Well, it was bound to happen sooner or later....between general outdoor stuff, canoeing stuff, climbing stuff, camping stuff etc I have been working myself up for some time to learn to sew. So I spent some time learning just enough to get myself in trouble and ordered a few kinds each of canvas, packcloth, ripstop, needles and such and started tinkering. And as I live in an area with a lot of used commercial/industrial sewing machines floating around I started trying to get my brain cell wrapped around the many kinds of those and narrow down what I might be looking out for.
I have a good sized heavy canvas tarp that saw a lot of years of use as a dining fly for scout and family camping. In fact it still gets used for drive up camping and such. But my pole bag has gotten pretty rough. It was after all made from lightweight tent canvas 25-30 years ago.....
One of the canvas' I had is natural color 72" wide 10 ounce canvas so I looked at what I'd change from the old bag and added some length, width and a stout pocket to hold the 16 or so 12" GI surplus aluminum pins I tote around with the tarp.
I used what I had on hand so the handle is a piece of 1" climbing tubular nylon, the handle gussets were cut from 1-1/2" canoe seat webbing with a hot knife, the drawstring is a stout elastic cord I had on hand etc. The side pocket has some pleats as one end of the pins is a lot wider than the other and the pocket has extra length to hold some extra guy lines etc.
I used a size 90/14 needle with heavy polyester thread and it wanted to wander as it stitched due to flexing in the needle and the needle shaft of my wife's sewing machine but truthfully, most of the bobbles and wavy lines were me. Clearly this is going to be like learning to weld but instead of "padding" dozens of weld beads across a steel plate I just need to run a lot of seams of stitches. And if I'm going to do much of this I need to find a heavier machine.
Here's how it came out.
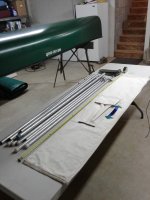
I pleated the pocket (hard to see under bright light with white fabric and no real shadow) and used a a strip of 2" hook and loop under the flap. Note the crooked handle gusset.... Frankly I was surprised that Nancy's 38 year old machine handled the thick canvas seams and webbing as well as it did. I did quickly find out that if I stopped with the needle buried in a seam corner or the webbing gussets I had to lift it free of the fabric by hand or the machine really struggled with restarting-no surprise there, ehh?
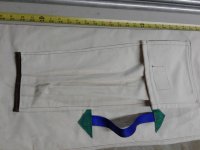
And the pocket with sixteen 12" pins in it.
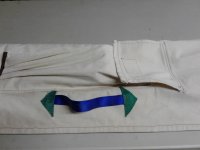
Here is the one design thing I may have to change. The drawstring sleeve is too tight for the elastic cord due to the stiff fabric as it won't collapse enough to close the bag. I'll likely need to open that seam and make a bigger sleeve and switch to 4 or 5mm accessory cord to get the opening to bunch up enough as the narrow tunnel is aggravated by the cord stretching instead of the fabric bunching up. Once I figure out what size cord it will have as the permanent cord I'll get a cord lock for it.
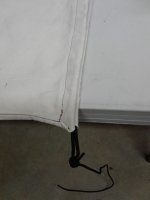
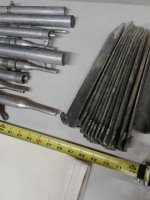
There is a guy a little over an hour from me with 9 or 10 industrial Singer straight stitch compound feed machines that are priced pretty reasonably. They are made for medium to heavy fabric and I may get one to spare Nancy's machine the abuse of heavy stuff. I eventually want to make us a set of portage packs and spray covers for our canoes but I will need a lot of practice before attempting something as visible as a spay cover.
I think a packcloth cover for the reflector oven is next up. And some paddle bags. And Dutch oven tote bags for our camp ovens. And I have at least a half dozen climbing ropes that could use rope bags. And maybe thwart bags. And.....
Best regards to all,
Lance
I have a good sized heavy canvas tarp that saw a lot of years of use as a dining fly for scout and family camping. In fact it still gets used for drive up camping and such. But my pole bag has gotten pretty rough. It was after all made from lightweight tent canvas 25-30 years ago.....
One of the canvas' I had is natural color 72" wide 10 ounce canvas so I looked at what I'd change from the old bag and added some length, width and a stout pocket to hold the 16 or so 12" GI surplus aluminum pins I tote around with the tarp.
I used what I had on hand so the handle is a piece of 1" climbing tubular nylon, the handle gussets were cut from 1-1/2" canoe seat webbing with a hot knife, the drawstring is a stout elastic cord I had on hand etc. The side pocket has some pleats as one end of the pins is a lot wider than the other and the pocket has extra length to hold some extra guy lines etc.
I used a size 90/14 needle with heavy polyester thread and it wanted to wander as it stitched due to flexing in the needle and the needle shaft of my wife's sewing machine but truthfully, most of the bobbles and wavy lines were me. Clearly this is going to be like learning to weld but instead of "padding" dozens of weld beads across a steel plate I just need to run a lot of seams of stitches. And if I'm going to do much of this I need to find a heavier machine.
Here's how it came out.
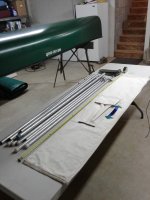
I pleated the pocket (hard to see under bright light with white fabric and no real shadow) and used a a strip of 2" hook and loop under the flap. Note the crooked handle gusset.... Frankly I was surprised that Nancy's 38 year old machine handled the thick canvas seams and webbing as well as it did. I did quickly find out that if I stopped with the needle buried in a seam corner or the webbing gussets I had to lift it free of the fabric by hand or the machine really struggled with restarting-no surprise there, ehh?
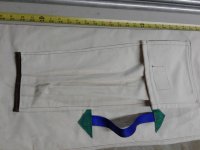
And the pocket with sixteen 12" pins in it.
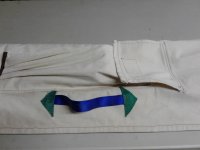
Here is the one design thing I may have to change. The drawstring sleeve is too tight for the elastic cord due to the stiff fabric as it won't collapse enough to close the bag. I'll likely need to open that seam and make a bigger sleeve and switch to 4 or 5mm accessory cord to get the opening to bunch up enough as the narrow tunnel is aggravated by the cord stretching instead of the fabric bunching up. Once I figure out what size cord it will have as the permanent cord I'll get a cord lock for it.
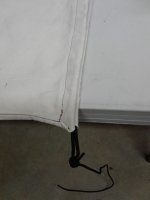
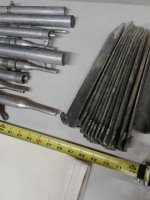
There is a guy a little over an hour from me with 9 or 10 industrial Singer straight stitch compound feed machines that are priced pretty reasonably. They are made for medium to heavy fabric and I may get one to spare Nancy's machine the abuse of heavy stuff. I eventually want to make us a set of portage packs and spray covers for our canoes but I will need a lot of practice before attempting something as visible as a spay cover.
I think a packcloth cover for the reflector oven is next up. And some paddle bags. And Dutch oven tote bags for our camp ovens. And I have at least a half dozen climbing ropes that could use rope bags. And maybe thwart bags. And.....
Best regards to all,
Lance
Attachments
Last edited: