- Joined
- Aug 10, 2018
- Messages
- 1,596
- Reaction score
- 2,355
As part of my plans, I'll need to be able to tilt this hull (before glassing the exterior) 90 degrees or so (side-to-side) and I lack the space to tilt the strongback as Jim does so I needed to devise something that would allow me to rotate it in place. I also wanted to make it removable as every hull is unlikely to get this treatment so a stationary SB is still likely to be ok under normal circumstances.
With 3/4 inch plywood forming the SB and 1/2" OSB above, I endeavored to find the center of balance and theorized that it would not be too far below the top of the SB. I measured & marked the center of the beam and screwed on a flange that will accept 3/4 inch black iron pipe.

Then, staying somewhat true to my automotive background, I grabbed a couple of 6 ton jackstands, removed the rams and replaced them with some 5/4 x 1 3/4 inch scraps (Sassafras left over from paddle making in this case but anything would work). I marked and cut out a notch in the top
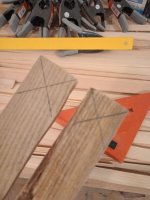
inserted them in the jack stands, lifted them (slightly) off of the floor and installed a couple of screws to act as stops so that the weight of the SB would be transferred to the base of the jack stands. I also used some paddle scraps to act as wedges to secure the new rams
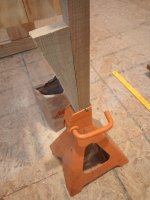
I traced the footprint of the SB with sharpie so that I could land it in the same spot, inserted 6 inch pipe nipples into each flange...
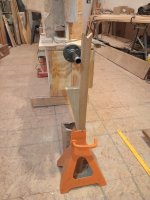
and lifted the SB onto the improvised jack stands. I'll need to tweak a little to better center the weight on the jack stand base (as it stands, the pivot is almost wide of the edge of the base and that's a bit precarious IMO) but I'm very pleased that the experiment went as well as it did on the first try and that, with about 3 inches of lift, I did not need to remove the feet from the SB
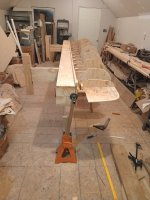
The SB rotated easily in place with enough room to walk around it on both sides and, when lowered back onto the floor, I rechecked and everything was still level & plumb.
I'll adjust the jack stand arrangement tomorrow to keep it centered and I should be ready to start stripping. With one week until enforced social distancing during radiation treatment, I'm very hopeful that I'll be ready to glass this hull by March 5th when I'm, again, cleared for human contact.
The reason that I need this rotation will, hopefully, be evident at that time.
With 3/4 inch plywood forming the SB and 1/2" OSB above, I endeavored to find the center of balance and theorized that it would not be too far below the top of the SB. I measured & marked the center of the beam and screwed on a flange that will accept 3/4 inch black iron pipe.

Then, staying somewhat true to my automotive background, I grabbed a couple of 6 ton jackstands, removed the rams and replaced them with some 5/4 x 1 3/4 inch scraps (Sassafras left over from paddle making in this case but anything would work). I marked and cut out a notch in the top
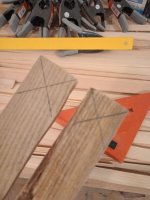
inserted them in the jack stands, lifted them (slightly) off of the floor and installed a couple of screws to act as stops so that the weight of the SB would be transferred to the base of the jack stands. I also used some paddle scraps to act as wedges to secure the new rams
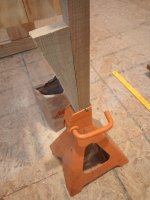
I traced the footprint of the SB with sharpie so that I could land it in the same spot, inserted 6 inch pipe nipples into each flange...
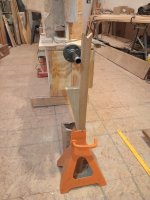
and lifted the SB onto the improvised jack stands. I'll need to tweak a little to better center the weight on the jack stand base (as it stands, the pivot is almost wide of the edge of the base and that's a bit precarious IMO) but I'm very pleased that the experiment went as well as it did on the first try and that, with about 3 inches of lift, I did not need to remove the feet from the SB
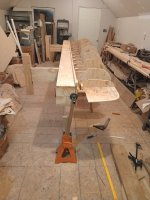
The SB rotated easily in place with enough room to walk around it on both sides and, when lowered back onto the floor, I rechecked and everything was still level & plumb.
I'll adjust the jack stand arrangement tomorrow to keep it centered and I should be ready to start stripping. With one week until enforced social distancing during radiation treatment, I'm very hopeful that I'll be ready to glass this hull by March 5th when I'm, again, cleared for human contact.
The reason that I need this rotation will, hopefully, be evident at that time.