G
Guest
Guest
The skid plates on my favorite RX big boy tripper, the soloized Penobscot 16, are kevlar felt with OT urethane resin, still firm and flush-ish to the hull. That was one of the last kevlar felt skid plate kits I ever installed; even done properly, smoothed down with beveled edges, I curse the day every time I see it.
I did a decent job of smoothing it and faring down the tall felt edges as the epoxy set up, but did not think to pigment the yellow kevlar felt. Just adding a dab of green pigment in the resin saturating that kevlar felt would have worn down more hull matching and less fugly.
With the attention to detail application technique that 16 year old skid plate has held up well. I did patch some chips and recoat it with pigmented epoxy some years ago, and it is drag and scrape worn nearly baby butt smooth, with a couple new chips of felt busted out, and is again getting down to kev felt yellow showing.
PB040024 by Mike McCrea, on Flickr
One skid plate application trick I have learned; once you have the process down it is much faster to do two boats at once rather than doing one at a time. If the fabric and epoxy and mixing pots, brush and tape and etc are already out, doing skid plates on two boats is only a little more work than doing one. Eh, 2x prep work, but even that is bit of a time saver doubling up.
Which second canoe to bring in? I did a (very) rudimentary skid plate experiment years ago, at the end of my kev felt skid plate era. We did four canoes at once, two friend’s canoes using two Old Town skid plate kits, with the leftovers of excess kev felt and urethane resin going on our Freedom Solo and Odyssey.
The MRC Freedom Solo got two short kev felt and OT urethane epoxy skids, and the Mohawk Odyssey more experimentally one felt and one no-fabric just urethane resin skid (ran out of extra felt from the kits), using up every bit of excess resin. The Freedom Solo needs help, but the Odyssey is crying out for skid plate refurbishment.
The Mohawk Odyssey 14 is my favorite canoe for shallow water streams; I swear it would grumblebump over a dewy lawn. It is likewise wonderfully stable traversing “step out” logs. Love that little canoe for shallow waters and swampy applications.
Kevlar felt and urethane resin skid plate on the Odyssey
PB040027 by Mike McCrea, on Flickr
Urethane resin only skid plate
PB040025 by Mike McCrea, on Flickr
That urethane-only skid plate held up surprisingly well, but is worn vanished thin on the edges and up the centerline. It is on the bow and less susceptible to abuse when dragging the canoe around strainers. Those two will do as the next renovated skid plate applications.
The well-done kevlar felt skid plates on the Penobscot, so well done I have little hope of chiseling or grinding them off, got a coat of straight G/flex, graphite powder and black pigment.
Both ends of the Odyssey got a layer of Dynel, graphite powder and pigment. The no-fabric end was originally done with thickening in the pot leftover urethane resin, so thick it was raised 1/8” gloppy at one edge. RO sander knocked that raised glop edge down flush. 60 grit disc needed; that Old Town urethane resin is some tough stuff.
Prep work on two boats took a while. I have never bothered to keep track of time when installing skid plates, but what the hell.
Debridement/scrubbing/cleaning the old skid plates – 10 minutes
Lay out/staging the epoxies, brushes, cups, gloves, graphite power, pigment – 10 minutes tops (there may have been a let’s-think-ahead-about-the-sequence beer in that time span).
PB040030 by Mike McCrea, on Flickr
Cut paper templates for the Dynel fabric size and shape, cut the Dynel, cut the release treated peel ply – 20 minutes. I even remembered to Sharpie a centerline on the Dynel to help my aim down the keel line, and cut a couple inch slit up the narrow end of the Dynel so the fabric could fold over more neatly at the curved tip.
PB040032 by Mike McCrea, on Flickr
Lay the Dynel fabric on the Odyssey for a test fit and tape out the perimeter, and tape out the Penobscot. Paper half way up the 1[SUP]st[/SUP] perimeter of tape, 2[SUP]nd[/SUP] run of tape over the edge of the newspaper – 35 minutes. That chore was the longest single time demand, and yet surprisingly fast this time.
It used to take me that long to tape and paper mask a single canoe; if nothing else I have gotten efficient at that part. I muscle-memory know the best order to lay the tape and paper for when it comes removal time, know where to most conveniently leave pull-tabs on the tape, and can even cut the curves in the stem end of the masking paper by eyeballing, without tracing a line.
PB040034 by Mike McCrea, on Flickr
PB040035 by Mike McCrea, on Flickr
Mixing the epoxy pots, painting on an undercoat of resin, laying the Dynel fabric, top coating with G/flex, walk away and begin Sharpie marking the ends of the drips – 30 (ish) minutes; I didn’t check the time until I was painting on the first pot .
PB050039 by Mike McCrea, on Flickr
I (mostly) remembered to keep the brush and pot over the skid plate areas at all times, so I (mostly) didn’t waste epoxy by dripping it on the floor or my shoes.
The rough texture of the Dynel develops quickly. Without using peel ply that surface gets much rougher as the epoxy sets up.
The two Dynel fabric plates and the two G/flex on existing kevlar took 4 small batches of epoxy, each batch about 1/3 of a cup by volume. Total resin used for both boats, 1 1/3 cup, or about 11 oz, including some excess that dripped down onto the paper mask, and the dregs of the last pot applied to another epoxy need project. Yes, this time I actually remembered to prep a use for any leftover epoxy in the last pot. Really need to get better at remembering that waste-not part.
The resin undercoat for the Dynel was roughly fifty-fifty West 105/206 and G/flex (plus a half teaspoon of graphite powder and dab of pigment per pot). The 105/206 and G/flex mix made it easier to saturate the Dynel once laid and gloved hand compressed before the peel ply went on. The top coats on both boats was 100% G/flex with graphite and pigment.
The runs had stopped dripping in 40 minutes observation and I could pull the paper and outer layer of tape; the inner tape perimeter gives me one last look at the epoxied edges. Five undrippy minutes later I pulled that last tape surround to lay on the peel ply.
PB050046 by Mike McCrea, on Flickr
Release treated peel ply laid atop the Dynel. I wished I had helping hands to hold and align one end of the peel ply while laying it in place. Gloved hand compressed and further compressed with the hard surface roller - 5 minutes.
PB050050 by Mike McCrea, on Flickr
Next morning I pulled the release treated peel ply on the Dynel skid plates
PB070054 by Mike McCrea, on Flickr
Total elapsed time: 2 hours 40 minutes, with some of that baby sitting the epoxy and beer drinking time.
The painting/topcoating plan is to use something better than black enamel this time.
PB070055 by Mike McCrea, on Flickr
I scored a discount can of black EZPoxy; black seems an unloved epoxy paint color. I can’t imagine using black on anything other than graphite powder and black pigment skid plates, but for topcoating already near Vantablack skid plates, why not.
The Freedom Solo needs more generously sized Dynel skid plates laid atop the shortie kev felt and OT resin leftovers, and we have a couple of glass & nylon decked canoes that could use some stem scrape protection.
I wonder how many boats I can line up side by side in the shop for a day of masking and black EZPoxy skid plate painting.
We shall see; it would be easiest to tape and paper and EZPoxy paint a bunch of boats at once. I think I can go four-wide in the shop for skid plate taping and painting.
I could probably skip the painting; I suspect (don’t know) that the graphite powder and pigment provide some UV protection. But there is some red hull peeking through the blackened epoxy on the Odyssey where there is no cloth to soak up color, and even with my heavy epoxy hand and peel ply compression a bit of fabric weave is, as always, visible right at the steepest curve of the tip where the epoxy tends to run away.
A coat of epoxy paint should hide both visual flaws.
I did a decent job of smoothing it and faring down the tall felt edges as the epoxy set up, but did not think to pigment the yellow kevlar felt. Just adding a dab of green pigment in the resin saturating that kevlar felt would have worn down more hull matching and less fugly.
With the attention to detail application technique that 16 year old skid plate has held up well. I did patch some chips and recoat it with pigmented epoxy some years ago, and it is drag and scrape worn nearly baby butt smooth, with a couple new chips of felt busted out, and is again getting down to kev felt yellow showing.

One skid plate application trick I have learned; once you have the process down it is much faster to do two boats at once rather than doing one at a time. If the fabric and epoxy and mixing pots, brush and tape and etc are already out, doing skid plates on two boats is only a little more work than doing one. Eh, 2x prep work, but even that is bit of a time saver doubling up.
Which second canoe to bring in? I did a (very) rudimentary skid plate experiment years ago, at the end of my kev felt skid plate era. We did four canoes at once, two friend’s canoes using two Old Town skid plate kits, with the leftovers of excess kev felt and urethane resin going on our Freedom Solo and Odyssey.
The MRC Freedom Solo got two short kev felt and OT urethane epoxy skids, and the Mohawk Odyssey more experimentally one felt and one no-fabric just urethane resin skid (ran out of extra felt from the kits), using up every bit of excess resin. The Freedom Solo needs help, but the Odyssey is crying out for skid plate refurbishment.
The Mohawk Odyssey 14 is my favorite canoe for shallow water streams; I swear it would grumblebump over a dewy lawn. It is likewise wonderfully stable traversing “step out” logs. Love that little canoe for shallow waters and swampy applications.
Kevlar felt and urethane resin skid plate on the Odyssey
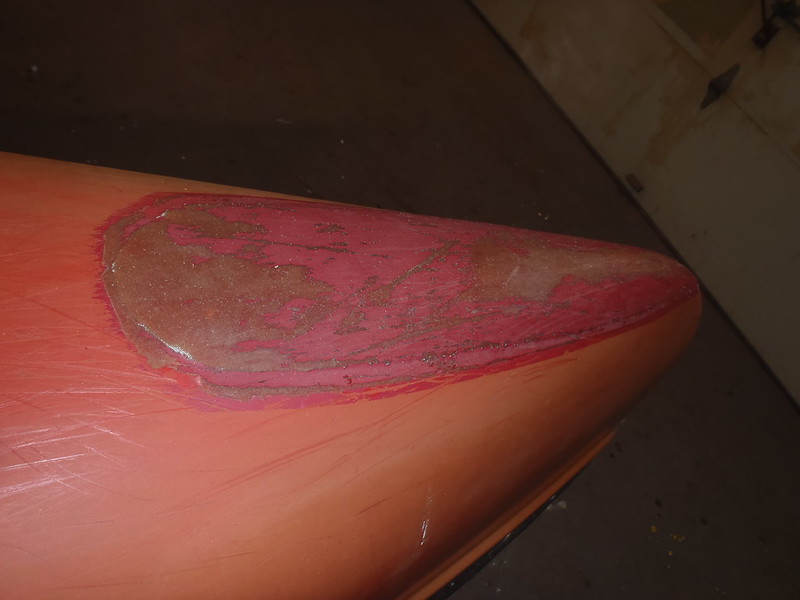
Urethane resin only skid plate

That urethane-only skid plate held up surprisingly well, but is worn vanished thin on the edges and up the centerline. It is on the bow and less susceptible to abuse when dragging the canoe around strainers. Those two will do as the next renovated skid plate applications.
The well-done kevlar felt skid plates on the Penobscot, so well done I have little hope of chiseling or grinding them off, got a coat of straight G/flex, graphite powder and black pigment.
Both ends of the Odyssey got a layer of Dynel, graphite powder and pigment. The no-fabric end was originally done with thickening in the pot leftover urethane resin, so thick it was raised 1/8” gloppy at one edge. RO sander knocked that raised glop edge down flush. 60 grit disc needed; that Old Town urethane resin is some tough stuff.
Prep work on two boats took a while. I have never bothered to keep track of time when installing skid plates, but what the hell.
Debridement/scrubbing/cleaning the old skid plates – 10 minutes
Lay out/staging the epoxies, brushes, cups, gloves, graphite power, pigment – 10 minutes tops (there may have been a let’s-think-ahead-about-the-sequence beer in that time span).

Cut paper templates for the Dynel fabric size and shape, cut the Dynel, cut the release treated peel ply – 20 minutes. I even remembered to Sharpie a centerline on the Dynel to help my aim down the keel line, and cut a couple inch slit up the narrow end of the Dynel so the fabric could fold over more neatly at the curved tip.

Lay the Dynel fabric on the Odyssey for a test fit and tape out the perimeter, and tape out the Penobscot. Paper half way up the 1[SUP]st[/SUP] perimeter of tape, 2[SUP]nd[/SUP] run of tape over the edge of the newspaper – 35 minutes. That chore was the longest single time demand, and yet surprisingly fast this time.
It used to take me that long to tape and paper mask a single canoe; if nothing else I have gotten efficient at that part. I muscle-memory know the best order to lay the tape and paper for when it comes removal time, know where to most conveniently leave pull-tabs on the tape, and can even cut the curves in the stem end of the masking paper by eyeballing, without tracing a line.

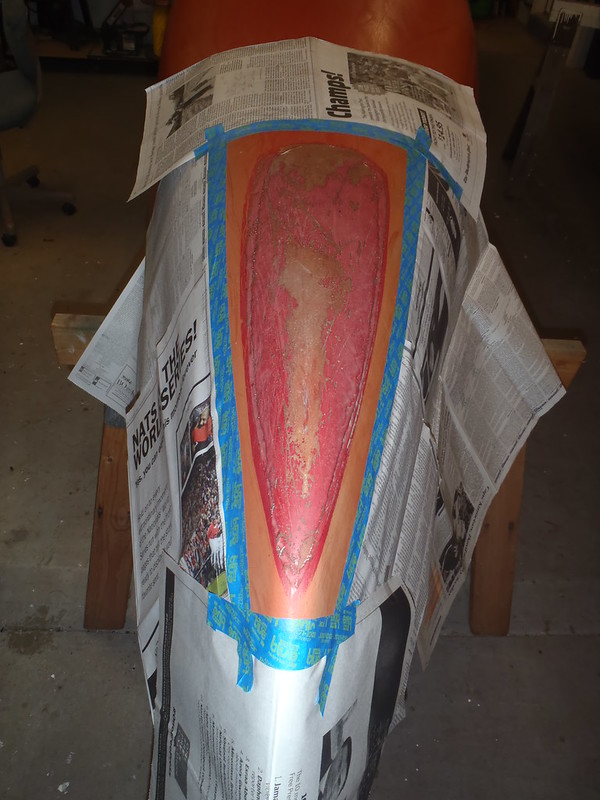
Mixing the epoxy pots, painting on an undercoat of resin, laying the Dynel fabric, top coating with G/flex, walk away and begin Sharpie marking the ends of the drips – 30 (ish) minutes; I didn’t check the time until I was painting on the first pot .

I (mostly) remembered to keep the brush and pot over the skid plate areas at all times, so I (mostly) didn’t waste epoxy by dripping it on the floor or my shoes.
The rough texture of the Dynel develops quickly. Without using peel ply that surface gets much rougher as the epoxy sets up.
The two Dynel fabric plates and the two G/flex on existing kevlar took 4 small batches of epoxy, each batch about 1/3 of a cup by volume. Total resin used for both boats, 1 1/3 cup, or about 11 oz, including some excess that dripped down onto the paper mask, and the dregs of the last pot applied to another epoxy need project. Yes, this time I actually remembered to prep a use for any leftover epoxy in the last pot. Really need to get better at remembering that waste-not part.
The resin undercoat for the Dynel was roughly fifty-fifty West 105/206 and G/flex (plus a half teaspoon of graphite powder and dab of pigment per pot). The 105/206 and G/flex mix made it easier to saturate the Dynel once laid and gloved hand compressed before the peel ply went on. The top coats on both boats was 100% G/flex with graphite and pigment.
The runs had stopped dripping in 40 minutes observation and I could pull the paper and outer layer of tape; the inner tape perimeter gives me one last look at the epoxied edges. Five undrippy minutes later I pulled that last tape surround to lay on the peel ply.
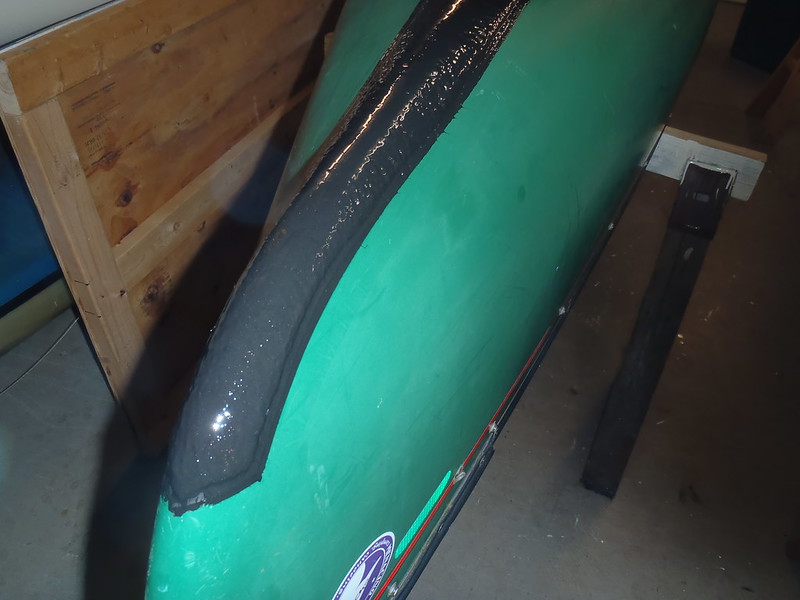
Release treated peel ply laid atop the Dynel. I wished I had helping hands to hold and align one end of the peel ply while laying it in place. Gloved hand compressed and further compressed with the hard surface roller - 5 minutes.

Next morning I pulled the release treated peel ply on the Dynel skid plates

Total elapsed time: 2 hours 40 minutes, with some of that baby sitting the epoxy and beer drinking time.
The painting/topcoating plan is to use something better than black enamel this time.

I scored a discount can of black EZPoxy; black seems an unloved epoxy paint color. I can’t imagine using black on anything other than graphite powder and black pigment skid plates, but for topcoating already near Vantablack skid plates, why not.
The Freedom Solo needs more generously sized Dynel skid plates laid atop the shortie kev felt and OT resin leftovers, and we have a couple of glass & nylon decked canoes that could use some stem scrape protection.
I wonder how many boats I can line up side by side in the shop for a day of masking and black EZPoxy skid plate painting.
We shall see; it would be easiest to tape and paper and EZPoxy paint a bunch of boats at once. I think I can go four-wide in the shop for skid plate taping and painting.
I could probably skip the painting; I suspect (don’t know) that the graphite powder and pigment provide some UV protection. But there is some red hull peeking through the blackened epoxy on the Odyssey where there is no cloth to soak up color, and even with my heavy epoxy hand and peel ply compression a bit of fabric weave is, as always, visible right at the steepest curve of the tip where the epoxy tends to run away.
A coat of epoxy paint should hide both visual flaws.