Well, as Brian (AKA "Cruiser") pointed out in his thread: https://www.canoetripping.net/threads/building-some-new-wood-composite-paddles-for-2020.120222/ with every new canoe comes the need for a couple new paddles. Having completed my first stripper build in late fall, I felt the need to build a couple paddles. What originally started out as a plan to build two straight shaft, and two bent shaft, in the same build was actually broken down into two separate builds, back to back. I did this, since it was my first paddle build, I decided I'd rather mess up two than four. I did the straight shaft first, then the bent shaft.
I'm not going to go into much detail on the processes I used from Brian's thread. The information there is awesome. I did make a few "tweaks" based on my equipment, and thoughts I had along the way. I'll go into a bit more detail on my individual modifications. Nothing special about the blades; I'm saving crazy blade designs for another build, now that I feel fairly confident in my process. Here's the finished paddles, then I'll go through how I got there. I made these for myself and my wife. I'm 5'-9", she's 5'-5". Mine are both 34" shaft, hers are 32" (straight) & 32.5 (bent).
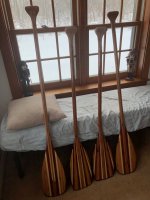
Not going into a lot of detail on shaft sizing, primarily because I'm not an expert. My normal paddles are all about 5 hours away, and I wasn't sure when I'd see them again, and I was anxious to start the build, so I forged ahead with best guess, and measuring the shaft on the head method, with both arms at 90 degrees like a goal post. I came up with 34" for me, 32" for my wife. I added a 1/2" to the length of her bent shaft because I shortened her blade a bit. Next, I decided on blade design. I prefer a shorter blade for general paddling, and found an "ashes" guide blade design that I liked. For the bent shaft, I looked at sizes of a variety of blades out there. Going off of several Bending Branches blade sizes, I drew my own.
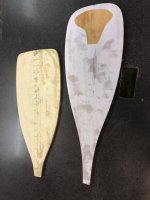
To do my own blade design, I started with a centerline running the length of the blade, marked the width of the shaft, the max width of the blade, and the desired length. I set my max width at 8 1/4", length of 19 1/2". I then marked off lines at 1" spacing, across the blade, perpendicular to the center line. I drew the rough shape of the blade, using a combination of curves, and the profile of the guide blade as a starting point. My target was 120 sq. in.
Once I had the rough shape, I measured from the center line to the profile, at approximately the center of each 1" space. I used a dial caliper, for accuracy, and to get all measurements in decimal inches. After I measured all the spaces, I added all measurements, multiplied by 2, and this gave me a very close approximation of blade area. I tweeked design until I was at 120 sq. in.
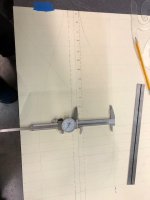
So bent shaft blades ended up being 19 1/2", Straight shaft blades 24". I decided to make all shafts 62" long rough, to allow for trimming later.
Given I realized I could probably sell these for pretty close to McDonald's wages, when I gear up for mass production this shaft size will allow for most single blade paddles for me. If I get into beaver tail or otter tail, I'd have to adjust accordingly. Time to make the shafts.
I'm not going to go into much detail on the processes I used from Brian's thread. The information there is awesome. I did make a few "tweaks" based on my equipment, and thoughts I had along the way. I'll go into a bit more detail on my individual modifications. Nothing special about the blades; I'm saving crazy blade designs for another build, now that I feel fairly confident in my process. Here's the finished paddles, then I'll go through how I got there. I made these for myself and my wife. I'm 5'-9", she's 5'-5". Mine are both 34" shaft, hers are 32" (straight) & 32.5 (bent).
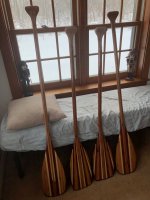
Not going into a lot of detail on shaft sizing, primarily because I'm not an expert. My normal paddles are all about 5 hours away, and I wasn't sure when I'd see them again, and I was anxious to start the build, so I forged ahead with best guess, and measuring the shaft on the head method, with both arms at 90 degrees like a goal post. I came up with 34" for me, 32" for my wife. I added a 1/2" to the length of her bent shaft because I shortened her blade a bit. Next, I decided on blade design. I prefer a shorter blade for general paddling, and found an "ashes" guide blade design that I liked. For the bent shaft, I looked at sizes of a variety of blades out there. Going off of several Bending Branches blade sizes, I drew my own.
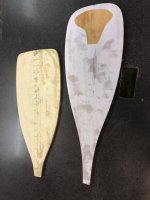
To do my own blade design, I started with a centerline running the length of the blade, marked the width of the shaft, the max width of the blade, and the desired length. I set my max width at 8 1/4", length of 19 1/2". I then marked off lines at 1" spacing, across the blade, perpendicular to the center line. I drew the rough shape of the blade, using a combination of curves, and the profile of the guide blade as a starting point. My target was 120 sq. in.
Once I had the rough shape, I measured from the center line to the profile, at approximately the center of each 1" space. I used a dial caliper, for accuracy, and to get all measurements in decimal inches. After I measured all the spaces, I added all measurements, multiplied by 2, and this gave me a very close approximation of blade area. I tweeked design until I was at 120 sq. in.
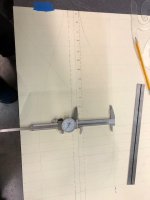
So bent shaft blades ended up being 19 1/2", Straight shaft blades 24". I decided to make all shafts 62" long rough, to allow for trimming later.
Given I realized I could probably sell these for pretty close to McDonald's wages, when I gear up for mass production this shaft size will allow for most single blade paddles for me. If I get into beaver tail or otter tail, I'd have to adjust accordingly. Time to make the shafts.