- Joined
- Jul 25, 2012
- Messages
- 838
- Reaction score
- 8
There may come a time when you need to make an axe or hunting knife sheath. Maybe it got lost or damaged or perhaps it wasn't much good at the start. Anyway here is how I go about doing a sheath. Just about all my work in leather has been done with Tandy Leather and tools; there may be other sources of supply, I just don't know of them. I'm sure there are better ways to work leather but this one works for me.
The words that go with a photo are printed under it, just so we're clear. I'll try to limit the blab but some will be required.
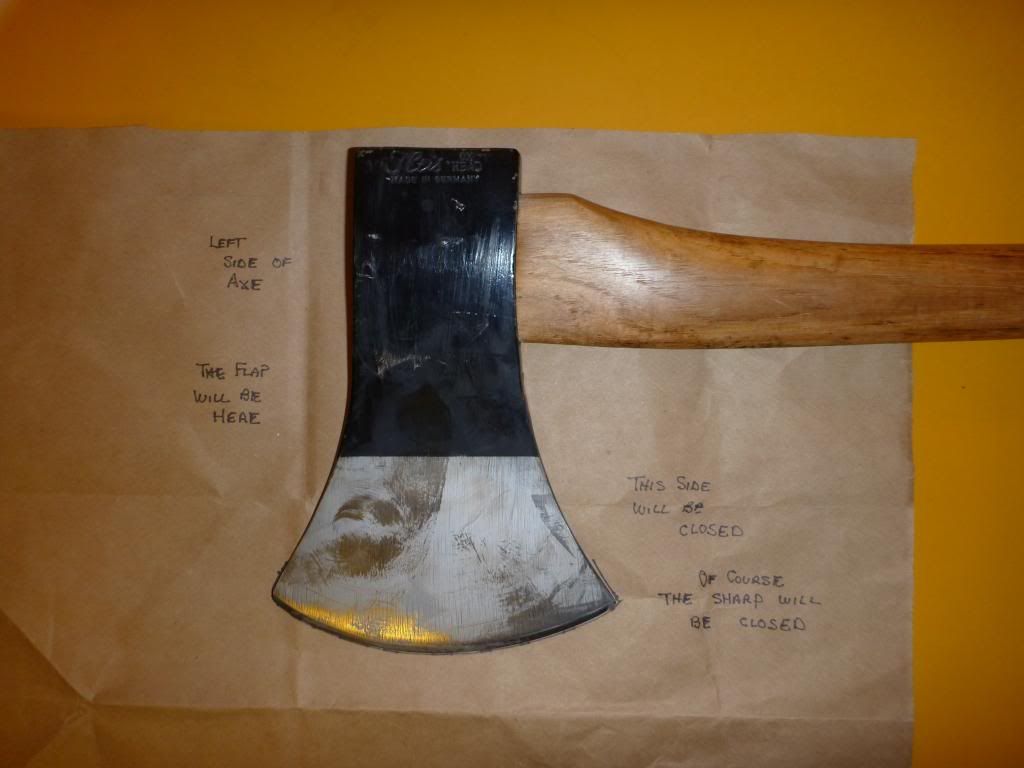
Here is the axe we will be working on. The pattern is made from a brown paper bag, this is the left side of the axe and a pattern has been made of the right as well. Notice the curves on the sides of the axe, they will present some problems for us.

The left and right patterns have been matched up and stapled across the sharp and also one on the lower edge. What we're making is a "pocket" where the axe can be positioned and we can start defining where the sheath will go and what is extra and can be trimmed off.
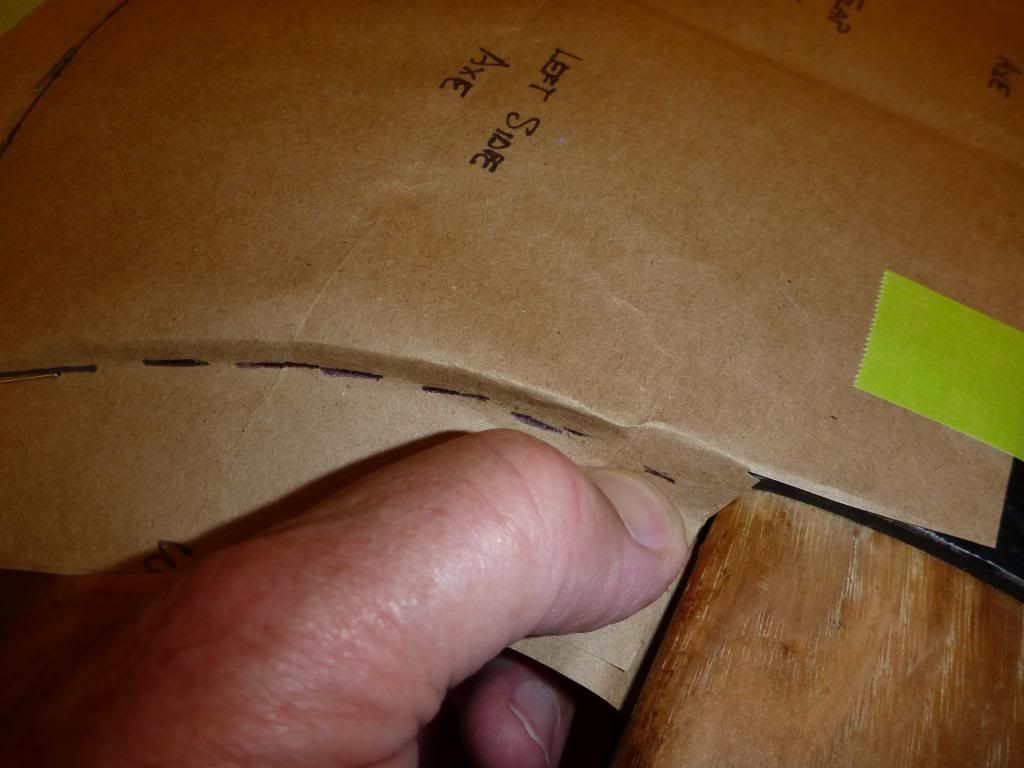
Study the photo, it may be a little confusing. That's my left thumb nail pressing the paper closed to what will be the bottom closed part of the sheath. I'm trying to get the crease to fall half way, some from each side. Left and right, then marked with those black dashes. The paper where I'm squeezing will be where the stitching will be in the leather to hold it closed. I've marked both left and right sides.
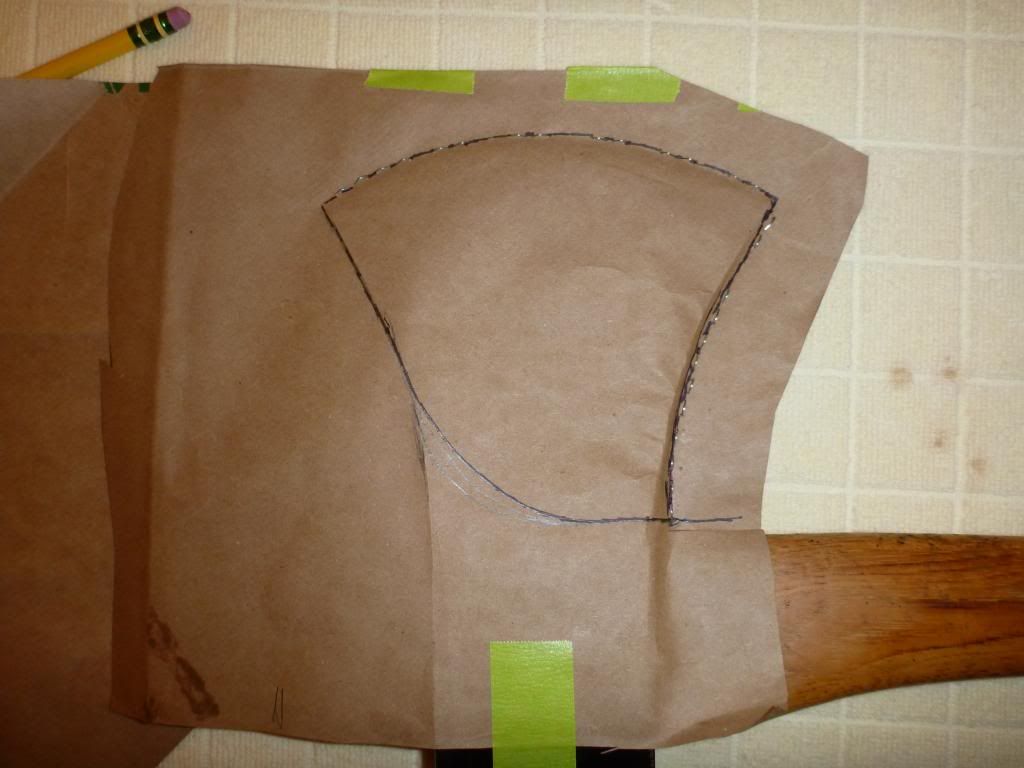
Now we can see progress! We're looking at the right side of the axe; you can see that the bottom edge where we were pinching it is now stapled closed. I've marked a graceful line that will be the top edge of the right hand side. That green tape is holding the axe snug in the "pocket" we made with the staples.
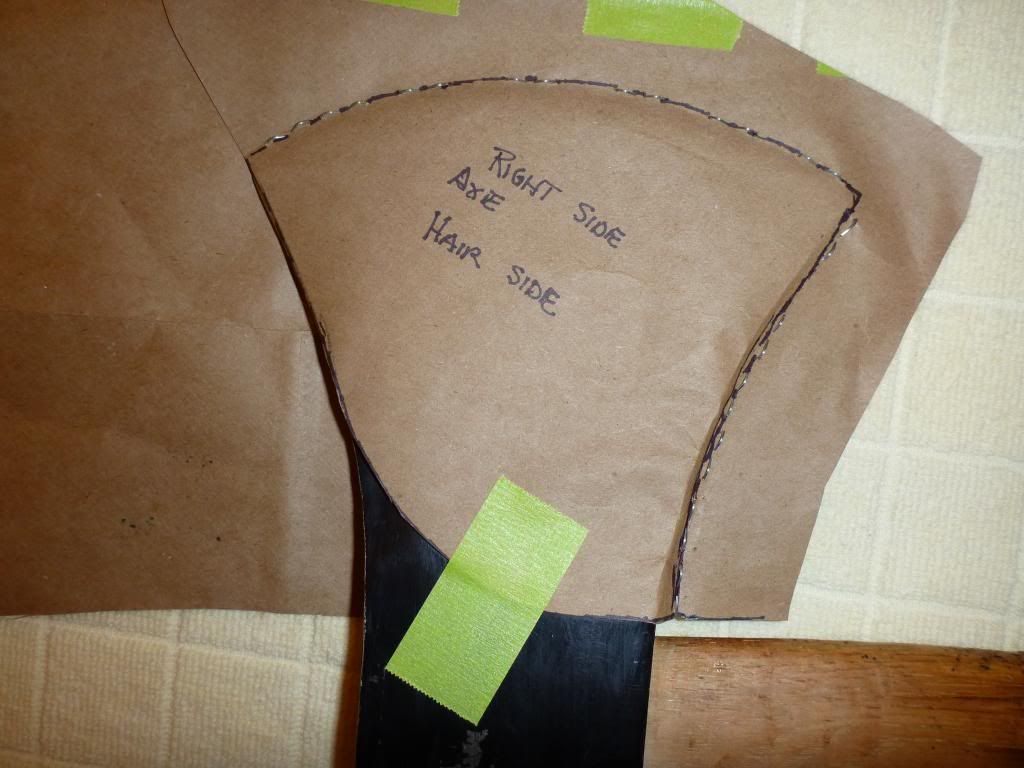
The excess has been cut off and the pattern has been labeled. Leather has two sides "hair" and "flesh". I always over do labels, but it's so easy to get screwed up and cut the leather the wrong way. $$$$ down the tube!
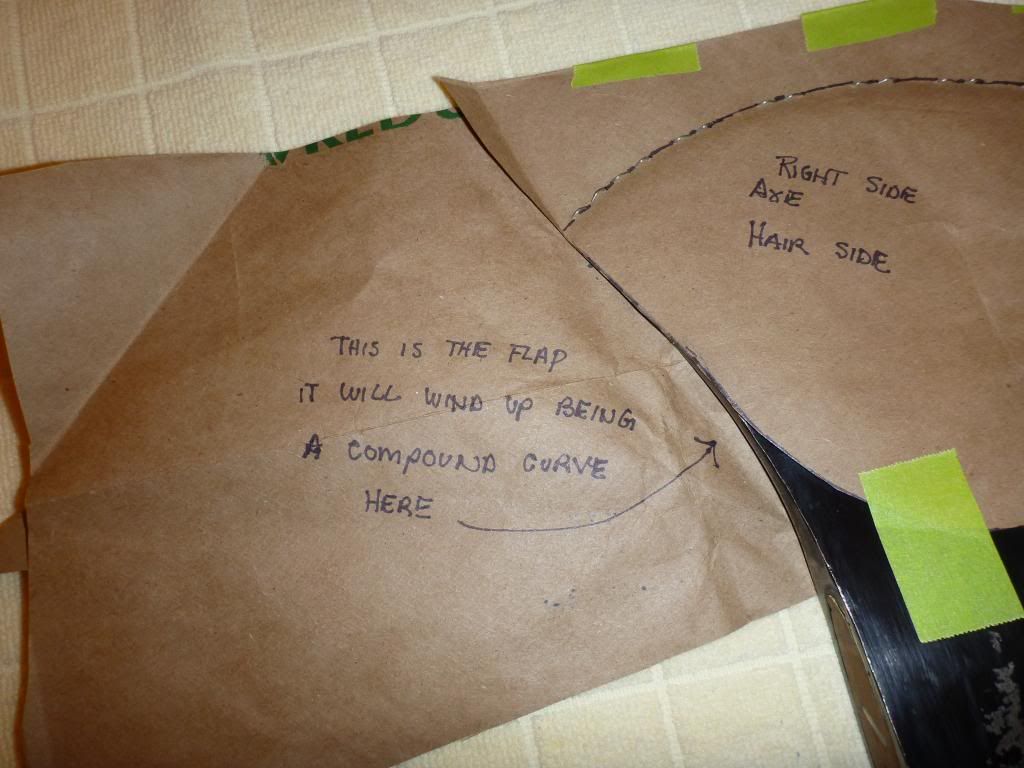
You see my note about the compound curve: all the leather I've used has a unique property. When you want the leather to mold to the article, in this case an axe, if you wet it, it becomes moldable. Think of strong wet cardboard crossed with really stiff modeling clay. That's maybe close. I'm guessing here but maybe the fibrous layers deep in the hide are able to move some when wet. Now once it's dry the hide will retain the molded impression pretty well.
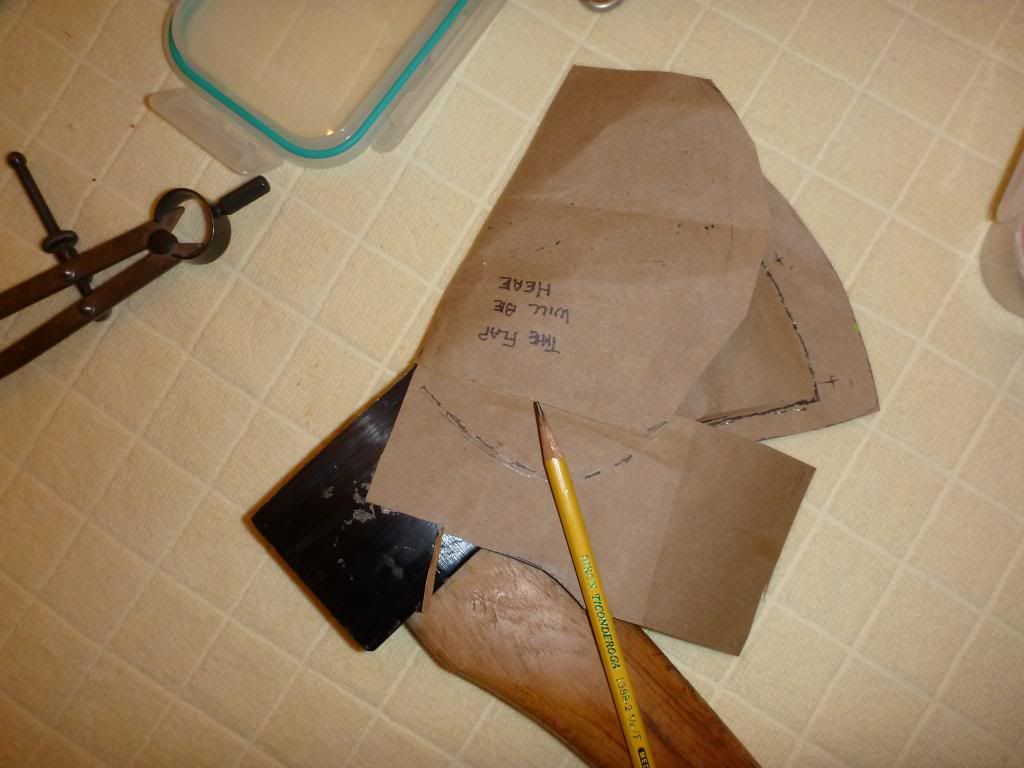
That's the flap but it won't mold for beans, it's just paper. Right by the pencil point I glued on some more paper, I cut off too much and when we get to the real leather I don't want to come up short for the flap.
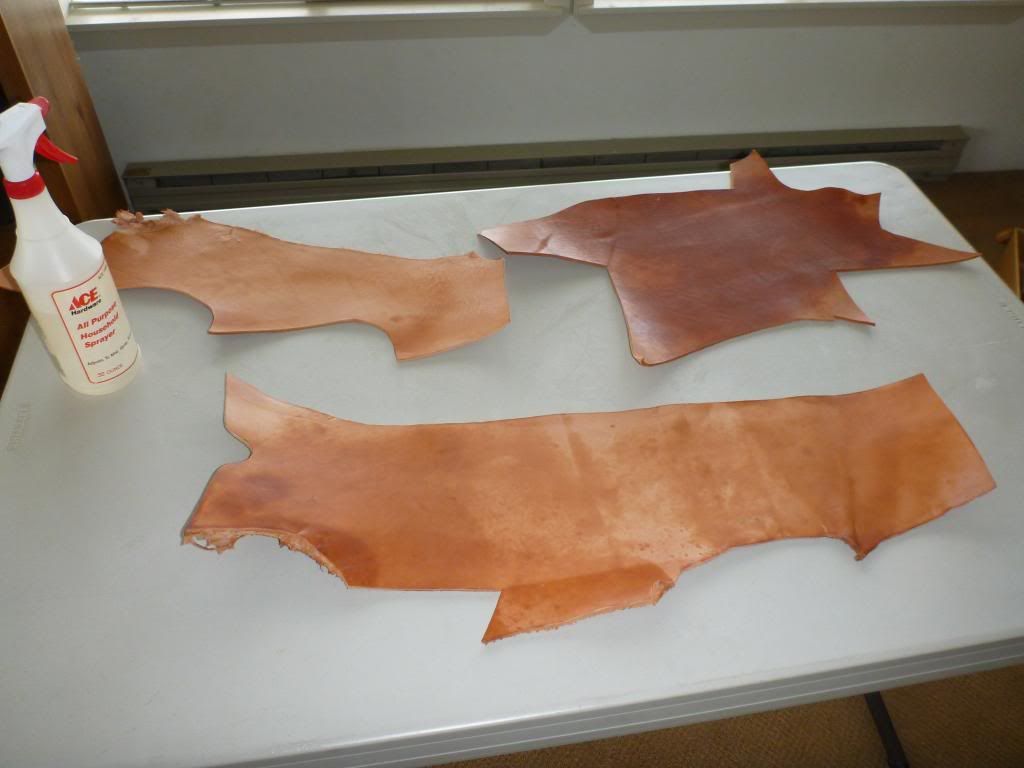
This is the leather I've got to pick from; it was tied up in a roll so I sprayed a little water on it to get it to lay flat. I didn't buy the best and it's been picked over from other projects. I really need to look at both sides and see what imperfections I can work around and what must be avoided. Leather comes in Backs, Sides and Belly. By and large backs are the very best. Then sides. Maybe for your first projects you might try some really good leather; it would be just one less thing to worry about.
Now I'm going to pause here and post this off to the site. I'll start in again right away but I've lost everything three times so far and really get cranky when it happens.
Rob
The words that go with a photo are printed under it, just so we're clear. I'll try to limit the blab but some will be required.
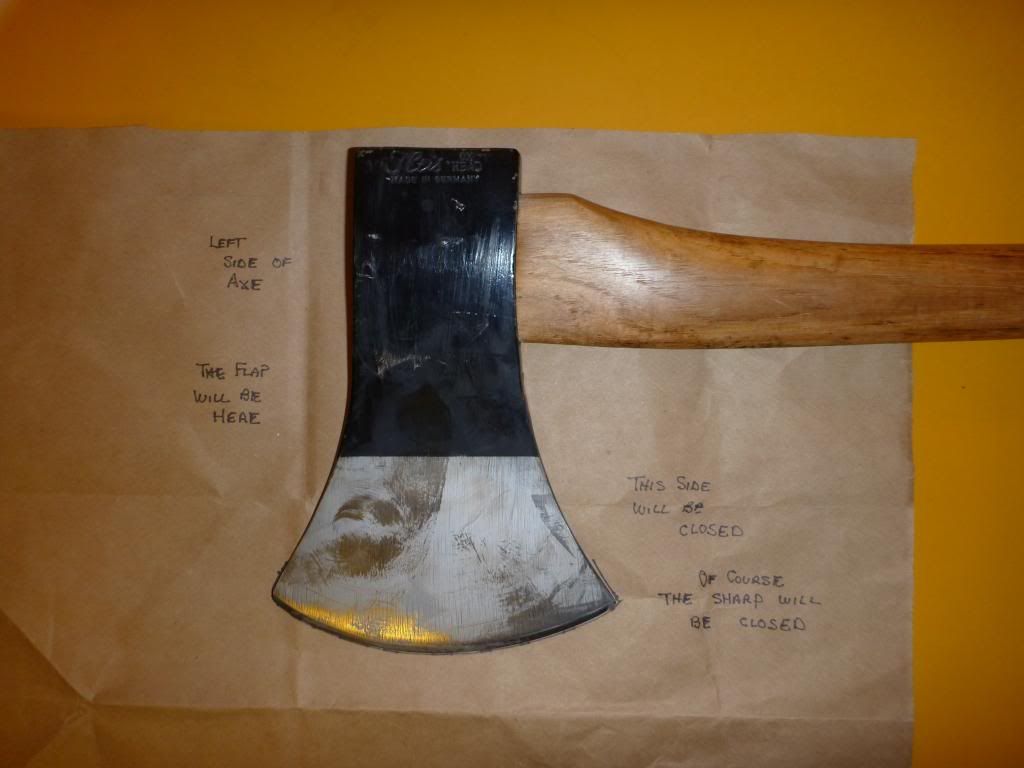
Here is the axe we will be working on. The pattern is made from a brown paper bag, this is the left side of the axe and a pattern has been made of the right as well. Notice the curves on the sides of the axe, they will present some problems for us.

The left and right patterns have been matched up and stapled across the sharp and also one on the lower edge. What we're making is a "pocket" where the axe can be positioned and we can start defining where the sheath will go and what is extra and can be trimmed off.
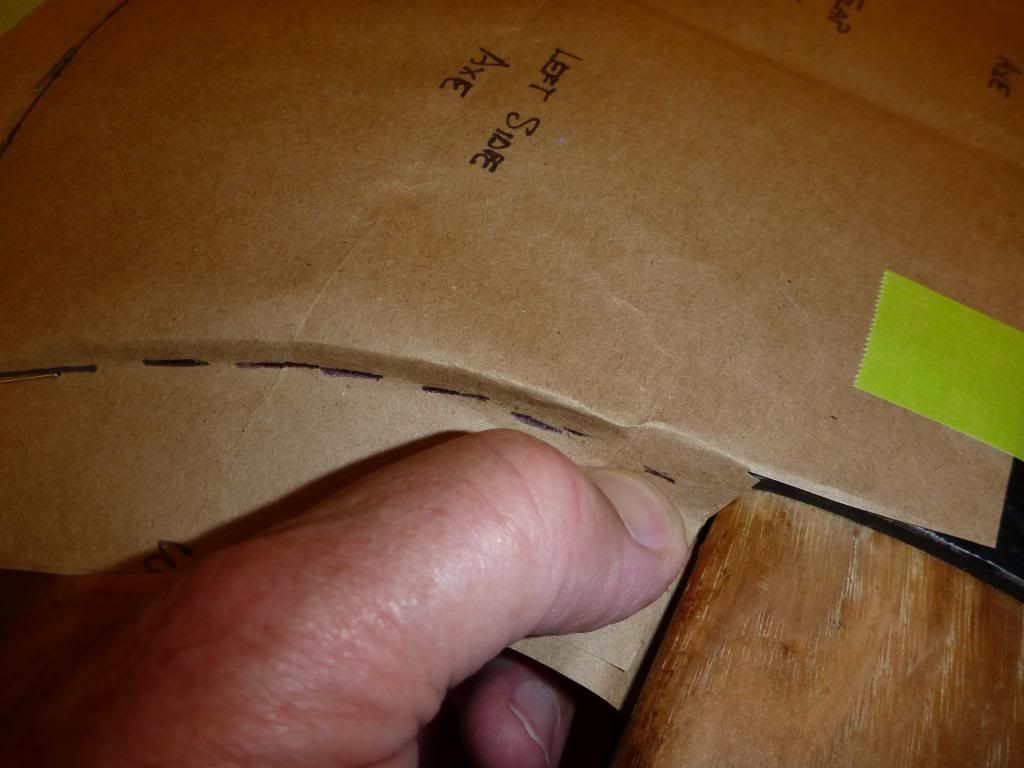
Study the photo, it may be a little confusing. That's my left thumb nail pressing the paper closed to what will be the bottom closed part of the sheath. I'm trying to get the crease to fall half way, some from each side. Left and right, then marked with those black dashes. The paper where I'm squeezing will be where the stitching will be in the leather to hold it closed. I've marked both left and right sides.
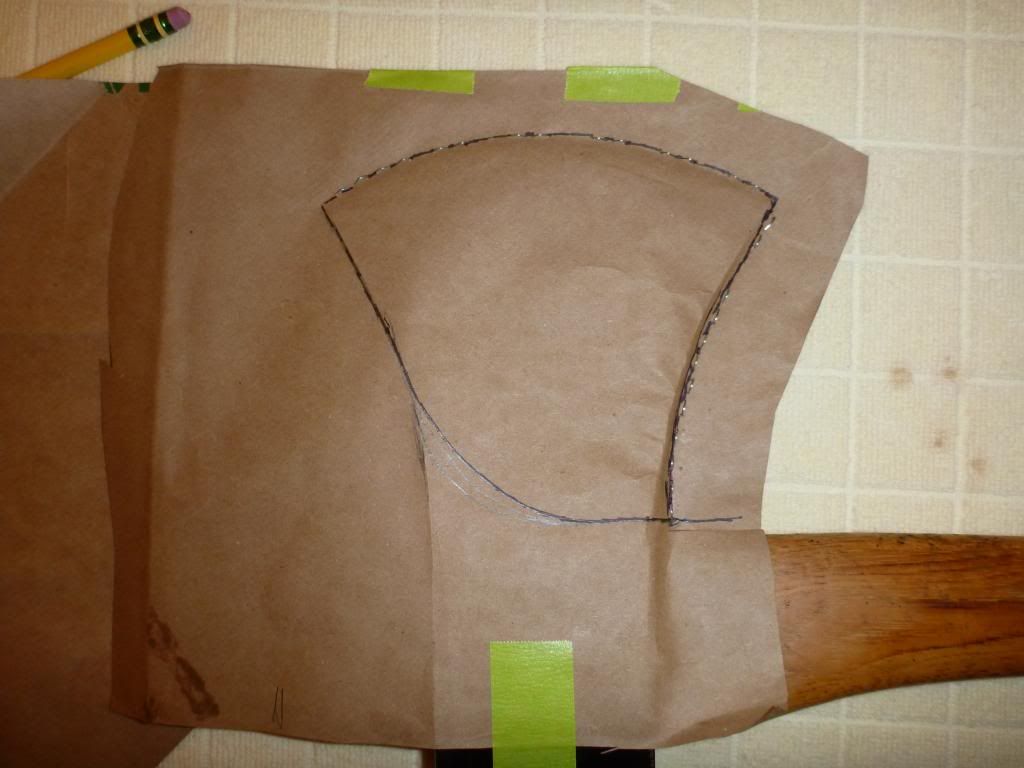
Now we can see progress! We're looking at the right side of the axe; you can see that the bottom edge where we were pinching it is now stapled closed. I've marked a graceful line that will be the top edge of the right hand side. That green tape is holding the axe snug in the "pocket" we made with the staples.
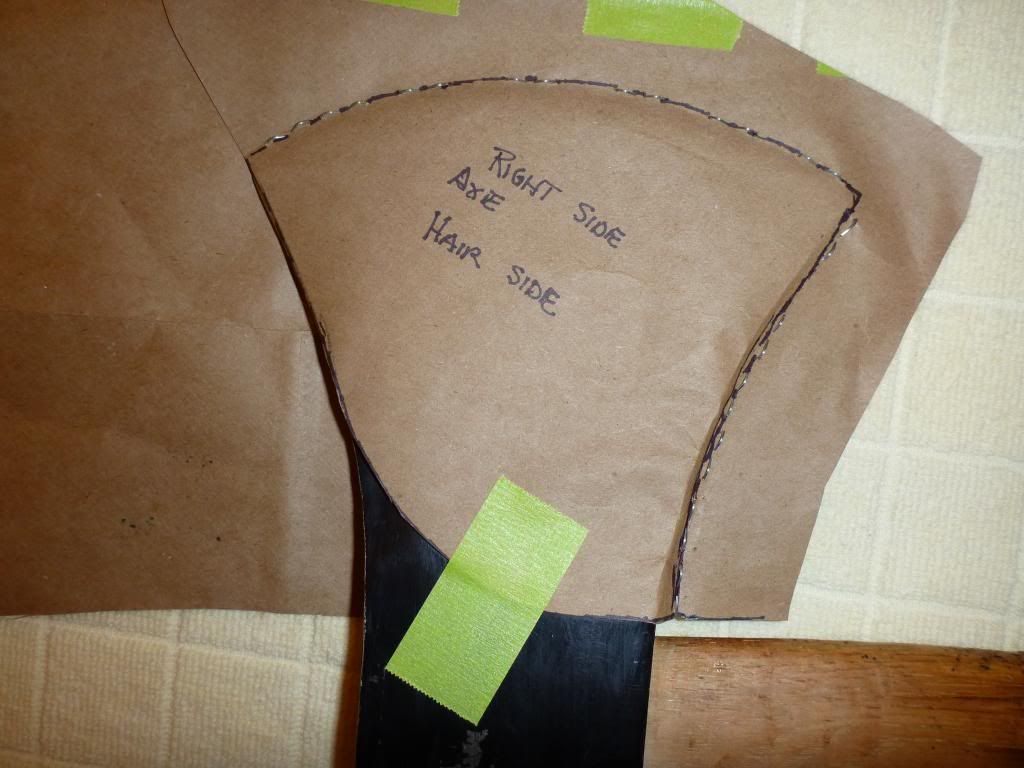
The excess has been cut off and the pattern has been labeled. Leather has two sides "hair" and "flesh". I always over do labels, but it's so easy to get screwed up and cut the leather the wrong way. $$$$ down the tube!
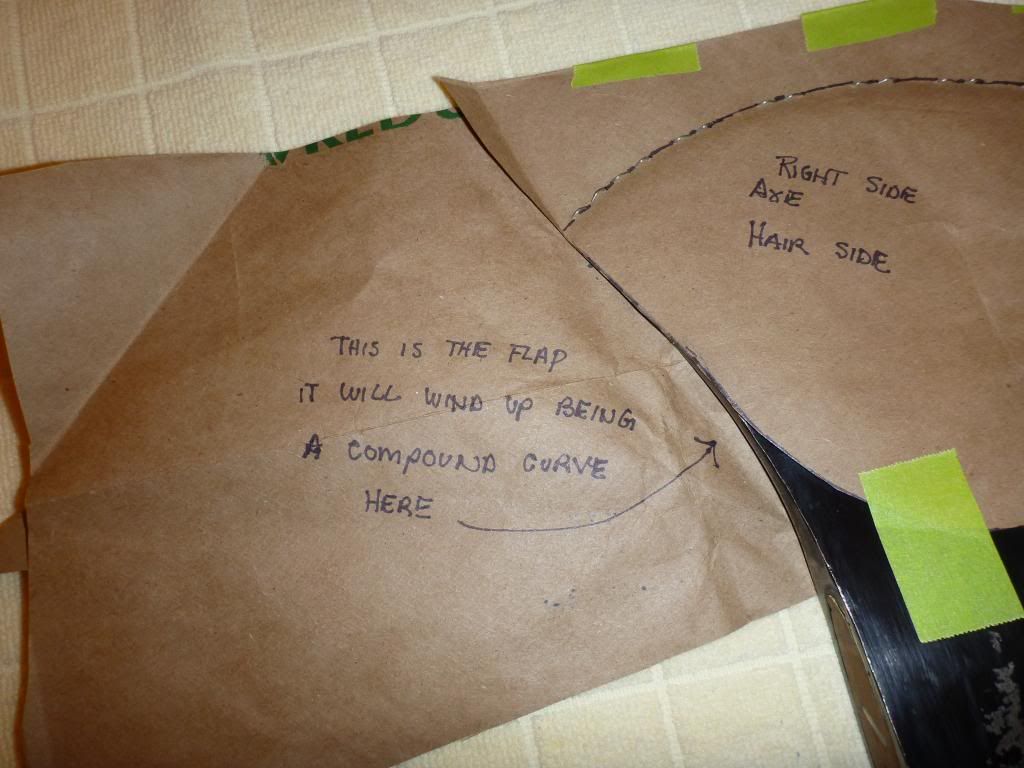
You see my note about the compound curve: all the leather I've used has a unique property. When you want the leather to mold to the article, in this case an axe, if you wet it, it becomes moldable. Think of strong wet cardboard crossed with really stiff modeling clay. That's maybe close. I'm guessing here but maybe the fibrous layers deep in the hide are able to move some when wet. Now once it's dry the hide will retain the molded impression pretty well.
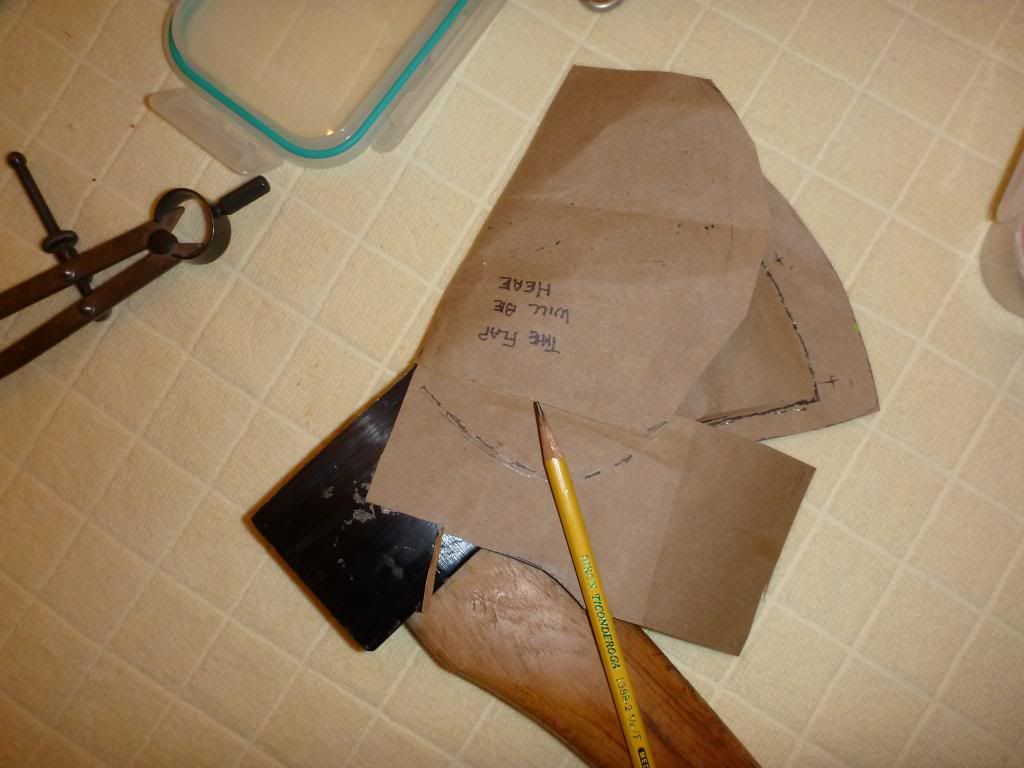
That's the flap but it won't mold for beans, it's just paper. Right by the pencil point I glued on some more paper, I cut off too much and when we get to the real leather I don't want to come up short for the flap.
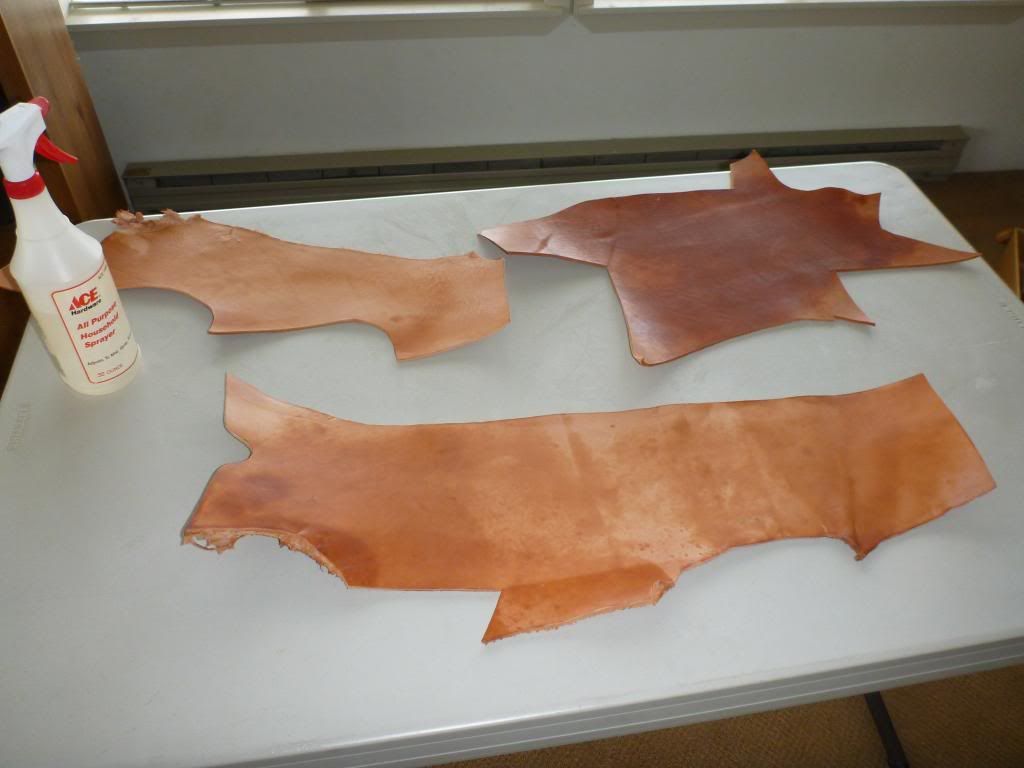
This is the leather I've got to pick from; it was tied up in a roll so I sprayed a little water on it to get it to lay flat. I didn't buy the best and it's been picked over from other projects. I really need to look at both sides and see what imperfections I can work around and what must be avoided. Leather comes in Backs, Sides and Belly. By and large backs are the very best. Then sides. Maybe for your first projects you might try some really good leather; it would be just one less thing to worry about.
Now I'm going to pause here and post this off to the site. I'll start in again right away but I've lost everything three times so far and really get cranky when it happens.
Rob