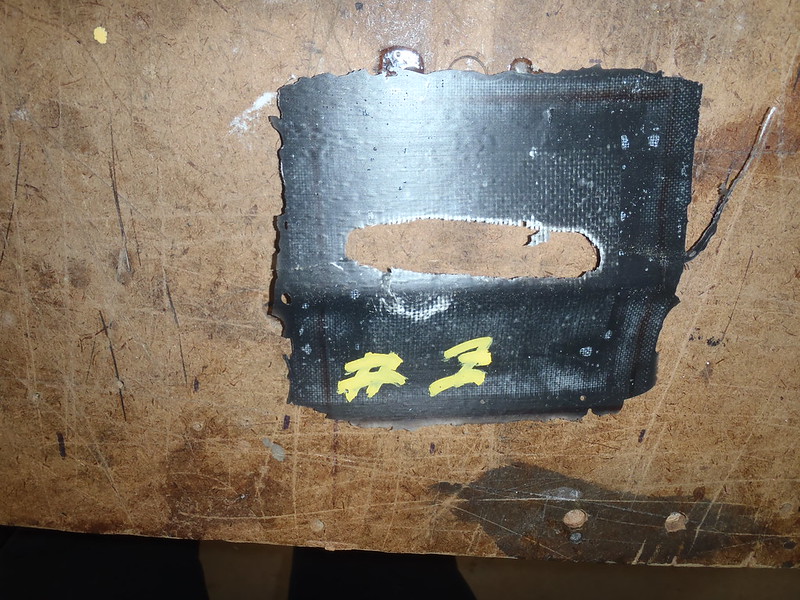
#8, single layer Dynel. Smooth and fully epoxy saturated, with a (very) few champagne-bubble sized pock marks.
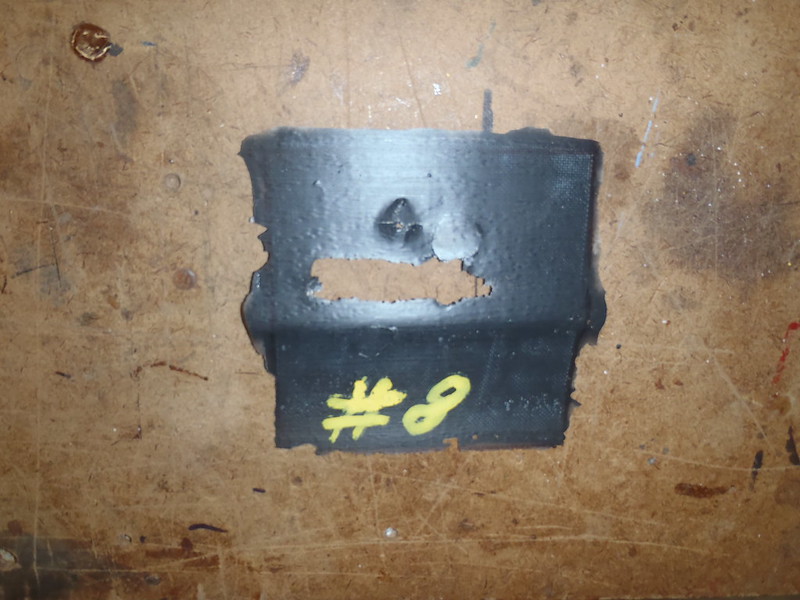
I have always thought that I was too-heavy-hand with epoxy; painting an uber thick coat, laying fabric, painting a thick coat of epoxy on top and then peel ply hand compressing. But I’ve never had a good look at the bottoms of fabrics I have hand laid before. Not something you usually get to see.
I was not heavy enough with any of the kevlar felts, and it makes me reconsider the “lighter epoxied is better” theory; although that more lightly epoxied kevlar felt does seem to perform better under impact. I was closer to full saturation with the kevlar tape and closer still with the 8oz E-glass.
Those bottom saturation differences would not have been as visible without the graphite powder and black pigment, showing the under-saturated kevlar yellow and E-glass white fabric colors.
I already recognized the weight difference achievable with vacuum bagged boats; I now have a better appreciation of the more thorough epoxy saturation with vacuum bagging, in the layers you don’t usually get to see.
With all of the skid plate materials removed I have one more torture test to perform.