- Joined
- Aug 10, 2018
- Messages
- 1,511
- Reaction score
- 2,189
The game plan coming into winter this year was to finish the Raven that I'd started and to get another solo finished before spring. This one will be built from White Pine & Cherry. These woods should look nice but I expect them to be a more bland combination than the Tamarack / Sassafras or even the Aspen / Cherry that I've used previously and that's good... I've been wanting to color the outside of a stripper and a more mundane wood might be just the ticket.
For a few years now, I've had pdf plans for a Merlin (from Northwest Canoe) and, while I think it will be a very similar hull to the Freedom solo that I built (maybe a little more rocker and a little less freeboard), I like the Freedom and I see no harm in another boat that's similar to one I already like. Besides, I'd set the Freedom up for tripping with the seat moved really far to the rear and I can set the Merlin up as a day tripper with the seat more centralized.
I'm also planning on hanging this seat from the gunwales because I haven't done that yet and I should try it. I'll eventually build a hull with inner and outer stems for that same reason but it won't be this hull. This one will be stemless and already has enough experimental stuff planned IMO
The plans were pdfs and the local print shops could print them but only on heavy weight paper that was just short of card stock. One of them (the one I use for waterproof maps) suggested finding someone able to print blueprints so I contacted an architect friend. He loved the idea of building a canoe this way, had the plans printed within hours and refused payment as long as I sent him pictures of the canoe.
Deal.
There was some question about the scale (I guess engineering drawings typically include a letter that indicates scale and it was missing?) so my first order of business was to lay out the plans and make a few measurements to verify the size.
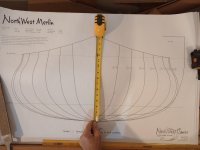
Satisfied that we were in the right ballpark, the next item of business was the shop.
I'd put bead on a mountain of White Pine & some Cherry strips when I was milling the Larch for the last build and the shaper was still set up for the coves so I spent about 2 1/2 hours cutting the coves and trimming off any places where the strip had been cut thin or the bead or cove had not cut well. That done, I moved all strips to the infeed table near the strongback and moved the Raven to the now empty offloading table.
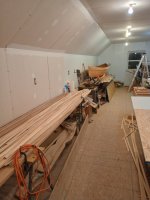
That being accomplished, I now had the strongback empty for laying out station molds and I ran to the local Lowe's for 2 4x8 sheets of 1/2" OSB and had them cut them in 1/2 for me (I like buying local but neither of the mom & pop lumber yards near me have a panel saw to cut the sheets).
I extended the center line to the edge of the paper, cut two 3/8 inch holes in that center line so that I could align it with the center line on the OSB and used the factory edge of the sheet as an additional guide for square. I measured out 5 inches from each side of the centerline for the form bases & left them long so that the stems will be at least 3 inches above the strongback. (the reason for this will be clear just before I'm ready to glass)
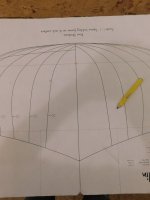
In all, I spent about 5 (very snowy) hours in the shop today and I'm ready to cut out the forms. I was hoping to do that outside & reduce the amount of dust in the shop but that's unlikely given the short range forecast (and I'm not waiting for nicer weather).
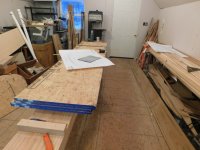
A keen observer will note that I've moved the band saw. This was necessary because the Pine strips are 14 feet (longest strips I've used so far) and the saw was in the way. That same keen eye might note that I've drawn a line 12 inches up from the factory edge (bottom of the form). That will be used to align the forms with a laser level once they're cut out & sanded to the pattern lines. (hopefully tomorrow but we'll see)
For a few years now, I've had pdf plans for a Merlin (from Northwest Canoe) and, while I think it will be a very similar hull to the Freedom solo that I built (maybe a little more rocker and a little less freeboard), I like the Freedom and I see no harm in another boat that's similar to one I already like. Besides, I'd set the Freedom up for tripping with the seat moved really far to the rear and I can set the Merlin up as a day tripper with the seat more centralized.
I'm also planning on hanging this seat from the gunwales because I haven't done that yet and I should try it. I'll eventually build a hull with inner and outer stems for that same reason but it won't be this hull. This one will be stemless and already has enough experimental stuff planned IMO
The plans were pdfs and the local print shops could print them but only on heavy weight paper that was just short of card stock. One of them (the one I use for waterproof maps) suggested finding someone able to print blueprints so I contacted an architect friend. He loved the idea of building a canoe this way, had the plans printed within hours and refused payment as long as I sent him pictures of the canoe.
Deal.
There was some question about the scale (I guess engineering drawings typically include a letter that indicates scale and it was missing?) so my first order of business was to lay out the plans and make a few measurements to verify the size.
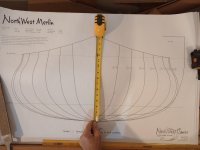
Satisfied that we were in the right ballpark, the next item of business was the shop.
I'd put bead on a mountain of White Pine & some Cherry strips when I was milling the Larch for the last build and the shaper was still set up for the coves so I spent about 2 1/2 hours cutting the coves and trimming off any places where the strip had been cut thin or the bead or cove had not cut well. That done, I moved all strips to the infeed table near the strongback and moved the Raven to the now empty offloading table.
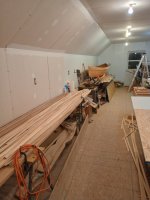
That being accomplished, I now had the strongback empty for laying out station molds and I ran to the local Lowe's for 2 4x8 sheets of 1/2" OSB and had them cut them in 1/2 for me (I like buying local but neither of the mom & pop lumber yards near me have a panel saw to cut the sheets).
I extended the center line to the edge of the paper, cut two 3/8 inch holes in that center line so that I could align it with the center line on the OSB and used the factory edge of the sheet as an additional guide for square. I measured out 5 inches from each side of the centerline for the form bases & left them long so that the stems will be at least 3 inches above the strongback. (the reason for this will be clear just before I'm ready to glass)
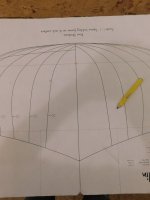
In all, I spent about 5 (very snowy) hours in the shop today and I'm ready to cut out the forms. I was hoping to do that outside & reduce the amount of dust in the shop but that's unlikely given the short range forecast (and I'm not waiting for nicer weather).
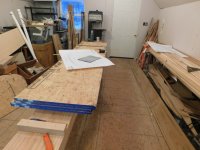
A keen observer will note that I've moved the band saw. This was necessary because the Pine strips are 14 feet (longest strips I've used so far) and the saw was in the way. That same keen eye might note that I've drawn a line 12 inches up from the factory edge (bottom of the form). That will be used to align the forms with a laser level once they're cut out & sanded to the pattern lines. (hopefully tomorrow but we'll see)